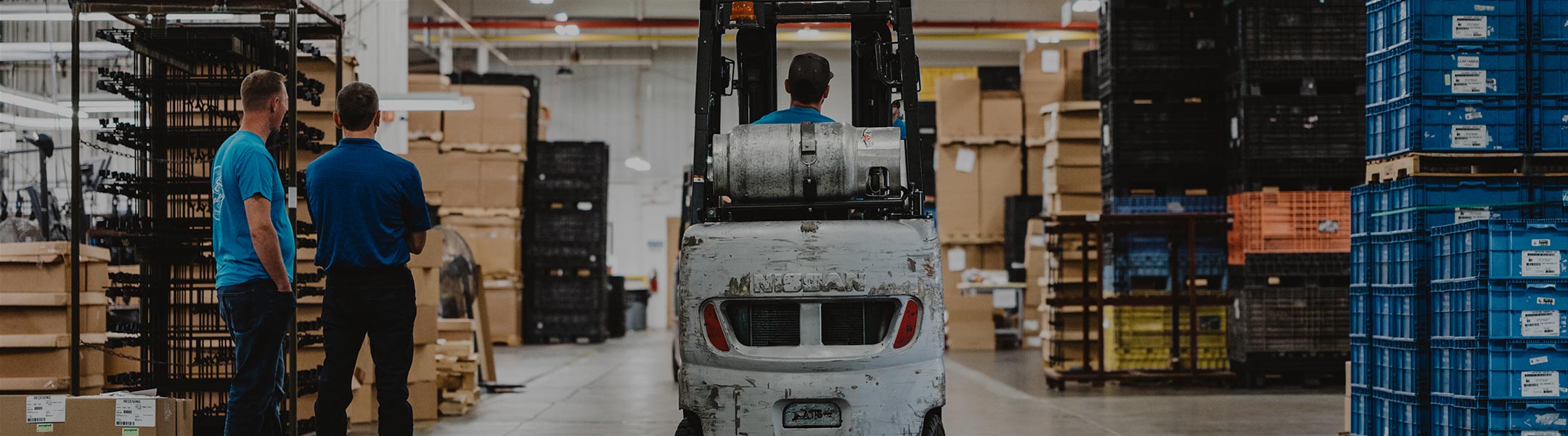
Get your copy of the 7th Annual State of Smart Manufacturing and hear from 300+ manufacturers in this new survey report!
For a monthly digest of expert insights, data points, and tips like the ones in this article.
Bumps, clanks, hisses, and creaks. What’s that noise?
In a manufacturing operation, just like a Halloween movie, these sounds are always scary. But sometimes, we don’t hear the sounds until they’ve jumped out at us, eliciting a haunted-house scream and a bit of embarrassment that we didn’t see it coming.
Manufacturing companies using traditional production tracking and manual data collection may think their quality, manufacturing processes, and production performance are excellent. Using a simplistic “If it isn’t broke, don’t fix it” approach, they feel that if they don’t hear the noise, all is well.
Unfortunately, this is both literally and figuratively true. Broken processes and siloed data have been the cause of more than enough zombie groans among planners and werewolf howls among purchasing managers and finance execs.
Manual data collection, data entry, and analysis can hide many problems. Like the ghouls and ghosts on Halloween night, these problems plague managers with their own creepy effects. Data entry errors, siloed data, information bias, inefficient processes, bottlenecks, and missing information can lead staff to believe that things are fine when suddenly…they aren’t.
A smart manufacturing platform allows you to find these threats before they have a chance to make noise and cause harm. With real-time or near real-time data and analysis, light is thrown onto hidden problems so operators, technicians, and managers can address issues as or before they arise.
There are several ways a smart manufacturing platform can relieve fears and help fix what’s broken while improving efficiency and performance.
Paper-based factory monitoring is severely limited. Besides being error-prone, a busy plant floor may leave out information altogether. Paper-based systems limit a staff’s ability to move forward with agility too. Like a mummy wrapped so tight they can only shuffle, paper monitoring systems that try to add more layers only slow mobility and turn the shuffle into a fall.
With a smart manufacturing platform, data collection is automatic and error-free. Cloud-based analytics deliver unsiloed actionable insights to those who need it to improve processes, reduce bottlenecks, and improve efficiency, productivity, and OEE.
Production and quality management teams will have access to the data they need in a way that empowers action. Instead of adding more paper to an already mummified system, unwrap the mummy with automated data collection and factory monitoring. Turn your factory floor into an agile, paperless, data-driven environment.
When problems you didn’t even know existed pop up on the factory floor, customers become the villagers with torches and pitchforks. Traditional manual data tracking for production and quality are like Frankenstein’s monster.
Companies stumble along using disparate, unconnected software that relies on siloed data. Each piece multiplies the effects of error-prone and biased data until the output of each system and the lack of communication create an oddly assembled monster that plods along.
A smart manufacturing platform lets you disassemble the monster. Instead of separate pieces forming an inefficient production floor, a single version of truth using common standardized data emerges. Process improvements have an immediate impact, resulting in a sleek, efficient system that scares no one.
A sudden shift in demand causes bottlenecks that slow production and increase scrap and rejects. A missed spec change can cause entire lots to be scrapped. When this happens, the effect is the same as the full moon that triggers a werewolf’s howl. Execs, distributors, customers, and even media howl at the disaster, and no amount of wolfsbane can help.
Fortunately, a smart manufacturing platform is like a silver bullet. Production tracking software significantly improves production processes and efficiency. It also helps drive quality improvement throughout the organization.
Automated data collection in a smart manufacturing platform helps teams undertake root cause analysis. As problems are identified, accurate and improved work procedures are easily deployed and accessible in real-time to prevent missed spec changes from having an effect. As actionable insights transform the production floor, teams are better trained and prepared for problems as an improved quality culture takes hold, silencing the werewolves for good.
Your Halloween can be all treats and no tricks when you’ve got a leading smart manufacturing platform at your fingertips. With complete visibility, improved communication, optimized processes, and higher efficiency and productivity, your team will finally put a rest to the things that go bump in the night, unlock hidden capacity, and significantly improve quality. Take the screams out of your plant floor and save them for your horror-movie marathons instead.
To discover how one company fixed what was broken and achieved 412% ROI with Plex, click here for the case study.