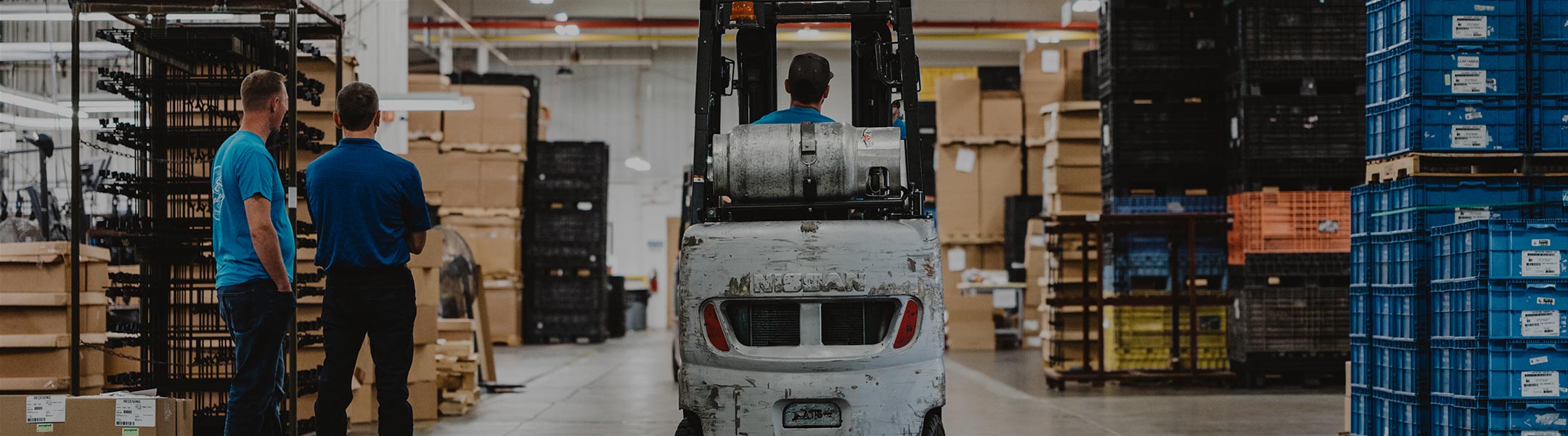
Get your copy of the 7th Annual State of Smart Manufacturing and hear from 300+ manufacturers in this new survey report!
For a monthly digest of expert insights, data points, and tips like the ones in this article.
Everyone knows that poor quality can cause headaches that ripple throughout an organization, but not every manufacturer approaches (or even defines) quality the same way. Quality improvement strategies are as old as manufacturing itself, and yet achieving success in this area continues to be a challenge for many in the industry. Done right, and your quality concerns will be reduced to a minimal and fixable list. Done wrong, and your costs can spiral out of control.
Poor quality in manufacturing goes deeper than just a vague notion of scrap or waste. It can be revealed through obvious visible problems on the production floor, such as:
Manufacturing also has hidden quality costs that are just as damaging, including:
Together with visible costs, these hidden costs account for the total cost of quality.
For both visible and hidden quality costs, quality improvement activities in manufacturing can be designed to reduce and eliminate many of these issues. Here are five steps that will help.
The days of “shooting from the hip” in quality are gone. High volume manufacturing equipment and precision specifications call for standard work in operator and technician tasks. Tools like 5S, kaizen events, and other Lean and Six Sigma methodologies can lead to process improvements that can be documented, standardized, and repeated for consistent operation.
Greater focus on teams can lead to shared maintenance. This practice breaks down the barriers of traditional “us” vs. “them” thinking between operators and maintenance staff. Teams become more interdependent by having operators do some basic maintenance during startup, stop, and changeover, leading to improved equipment conditions.
Like shared maintenance, continuous training means that core skills are constantly being refreshed, reducing the chance of off-quality production. This allows for more effective cross-training and for staff to be trained in identifying and acting upon a problem without producing scrap and without having to wait on others to fix it for them.
Traditional management often results in punitive measures for quality issues. Creating a culture of quality where operators, technicians, and other manufacturing staff are encouraged to point out problems increases buy-in. It helps reveal quality problems that may have gone undetected for more extended periods.
Often, companies will initiate projects to improve quality problems. And one tool for identifying and fixing those problems is root cause analysis. By drilling down to what happened and why, root cause analysis can improve processes that eliminate the quality concern.
The above steps can be included in a robust quality system with well-designed quality assurance protocols and the correct quality control measurements. But to truly drill down into the quality problems plaguing your operation, technology in the form of QMS software is the answer. It’s what takes every step to the next level by leveraging the power of data created at the machine level.
Consider Plex QMS as an example. It helps companies track, analyze, and act using data-driven insights for repeatable and predictable quality. By taking the monitoring and tracking out of the hands of operators and technicians, our software offers digital quality and compliance monitoring to create a closed-loop quality system. It utilizes tools such as PDCA so you can implement continuous quality improvement faster than humans alone can accomplish. Importantly, Plex QMS also offers companies the ability to control operational behavior in real-time while providing tools for issue resolution for corrective and preventive actions. And that’s just a fraction of what’s possible.
If you’re like others, you’re looking to move your quality strategy from a dusty old clipboard filled out yesterday to data-driven reporting on production occurring right now. Move your journey forward by reading about the different types of quality management systems and finding the right one for you.