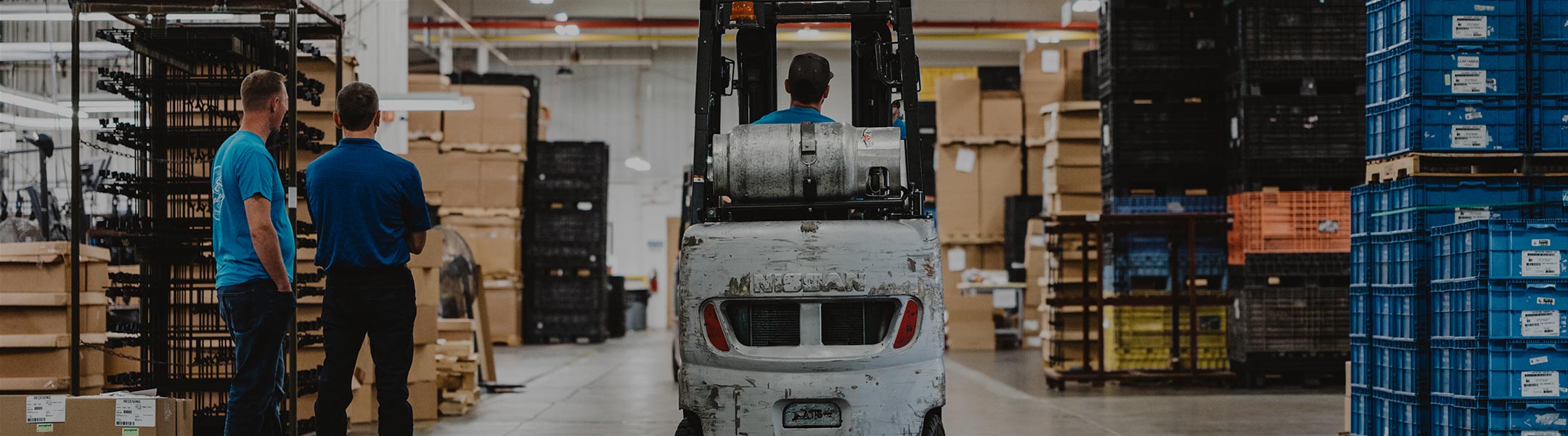
Get your copy of the 7th Annual State of Smart Manufacturing and hear from 300+ manufacturers in this new survey report!
For a monthly digest of expert insights, data points, and tips like the ones in this article.
Leadership within a complex operational structure has never been easy. Now, new pressures are making this level of responsibility even more challenging.
One of the forces in play is an unprecedented level of global disruption. From COVID to supply chain issues to rising energy costs, manufacturing operations leaders must navigate new hurdles and bottlenecks to ensure on-time delivery and extract greater efficiencies. Then there are changing workplace dynamics to consider, notably unprecedented and widespread labor shortages.
Before we can solve roadblocks, we must first understand some of the new headaches these factors create for operations leaders:
Statistics from the 9th Annual State of Smart Manufacturing Report confirm that obstacles are rife in today’s manual manufacturing operations. Overcoming the industry’s challenges are spurring companies to innovate, with 42% increasing automation and 37% introducing AI/ML technologies to beat roadblocks.
Without innovation, poor operational effectiveness results in an increased chance of equipment failures, including increased or chronic downtime and negative overall equipment effectiveness (OEE). These factors and more are driving manufacturers to accelerate digital transformation, with the result that technology investment in the industry is up 30% over last year.
The path to success lies in increasing visibility across the organization and harnessing data for more informed decision-making. Fortunately, technology that drives real-time data and analysis through process automation is here to help.
A smart manufacturing system breaks down the silos present in traditional manufacturing operations. It drives an automated, accurate, and real-time flow of data that links all business processes together under a single version of the truth.
Smart manufacturing software and technology also usher in the age of the connected worker by eliminating manual processes and the errors and data bias that come with them. Because everyone has access to machine, operator, and process data, analytics are accurate and relevant to the moment.
Quality becomes part of the process instead of a standalone operation. The same data that monitors and automates production volume and tasks allows process automation of quality protocols, allowing for automatic correction or fast action and mitigation by staff when required. As a result, quality losses are significantly reduced.
The same is true for inventory accuracy. Inventory is now tied to demand and production at a level never before possible. It becomes a data-driven link between production processes and a fully visible supply chain, allowing operations leaders to use data-driven decision-making to manage the disruptions previously discussed.
The result is higher quality, greater equipment and labor utilization, and superior operational resilience that ensures the on-time delivery required to remain competitive.
The challenges facing manufacturing operations are complex and multifaceted. Leaders who embrace data-driven solutions that eliminate manual processes and provide a platform for real-time data and analytics will be the ones who clear these obstacles and successfully drive growth.
For more on how data and technology can boost your leadership capabilities and drive value for your business, read this related article.