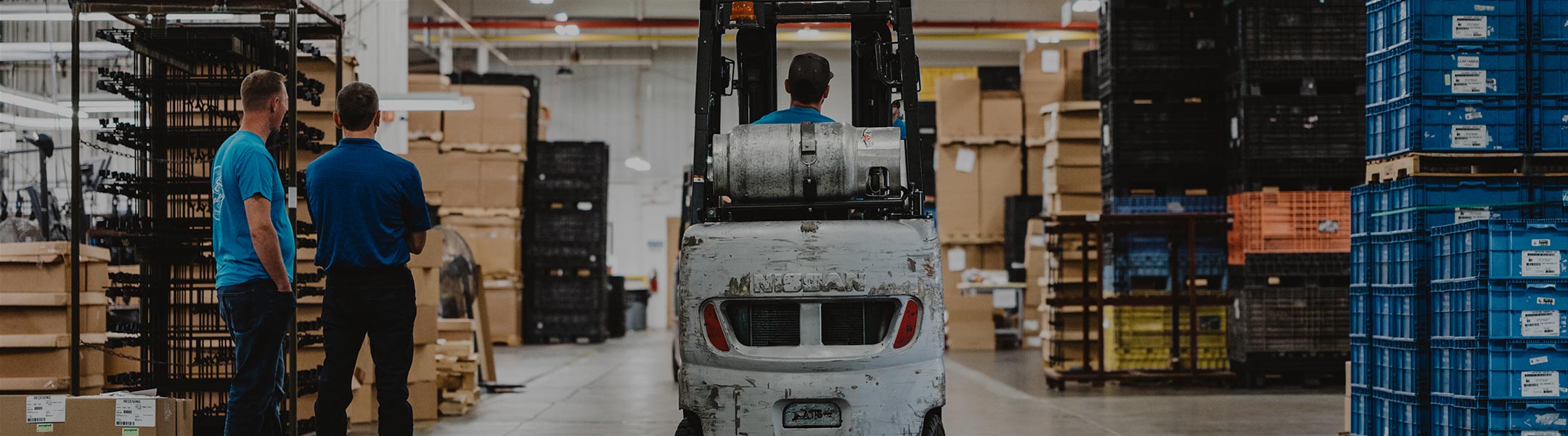
Get your copy of the 7th Annual State of Smart Manufacturing and hear from 300+ manufacturers in this new survey report!
For a monthly digest of expert insights, data points, and tips like the ones in this article.
The constant hum of excitement about the Industrial Internet of Things (IIoT) is becoming louder and more intelligible every day. It is now clear that we are well passed the initial hype (even if that is not the case in most consumer-facing IoT) and opportunities for forward thinking manufacturers are real. The initial benefits are in two areas: analytics and connectivity. But analytics and all the other benefits of the IIoT start with connectivity. In this post, I’m going to focus on plant floor connectivity, specifically where we are on the journey toward connectivity, and a quick look at where might that journey take us.
Dealing with the Challenges of Siloed, Operational Data
Most factory floor data has traditionally been used for control purposes. Between 95 and 99 percent was never used—it simply remained inside machines, devices, and probably heads. Another traditional deterrent to progress was the split between Operational Technology (OT) and Information Technology (IT). The cultural differences were probably a bigger problem than any technical separation. The interface between Manufacturing Execution Systems (MES) and business systems, usually ERP, was and remains a convenient point of separation between IT and OT.
Thankfully things are changing rapidly. IIoT has made everyone much more aware of plant data and its benefits beyond the shop floor. Those manufacturers who already run their software in the cloud have a clear lead in the plant-to-enterprise connection—part or all of the MES functionality already runs in the same environment as business systems, making “integration” easy.
The next phase of improvement will be more and better use of plant floor data. As little as one to five percent of plant data are made available to applications and people. Before the benefits of the IIoT can be delivered, that must change. It’s not reasonable to expect new data to be connected through traditional control hierarchy because connecting direct inputs and outputs (IO) is both expensive and inflexible. Instead, we need to make sure that data is connected in an efficient way and can be delivered to, or accessed by, whatever apps need it. Mobile devices alone do not address this issue, as they often have to go through the same control hierarchy in order to access information. As mobile devices become more sophisticated they will be able to process much more data. An example is augmented reality devices that need to access both manufacturing data and design information (such as 3D models) to help operators with complex assembly tasks.
Moving Forward with the Connected Plant
Many companies are now looking at the possibilities for accessing and using much more plant data. One area of growth that LNS Research predicted last year is the IoT device: a simple piece of kit with the possibility to connect to IO or specific data protocols and then to transfer that data via an Internet connection to the main information platform running in the cloud. These devices can be very low cost (we have even seen them based on Raspberry Pi boards) and provide access to useful information that would otherwise be tied up inside older plant equipment. As manufacturers of plant equipment, and especially complex machines, realize that there is potential in information. They are starting to build more sophisticated Internet Protocol (IP) based interfaces that give access to much more information.
There is still a problem with this model. Who owns the data? Most manufacturers want to keep control of the data generated by the machines they have bought as it may contain intellectual property or even affect security. However, it might be in the interest of a manufacturer to let the machine builder use detailed machine performance data in order to improve reliability, aid maintenance, and lead to better future design.
Another opportunity for complex machines in a connected world is to talk with each other—known as "machine-to-machine communication." This option negates the need for some supervisory control and automates some decisions but it will take time as standards and interconnectivity semantics need to be defined in an open and secure way. Manufacturers should not expect sophisticated machine-to-machine communication to be the norm in the next year or two.
Collecting Data and Using it Now
Although who owns the data is an important consideration for complex machines, for most newly accessible plant data, the most important thing is to make data available as widely as possible on a business platform. That way new data can lead to new business processes that enable people to do a better job. For example, location-aware devices allow a system to see where people are so they can be served relevant information on their mobile devices. With this information, managers can do their jobs while walking around a plant and operators get instructions specific to their location.
The short term goal for manufacturing companies should be to find ways to connect and collect as much data as possible from their plants then make it available through mobile devices to improve the quality of people’s work (and hence the quality of the products). As more data is gathered, those manufacturers who have a suitable cloud-based platform on which to analyze and manage such data will start to gain a substantial competitive advantage. They can then move on to the next phases of IIoT development—analytics and sharing information with your suppliers and customers.
Learn more about connecting your shop floor. Download the white paper, What’s Happening on Your Shop Floor?