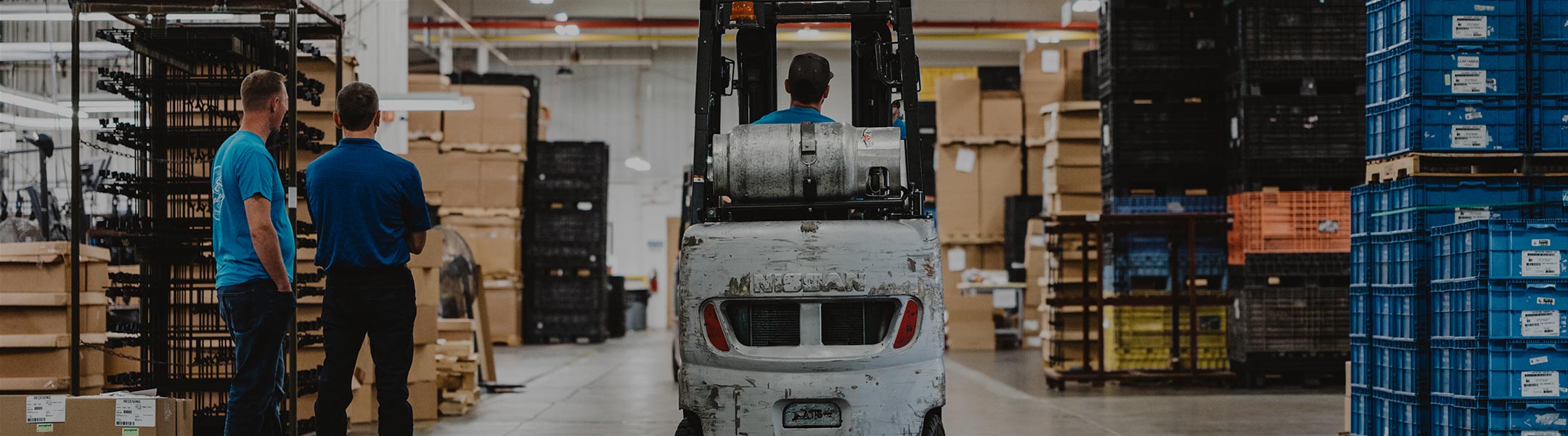
Get your copy of the 7th Annual State of Smart Manufacturing and hear from 300+ manufacturers in this new survey report!
For a monthly digest of expert insights, data points, and tips like the ones in this article.
In past decades, business continuity was mainly considered to respond to the dangers of natural disasters like fires, floods, or hurricanes. The dawn of the internet brought a new focus to continuity; it broadened its definition as companies raced to protect data from cyberattacks and breaches that could shut them down and leave them without critical information.
That definition has been re-challenged with significant disruptions that began with COVID-19 and continued with trade wars, stuck cargo ships, jammed supply lines, and more. These disruptions caused businesses to pivot to new solutions to stay afloat. Many businesses also made frequent raw material substations to address supply chain shortages.
Many commonalities impacted traditional operations and posed challenges for the continuation of businesses:
Before these new realities, companies had been moving toward lean operations. These methodologies were adopted in manufacturing and supply chains to create as little waste as possible. But the type of changes above meant that elements of these methodologies could no longer be practiced effectively.
In companies with traditional monitoring and tracking of production or with a heavy reliance on manual activity, this resulted in problems like:
Many of these disruptions aren’t going away anytime soon and will continue to influence business at some level. That’s why so many companies are now looking for a way to manage disruption efficiently into the future and prepare for whatever comes next.
The single best option for manufacturers lies in IIoT technology and digital manufacturing. While disruption interrupted the collaboration, communication, and workflows necessary for close adherence to lean and other methodologies, a smart manufacturing platform can fill those gaps and improve them to a point better than before the disruption occurred.
With a continuity plan and the digital technology of a solution like Plex, companies have the innovative tools needed to maintain and drive business. Because data is real-time, everyone from operators to executives can access the same analytical insights regardless of their physical location.
Smart manufacturing platforms also enable visualization of production so that managers, technicians, mechanics, and operators have a true picture of machine condition and production as it occurs. This capability allows them to be proactive and manage their tasks, even with distancing and other relatively new safety measures in place.
Modern technology also helps manage disruptions to the supply chain. As demand changes and disruption occurs, an innovative solution allows transparency throughout the supply chain to grant planners time to react and mitigate the impact. Plus, with a smart manufacturing platform, many machines can be connected to allow for autonomous or semi-autonomous operations that can be monitored from a distance. This enables automation at a scale not possible before.
If you’re ready to better manage disruption and improve business continuity no matter what comes at you next, then click here to learn more about the Plex Smart Manufacturing Platform.