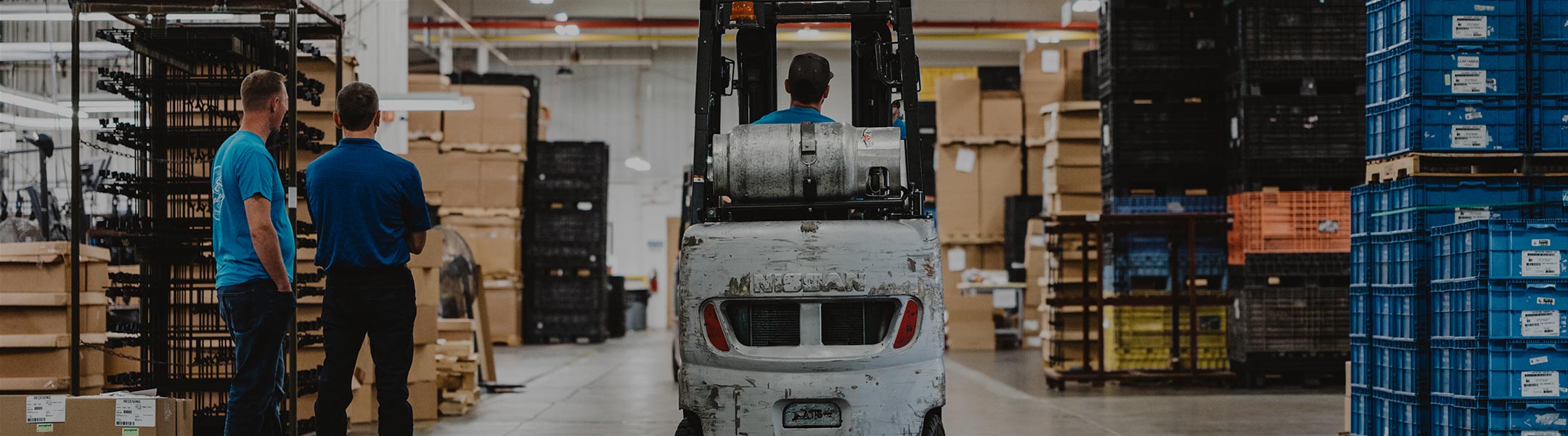
Get your copy of the 7th Annual State of Smart Manufacturing and hear from 300+ manufacturers in this new survey report!
For a monthly digest of expert insights, data points, and tips like the ones in this article.
Running a multi-operational business is an impressive feat, but that hasn’t always been the case for Brass Aluminum Forging Enterprises (BAFE). The company specializes in the production of brass, copper, and aluminum forgings and was originally comprised of only two forging presses, one trim press, and an eight-operator workforce. Over the years, the company has grown both in size and in opportunity, continually staying ahead of the competition. With over 150 employees today, BAFE continues to invest in expanding the physical and human capital and invest in impactful R&D initiatives.
However, success doesn’t come without the right tools and strategy. For years, Brass Aluminum struggled with a lack of visibility into material planning and purchasing, something that many manufacturers can relate to. The result? Their financial assets were locked in place, and the company found themselves unable to venture into new markets. To avoid customer-facing issues, the company over-purchased raw materials which both occupied space and impacted cash flow.
Something had to change for Brass Aluminum—they needed the ability to better track inventory and gain shop floor insights that could unlock new capabilities. To achieve this efficiency, Brass Aluminum looked to smart manufacturing technology in Plex ERP, which is inclusive of Plex MES and MES A&O. The company’s implementation and subsequent journey showcases a roadmap that manufacturers from all industries can learn from.
Change can be difficult, but Brass Aluminum’s strategic decision on which smart manufacturing tools to use means the battle was already half won. The manufacturer approached its implementation with the help of implementation partner SX to add even more confidence in their way forward. Together, the two companies successfully introduced Plex at a facility in Ferndale, Michigan. Since the implementation, the company has seen and benefitted from major operational improvements, something important to all manufacturers across industries.
With technology at their fingertips, foresight is now the name of the game at Brass Aluminum. Operators are aware of needed jobs days in advance, a significant upgrade to the previous uncertainty surrounding job changes. Department leads can also plan and prioritize tooling readiness based on which jobs are changing and when.
Additionally, Brass Aluminum has seen the elimination of organizational silos, helping the team across all departments communicate and collaborate with ease. Before Plex, every department had built its own data tracing and analyzing spreadsheets. That means each department had its own source of truth, and those truths oftentimes didn’t match. Leadership faced challenges in the decision-making process due to the variations of the answers to the same question from different departments. “With Plex, teams from all departments can communicate and collaborate to draw the conclusions that they and BAFE need to operate successfully,” commented Greta Gashaj Baffrow, Process Engineer & ERP System Admin.
Prior to Plex, the Brass Aluminum production recording process depended on manual operator counts without cross-checks. Now, the system efficiently records production that equates to the maximum yield, significantly increasing inventory accuracy. Enabled by Plex, Brass Aluminum has improved material traceability by 27%, improved material planning by 30%, and increased inventory accuracy by 50%. The transition to Plex as Brass Aluminum’s smart manufacturing platform has also increased cash flow and inventory insight, making it easier for the company to proactively plan and cut down on scrap. Now that’s something every manufacturer would love to accomplish.
Smarter manufacturing takes more than just flipping a switch and every company is different. But Brass Aluminum’s journey provides clear takeaways for manufacturers: find the right solution, commit 100% to its implementation and usage, and keep pushing the envelope.
With this mentality, Brass Aluminum now has a world of automation available for them to tap into. Gashaj Baffrow noted, “MRP & PRP modules have had a great impact on our material planning and purchasing. The Workcenter Logs screen is helping us understand the weaknesses in our processes, machine functionality, staff readiness, and availability to keep the production line up and running. The Control Panel is facilitating the production recording process for our operators and helping them reduce counting errors. Now BAFE’s goal is machine integration and MES A&O implementation so counts can be obtained directly from the machine.”
Imagine – these improvements are only the beginning of what’s possible. Brass Aluminum is currently working on one major project for their future: one that’ll provide an automated solution for optimized die setup. What projects could smart manufacturing technology help you achieve in your future?
For more real-world examples that can help you improve your own operations, view dozens of success stories here.