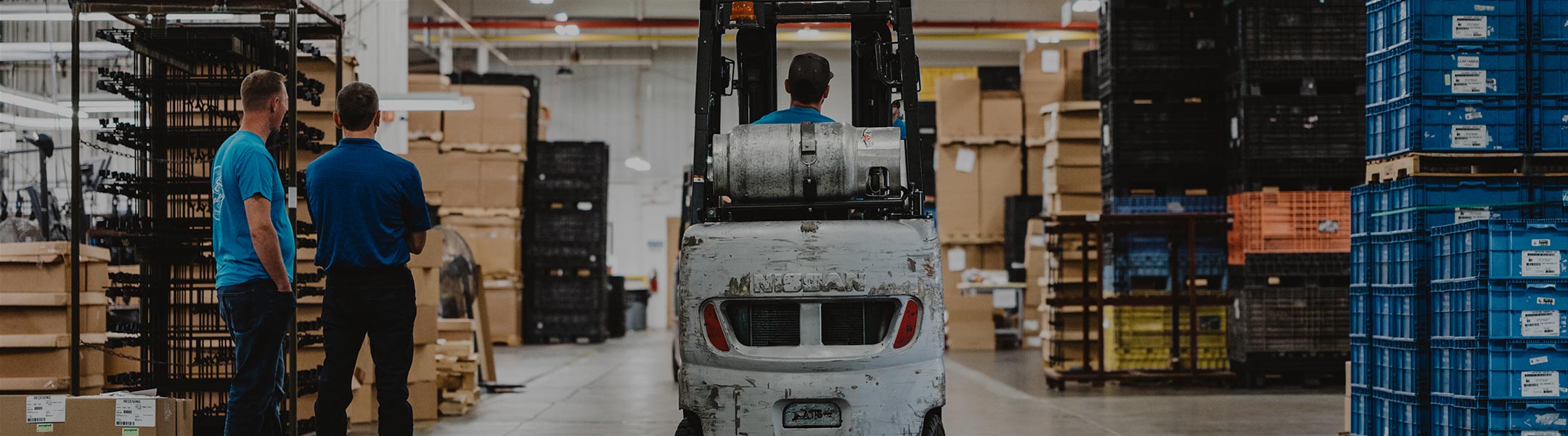
Get your copy of the 7th Annual State of Smart Manufacturing and hear from 300+ manufacturers in this new survey report!
For a monthly digest of expert insights, data points, and tips like the ones in this article.
“Efficiency” is a broad term in manufacturing. It means producing or doing something while using the least time, resources, and energy. For companies like yours, that may encompass efficiency of motion, the effectiveness of training, the quality of SOPs, or inventory accuracy. But it’s when all those components are working together that operations achieve their highest efficiency.
Many methodologies like Lean and Six Sigma are used to streamline operations and make various components work together. Within these methodologies, one tool stands out as a manufacturing “best practice” for measuring efficiency and building improvement strategies: OEE.
Overall equipment effectiveness (OEE) is a practice that uses formulas to measure how much planned production time is really productive. It seeks to increase efficiency by measuring the effectiveness of the production process.
By measuring a machine’s actual rate of production and comparing it to the theoretical rate, the effectiveness of the production process can be determined. OEE uses a formula to arrive at this number and can be broken into several categories that allow managers to focus on specific areas for change.
The basic way to calculate OEE is by taking the good unit count, multiplying it by the ideal cycle time, and dividing it by the planned production time.
OEE = (Good Count x Ideal Cycle Time)/Planned Production Time
In this formula, good count describes first quality units with no defects. The ideal cycle time is the quickest time that one unit can be produced. This cycle time does not mean the top speed of a machine. The product mix will determine the fastest speed for each piece or unit manufactured, which may vary across product ranges. Planned production time is the total time scheduled for a machine to complete an order or batch of orders. This time may include measured elements such as fatigue time or breaks as well as standard changeover times.
The OEE formula combines these elements to give the total productive time where first-quality pieces are produced as quickly as possible without stopping.
OEE is a high-level metric that assigns a numeric value to machine performance. It is used as a benchmark for measuring performance so that strategies can be deployed to gain greater efficiency.
The OEE formula is a measure of all time. But to drill down further to find opportunities for improvement, some sub-calculations can help understand OEE in specific areas. These calculations include:
Availability counts for planned stops such as changeovers and unplanned stops such as breakdowns and material flow issues. Availability is calculated as run time divided by planned production time.
(Run Time = Planned Production Time) – Stop Time
The performance calculation seeks to capture all short-term, small stops that reduce production speed. This time includes clearing jams, quick brushing, cleaning of fixtures, and other small events. It is calculated as the ideal cycle time times the total count produced and then divided by the run time.
Performance = (Ideal Cycle Time x Total Count Produced) / Run Time
The quality calculation seeks to measure a simple ratio of first quality parts fastest. This ratio includes reworks that can be returned to first quality with additional labor. The ratio is taken as a simple function of good count divided by total count.
Quality = Good Count / Total Count
Many manufacturers operate with around 60% OEE. And others may drop to as low as 20-40%. Used as an improvement metric, OEE helps companies identify areas of improvement overall and within specific functions such as quality, performance, and availability.
While it’s possible to manage OEE programs manually, why would you? If the goal is to measure production effectiveness to develop improvements that drive higher efficiency, why use a manual measurement system that is neither effective nor efficient?
Software in the form of a smart manufacturing platform, robust ERP, MRP, or MES system can significantly improve the accuracy of the measurements required to calculate OEE at any level. These platforms offer real-time data insights using advanced analytics by connecting directly to the devices embedded in or added to the equipment.
Want to see how software can drive your OEE program, free you from calculators and spreadsheets, and help you discover hidden capacity and value in your production system? Learn more here.