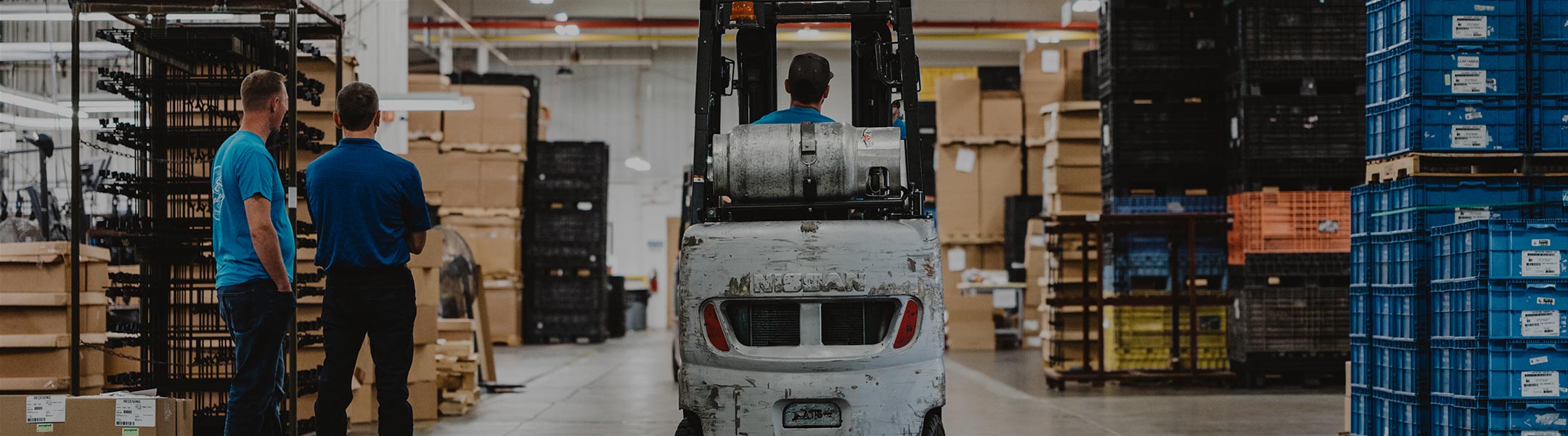
Get your copy of the 7th Annual State of Smart Manufacturing and hear from 300+ manufacturers in this new survey report!
For a monthly digest of expert insights, data points, and tips like the ones in this article.
Meeting customer demand, maintaining regulatory requirements, and competing in a global market all hinge on one critical aspect of your manufacturing business: product quality.
Given the high stakes, it’s no wonder organizations are increasingly turning to quality management systems (QMS) that can help them sustain high performance levels while reducing costs and finding efficiencies. As you seek out the right QMS for your organization, one that can unlock new capabilities and maximize the return on your investment, think through these six steps to quality management success.
Using paper-driven document management and manual processes has a hefty disadvantage — it can quickly lead to outdated information and unchecked errors. Spreadsheet-based quality control lacks the benefits that today’s digitized systems can deliver: continuous improvement of your operations while meeting customer requirements. Imagine being able to connect, automate, track, and analyze your data. Digitizing your quality processes introduces an elevated level of control that more closely aligns with industry standards. A digitized QMS helps you keep up with increasing product complexity while maintaining compliance and certifications.
Making quality management inherent to your workflows and processes reduces quality loss and risk of warranty issues or recalls, improving your brand reputation and customer relationships. A QMS boosts how well your processes are adopted, executed, and continuously improved. Digitizing your data means your enterprise can coordinate quality activities cross-functionally by using a single source of information. Quality requirements and documentation are available and shared in real time across the enterprise, whether you have one location or a multitude across the globe.
The goal: quality management that is predictable, repeatable, and actionable. Use your QMS to not only operationalize compliance efficiently, but also inherently error-proof production operations. This helps meet industry standards and customer regulations and means you can ensure compliance on a more consistent basis. Consistency doesn’t eliminate the ability to be flexible, however. A strong QMS can offer configurable compliance methodologies as your needs and your customers’ needs evolve and change.
Having the right data at your fingertips creates a host of opportunities. The information generated by a QMS can enable important lean manufacturing initiatives and quality assurance across your facility — the more you learn, the more you can improve. Continuous improvement cycles with integrated quality standards and processes in a digital system of record help drive and maintain quality. Use it to strengthen your company’s commitment to quality and having a reputation for high standards, as well as to collaborate with your customers and suppliers to achieve best practices.
A QMS centralizes quality information and documents, putting the right information in the right hands at the right time. Proper quality management connects information with people and allows fast and agile reactions to opportunities and obstacles. For example, you can go paperless with electronic check sheets that validate quality and process control in real time, ensuring that execution proceeds as planned. Knowledge is power — having data that is collected at each manufacturing moment in the context of your enterprise-wide goals and metrics results in data-driven insights, more accurate quality actions, and root cause analysis.
As you move away from paper, a QMS enables you to organize and manage recorded data in real time, ensuring your records are always in sync. Plus, it removes obsolete documents from circulation. Increased data control helps your enterprise document itemized quality standard requirements within the system and then use a formalized mechanism for review/signoff, audits, checklists, procedures, documentation, and follow-up activities. In the event of an audit, you can more easily achieve and retain quality certifications by providing auditors with instant evidence of compliance.
It’s simple: a successful quality management strategy relies on having a strong QMS in your organization’s toolkit. The right system improves your business operations and helps you meet the requirements of your customers and auditors. Whether you manage all production internally or have suppliers of your own, maximizing the capabilities of your QMS allows you to remain compliant with the latest quality standards and regulations.