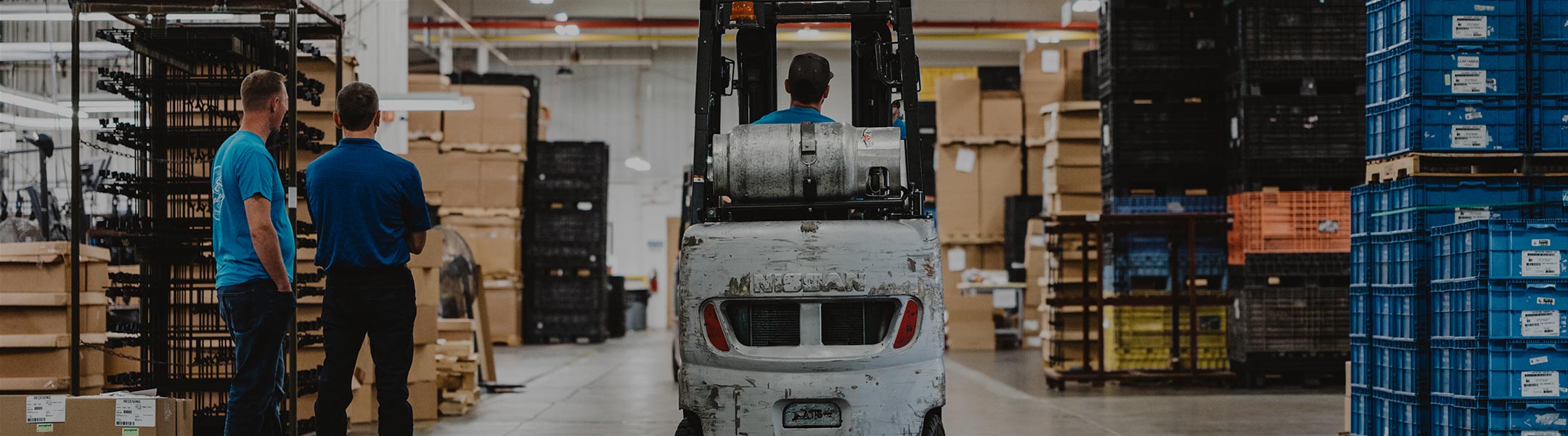
Get your copy of the 7th Annual State of Smart Manufacturing and hear from 300+ manufacturers in this new survey report!
For a monthly digest of expert insights, data points, and tips like the ones in this article.
The cost of quality has been a manufacturing KPI for generations. By understanding the cost of waste, rework, and scrap, companies can develop continuous improvement strategies that reduce or eliminate defects.
Many manufacturers rely on technology to strive for 100% quality, which lets them focus on continuous improvement and leads to significant savings when combined with the right tools and strategy. Let’s explore how smart manufacturing software can drive organizations toward 100% quality.
Strong smart manufacturing software can automate many processes involved in quality control, like production monitoring, variance from the spec, and more. It also eliminates the labor needed for inspection and testing, as these tasks can be done in real time at the point of production. The software uses data analytics to identify quality issues before they occur and enables real-time monitoring so operators can quickly act to address them.
Companies can adopt protocols and frameworks that work with smart manufacturing software and utilize less labor to achieve 100% quality, which alleviates workforce challenges while empowering current team members to focus on more impactful activities. As a result, employees will have greater confidence that improvements will work because of real-time data quality.
With supply chain complexity and volatility increasing, the cost of quality is more critical than ever. By combining smart manufacturing software with a quality mindset, companies can increase quality precision and extend the benefits of digitization into the supply chain.
Quality precision acts as a hedge against rising material costs. Empowered by robust software, products are made with greater accuracy and consistency. This accuracy offsets rising material costs by ensuring fewer materials are needed (or wasted) when producing each unit.
Using data analytics to optimize processes reduces the need for rework or scrap. This means companies can maintain higher profitability, even as material costs rise. Process optimization also leads to increased efficiency in the production process.
Let's face it; customers are more sophisticated and informed than ever. They have a much greater choice and more ways to purchase what they need. These factors combine to heighten the importance of a brand reputation that screams quality.
Smart manufacturing software eliminates the use of time-lagged data and brings actionability right to the point of production. The combination of real-time data, production monitoring, and automation results in improved product quality and cost savings.
These benefits directly impact customer satisfaction. Striving for 100% quality at the point of production means fewer defects in the hands of those you rely on for your sales. Not only does that make your company known for its quality, but that reputation flows to your customers who will also enjoy a boost in brand reputation by association.
Today more than ever, it’s imperative for manufacturers to carefully manage material costs and enhance their brand reputation among customers. A modern, digitized manufacturing company using smart manufacturing software has an edge over less savvy competitors in terms of costs and brand image.
Read more here to learn how a smart manufacturing strategy can help you improve quality, lower costs, and build your brand name.