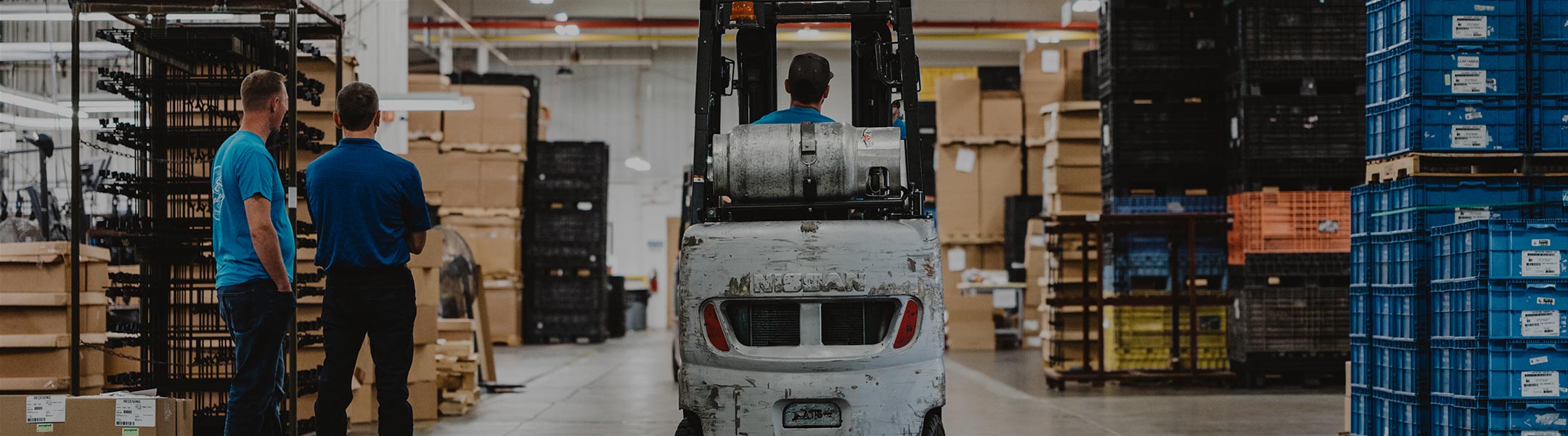
Get your copy of the 7th Annual State of Smart Manufacturing and hear from 300+ manufacturers in this new survey report!
For a monthly digest of expert insights, data points, and tips like the ones in this article.
Almost everyone loves French Fries. They go with many other foods and are a staple in restaurants around the world. But while many people enjoy them, most never think of what’s involved just to bring those fries to your plate.
The process to deliver fries that meet customer expectations is complex. The size of the potatoes can cause excess waste if too small. Blemishes and spots can create quality concerns and risk customer rejection. The amount of salt added has to account for shake-off.
All in all, there are many variables to pay attention that demand proper resource management. Without effective strategies inefficiencies can significantly impact profitability.
Food manufacturing faces unique challenges compared to other industries because of loss of yield during processing. Effective yield management has to address waste and inefficiencies by optimizing raw materials and processes.
Many factors can interfere with yield management, including:
Other variables that impact yield include the quality of raw materials, the type of equipment used within the plant, packaging formats, and broken processes. Operator skill and ambient conditions, like temperature and humidity, can also play a significant role.
But whether it’s due to legacy systems, patchwork siloed solutions, or home-brew processes and approaches, many food & beverage manufacturers deal with inconsistent, inaccurate data, and struggle to diagnose and fix issues within their processes.
These challenges combine to create a staggering drain on revenue and margins, and solving or mitigating them requires a new approach.
To achieve tighter control and better efficiency, food manufacturers are using smart manufacturing technologies for yield and materials management. This approach provides granular insight into individual processes like supply chain, quality, and inventory control so improvements can be made which deliver a powerful impact on the bottom line.
The critical component of this solution is the ability to accurately model, track & analyze the usage efficiency data of the inputs to the manufacturing process. The common challenges listed above usually stem from a lack of visibility, so harnessing data means manufacturers can obtain rapid feedback on actual yield. This in turn supports root cause analysis and sets the stage for continual improvement.
Plex Systems helps you connect your entire operations so you can gain deeper insights for optimization. Smart technology gives you timely visibility and control of yield performance to uncover the various factors influencing it, including raw material quality, production machinery, and operator efficiency.
Here are a few of the ways Plex lets you drive yield improvements within an operation:
Other benefits of the Plex platform that indirectly affect yield and help improve business processes include:
The demands on food manufacturers are only going to become more complex. But you can stay a step ahead by leveraging the best smart technology to create complete visibility and control to optimize your yield and revenue. Watch this webinar to discover how smart technology can help you manage yields and materials to keep you both competitive and productive.