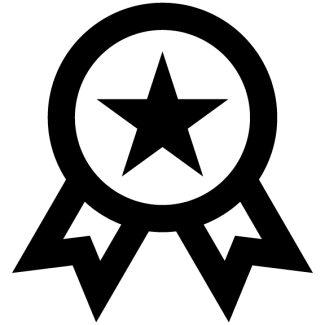
Get your copy of the 7th Annual State of Smart Manufacturing and hear from 300+ manufacturers in this new survey report!
Plex Quality Management System (QMS) helps process and discrete manufacturers meet strict industry and customer compliance with a closed-loop digital system of record.
through in-line quality, clear reporting, and simple audit tracking.
with quality documentation available real-time – digitally – across the enterprise.
with on-time delivery performance, improved supplier management, and increased customer satisfaction.
Plex QMS uniquely supports closed-loop quality from a “Plan-Do-Check-Act” perspective, enabling continuous improvement of quality processes.
Making quality management inherent to your workflows and processes reduces quality loss and risk of warranty issues or recalls, improving your brand reputation and customer relationships. With Plex quality requirements and documentation are available and shared in real-time across the enterprise.
Plex helps you generate process control plans with detailed inspection instructions and digital checksheets that are closely integrated with product specifications. You can manage and track documents such as engineering and material specifications, or recipes to maintain a detailed list of compliance requirements. And regulatory compliance (APQP, FSA, HACCP, FSMA, SQF) is supported easily across workflows.
Finally go paperless with electronic checksheets that validate quality and process control in real time to ensure that execution proceeds as planned. You can establish and maintain a detailed list of product specifications and characteristics to inspect.
Plex allows you to collect in-process inspection data for statistical process control (SPC) and view data visualizations. You can perform capability studies, dock audits, dimensional layouts, first-piece and final inspection sheets, and any other user-defined checks. You can automatically complete statistical calculations such as standard deviation and process capability (Cp/Cpk). Plex makes it possible to connect electronic gages and weigh-scales to eliminate manual data entry of dimensional measurements.
Achieve and retain quality certifications with best-in-class functions that provide auditors with instant evidence of compliance. Plex helps ensure that you meet quality standards that are crucial for your industry with flexible, user-configurable methodologies. You can also implement continuous improvement processes to manage lean manufacturing initiatives across your facility and involve customers and suppliers through portals.
You can document itemized quality standard requirements within the system and then use a formalized mechanism for review/signoff, audits, checklists, procedures, documentation, and follow-up activities.
Whenever issues are raised within your organization or by suppliers or customers, you can use built-in forms for problem reporting and resolution including common techniques like 8-discipline (8D), “5 Why,” or other corrective action methods to record, track, follow-up on, resolve, and report problems and concerns. You can assign actions needed for containment, correction, and prevention of problem recurrence. For supplier-related problems, the Plex Supplier Portal enables you to collaborate directly with suppliers on waivers or cost recovery.
Plex makes it possible for you to track production defects at the level of the container or individual part and determine products that need to be returned to the supplier. CAPA is integrated with inventory and lot tracking, problem control, supplies, rejections, and general shipping. You can also track approved deviations from control plan dimensions or specifications during the production process.
Plex QMS is designed to provide immediate value for your company, while preparing you for whatever tomorrow brings.
What is Smart Manufacturing?Quality documentation and standards available real-time, digitally – across the enterprise
Quality processes and check sheet data automated and updated in real-time
Quality measured in-line with clear reporting and data access for simple audit tracking
Quality performance available through digital control plans and document control
Quality requirements and documentation are available and shared in real time across the enterprise, making a formalized procedure a breeze.
CAPA is integrated with inventory and lot tracking, supplies, rejections, and general shipping to help you track down to the container or individual part level.
Coordinate quality activities across teams and centralize submission tracking for easy access by customers and suppliers.
In the event of an audit, digital in-line quality management makes it fast and simple to pass audits.
Barrett Petfood Innovations (BPI) has discovered that responding quickly in the case of a recall—real or mock—is a matter of running the business on one cloud-based platform.
Read Blog
"When there’s an anomaly in our production, we see it as an opportunity for us all to improve. Because the reports are so fresh, people don’t have to think back a week or two to remember what happened—we can easily find the source of a problem and work to prevent it from reoccurring."
Jeff Karan
Director of IT, G&W Products
See Case Study
“A major selling point was that we knew Plex could help us with traceability and quality control in general, which was an area for improvement for us. We connected with Plex and began to explore what they had to offer."
Eduardo Arana
Deputy Managing Director, Eurotranciatura Mexico
See Case Study