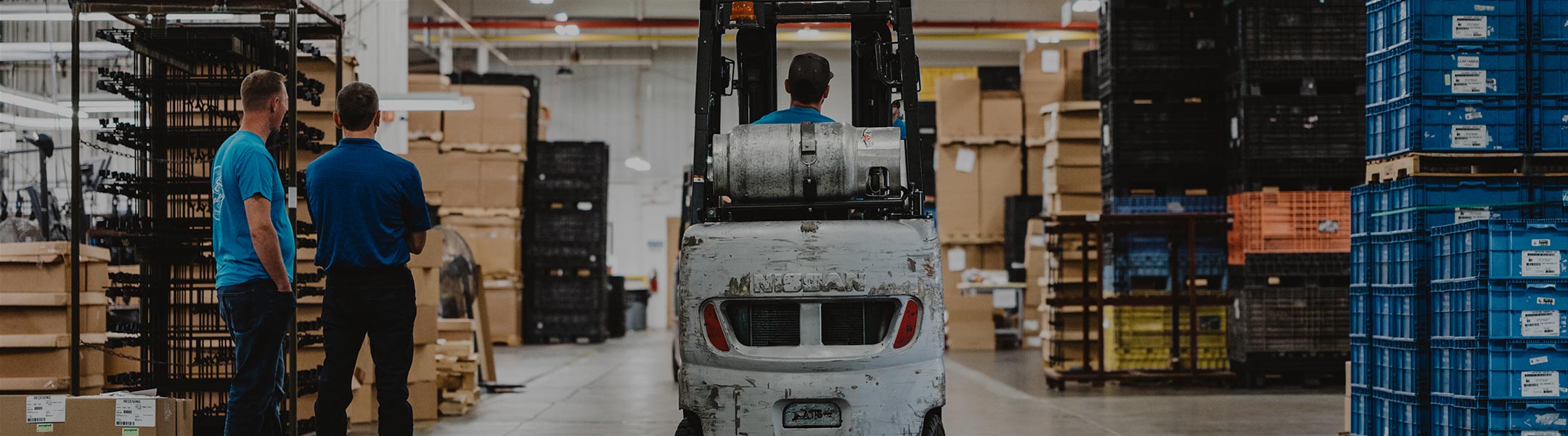
Get your copy of the 7th Annual State of Smart Manufacturing and hear from 300+ manufacturers in this new survey report!
For a monthly digest of expert insights, data points, and tips like the ones in this article.
Manufacturers have a lot of pressure on their shoulders. Traditional software solutions sought to relieve that pressure by automating processes, reducing labor-intensive tasks, and optimizing performance efficiency for specific disciplines.
That system of disparate software worked to improve efficiency - until one day it didn't. So, what changed? The most significant change was the technological leap brought on by IIoT devices and platforms that provided unprecedented amounts of data. These software systems weren’t equipped to handle such a large volume.
It turns out that having too many software systems with siloed data and a lack of interoperability was just a different kind of headache in the age of big data. New tasks (like reconciling quality reports from a QMS system that doesn't speak to an MRP system) were a pain. And this barrier appeared across organizations.
Managers and operators who had previously been tied down by manual management and data entry found themselves piecing together information from unconnected systems to make decisions. The result was a lot like juggling chainsaws. Because in the real world, there are only so many chainsaws that even the best jugglers can keep in the air before disaster strikes.
When business systems aren’t consolidated, there’s a high degree of error. These errors are further compounded as critical data is shuttled from one system to another. The list of disadvantages that arise from systems not being connected or integrated is long, including:
Since optimized business processes mean more profit and higher customer satisfaction, and no one likes juggling chainsaws, today’s smart manufacturing platforms provide structure under a unified data system to eliminate these disadvantages.
Driven by cloud-based analytics and advanced machine learning algorithms, these powerful platforms connect to factory assets to deliver data-driven smart manufacturing with a suite of products like ERP, MES, QMS, SCP, and more. But the platform also lets companies utilize their legacy systems and bring that software under the same umbrella of data within the smart manufacturing platform.
Real-time data is used to let that software perform to its highest capabilities by bridging the operability of a company's disparate software systems. It standardizes and unsiloes data from within different systems and analyzes it to deliver actionable insights. Because everyone uses the same data, information from each department or functional area contributes to that analysis.
Once the smart manufacturing platform is up and running, it lets companies connect their factory assets to a single source of truth. Processes are optimized and automated as analysis empowers better decision-making and fewer errors.
A smart manufacturing platform creates end-to-end visibility and lets users connect from laptops, tablets, mobile devices, and HMIs to speed up response time and drive improvement. Such systems enable complete production visibility, tracking, and asset and machine condition monitoring.
The use cases for a smart manufacturing platform are extensive. Using the Plex Smart Manufacturing Platform, Kendrick Plastics began utilizing the system specifically to consolidate and enhance its internal systems. The results were amazing. In nine months, they consolidated 27 software systems into one comprehensive platform with Plex.
But the system consolidation was only the beginning. With new data from connected IoT devices, the consolidated systems working under the platform enabled them to eliminate 40 hours of data entry while reducing purchase order processing from days to minutes. They also began real-time inventory tracking and significantly lowered new client onboarding via EDI from months to days.
Software has helped many companies improve processes. But in a complex manufacturing environment, data needs a comprehensive system that breaks down silos and delivers actionable analysis across the enterprise.
The Plex Smart Manufacturing Platform can help you stop juggling chainsaws and empower your production floor to realize the same level of improvement we shared above. You can utilize the entire platform or individual elements like MES, QMS, and more to consolidate your system and take your operation to the next level.