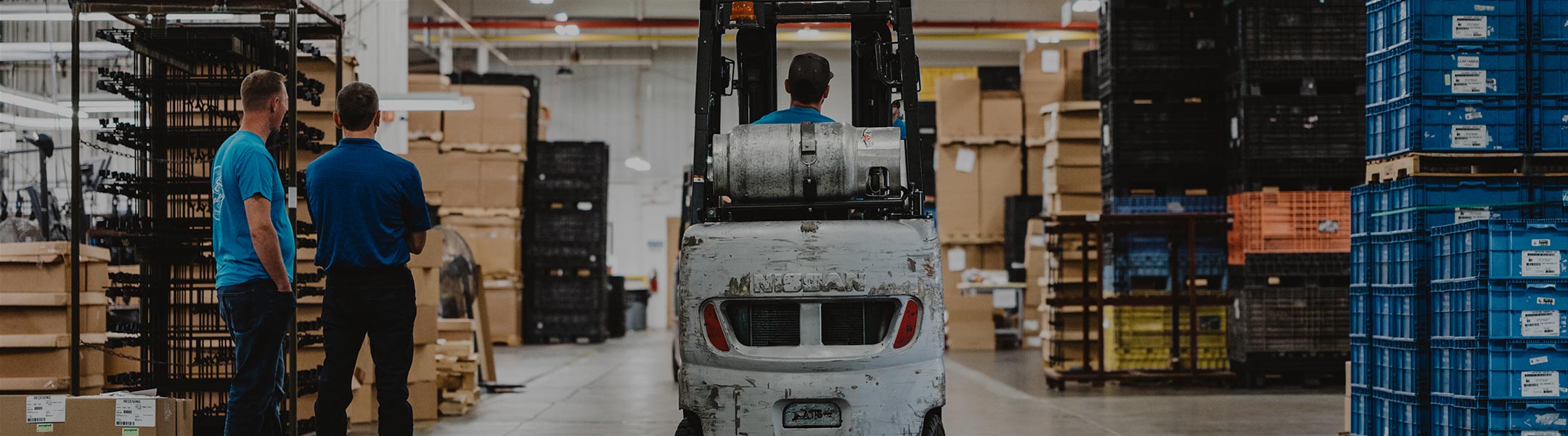
Get your copy of the 7th Annual State of Smart Manufacturing and hear from 300+ manufacturers in this new survey report!
For a monthly digest of expert insights, data points, and tips like the ones in this article.
Efficiency and downtime are two of the most recognized words in manufacturing. These two words are taught and enforced formally and informally from the executive boardroom to floor supervisors to an operator in their first week on the job.
While efficiency has a lot of variables and is calculated as creating as many finished units with the least amount of resources, downtime appears to be simple on the surface. Either the machine is running, or it isn’t.
But the problem with downtime isn’t as simple as stop and start. Instead, it lies in why a machine is down, the length of downtime, and what is done to restart.
Downtime can be broken down broadly into two types: planned and unplanned. Within each type, several reasons can contribute to downtime. There are several ways to classify these subcategories, and Lean, for example, breaks them down into waste types. The bottom line is that when equipment isn’t running, managers experience a case of the dreaded downtime blues.
Planned downtime is when a machine is scheduled to be down. For example, modern manufacturing uses measured jobs to plan labor capacity, so a break would be considered planned downtime. Types of planned downtime include:
Planned downtime is easier to manage because it’s known and teams have time to prepare. However, this doesn’t mean planned downtime isn’t open for improvement, as in the case of changeovers and line constraints.
It’s unplanned downtime where the manager’s blues hit the hardest. These are unexpected events with many causes, from systemized broken processes to one-off events. Common examples of unplanned downtime include:
With the current levels of inflation, disruption, labor shortages, and other factors, manufacturing faces a challenge to become more efficient in its operations. And that means addressing downtime in a new way.
Smart manufacturing software can lift the blues by offering benefits designed to zero in on downtime causes and develop strategies to mitigate or eliminate them. No more mystery events or missing information on a clipboard. These platforms also enable data-driven insights and advanced analytics to visually show teams and managers where, why, and how long an event occurred.
Smart manufacturing platforms can be customized to subdivide downtime reasons further so teams can focus on specific issues, detect patterns, and develop strategies for improvement. For example, there may be jams caused by operator error, mechanical error, or even higher than optimal temperature and humidity at the run time.
As the software is deployed, managers can identify trends using real-time actionable insights from cloud-based analytics. They can develop and implement process improvement methods to correct trends and patterns.
With a smart manufacturing platform, users have complete visibility over current production and conditions with advanced production monitoring. The ability to tackle multiple downtime issues within the facility while managing throughput, inventory, demand, and maintenance increases overall efficiency. As downtime falls, more resources are available to work on other processes requiring modification.
A best-in-class solution like the Plex Smart Manufacturing Platform™ cures your downtime blues with advanced analytics and machine learning algorithms. But it also allows you to manage demand and supply, optimize inventory, develop predictive maintenance strategies, and more.
Such a platform also integrates with other legacy and enterprise software to provide a single version of the truth. Your insights and efficiency improvement initiatives all rely on the same dependable data. This integration includes the capability to link to IoT hardware to take downtime even lower. If that’s not the right prescription for downtime blues, we don’t know what is.
Looking for more on downtime causes and solutions? Click here to read a related blog, Solving the Downtime Riddle.