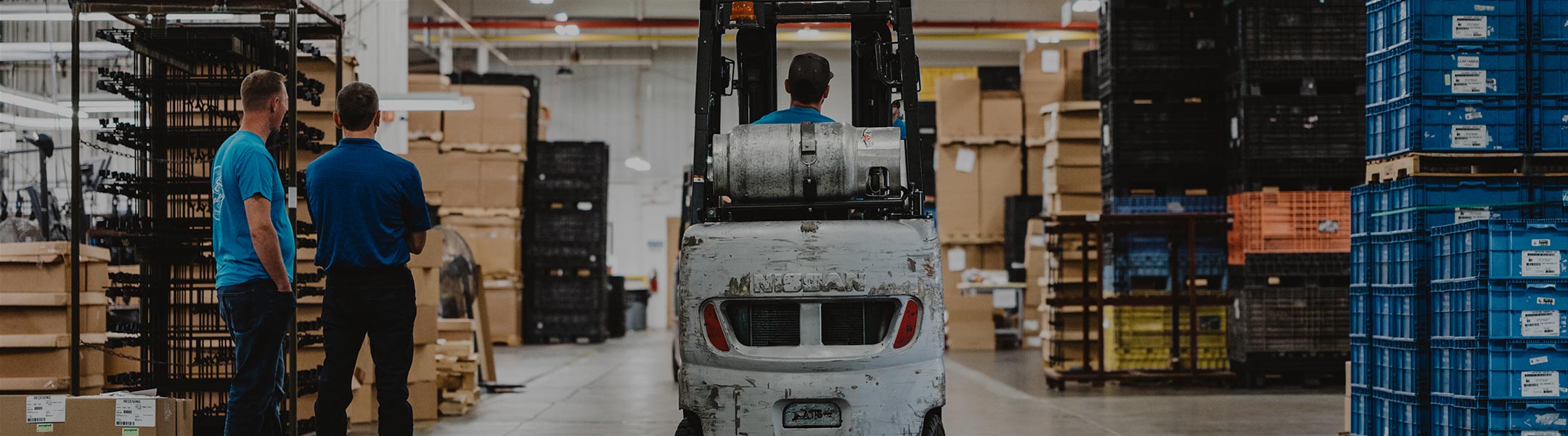
Get your copy of the 7th Annual State of Smart Manufacturing and hear from 300+ manufacturers in this new survey report!
For a monthly digest of expert insights, data points, and tips like the ones in this article.
One of the things I liked best about the recent PowerPlex 2016 conference was hearing first-hand feedback from customers. Many stories centered on the increased productivity and efficiency that a connected plant floor offers and how the Plex Manufacturing Cloud enables that connectivity.
Intricate, a leading high-tech metal stamping designer and manufacturer with facilities in China and Roanoke, VA, implemented the Plex Manufacturing Cloud in 2012-2013 after several expansions of their manufacturing plants. In conjunction with Plex partner, Kors Engineering, the company used the Kors MACH2 product to connect cloud transactions with plant floor machines through programmable logic controllers (PLCs).
Plex was initially implemented in Intricate’s Roanoke manufacturing facility, which involved configuration planning, wiring/installing the PLCs, testing with KORS and MACH2, and scaling to all work centers throughout the facility. The China implementation mirrored the US configuration with one week spent testing internally. On the first day of the second week, Intricate went live.
The driving factors for Plex programmable logic controller (PLC) integration included:
As a result of the integration, Intricate’s plant floor employees are able to get a real-time view of the shop floor through the MACH2 interface. At Intricate, every status in “OFF” is registered as downtime, so by using Plex to automate tracking of production hours and status, manual errors that could potentially affect OEE are eliminated.
Future plans call for integration with tooling that will, for example, stop machines when they reach 100 percent wear. Additional screens and visualization and more widespread use of mobile devices such as tablets and Bluetooth scanners connected to the Plex Manufacturing Cloud will provide faster response and improved productivity.
ParkOhio’s Assembly Components Group, a leader in the manufacturing of highly engineered components used in the final product of major original equipment manufacturer (OEM) assemblies (such as automobiles, agricultural, commercial trucks, forklifts, engines, or industrial equipment) first implemented Plex in 2009. Today Plex adoption encompasses 300 salaried users, 1,600 hourly employees, and 400 suppliers across 12 sites.
In 2013, ParkOhio acquired Bates LLC in Lobelville, TN along with some new, major OEM customers. In 2014, the Plex pilot system was successfully designed, configured and implemented in only five weeks. Plex replaced completely manual and paper systems; up until that time, many of the employees weren’t even using email. The roll-out went so smoothly that two weeks after the go-live date, one of the OEM customers asked if they had gone live yet!
ParkOhio also installed 13 Kors Engineering MACH2 vision centers with plans to install an additional 16, using MACH2 as the operator interface—communicating with Plex and pushing data into the Plex Manufacturing Cloud. Since the implementation, labeling errors at a key customer have been reduced to zero, and inventory accuracy and container-packed quantity have improved to 100 percent. At the same time, operator efficiency has increased.
Hatch Stamping Company is a world leader in highly engineered metal stampings and assemblies for the automotive industry. Hatch has been a Plex customer for the past eight years and is an early adopter for Plex UX (the next generation Plex user experience). Of 18 Hatch facilities using Plex, 4 are on Plex UX and Hatch is in the process of converting them all to the new interface— in order to take advantage of new features and the modern, customizable visualization and user experience.
Hatch has extended the functionality of the Plex control panel to provide more extensive work center status event reporting to the Plex Manufacturing Cloud—including information about planned maintenance, production, downtime, planned shutdown, and changeover set-up. For example, Hatch created a detailed downtime analysis report, and information regarding how common problems are solved has been added in drill-down screens (fixes to be automated in the future). By gathering more details from the plant floor, both uptime and quality have improved.
As with many presentations at PowerPlex 2016, this one provided an opportunity for interaction among members of the Plex community. The Hatch team offered support for their peers who expressed interest in creating a similar set of screens and reports for their own shop floor, providing detailed step-by-step handouts and copies of the presentation, as well as addressing many audience questions.
Plex collaborates with customers and partners to identify new use cases for the Plex Manufacturing Cloud and Internet of Things (IoT) technologies on the plant floor. These are just a few of the many customer stories shared during the PowerPlex conference — focused on finding use cases that provide better efficiency through automation, more-informed business decisions through analytics, and increased mobility through support of wearables and other emerging mobile technologies.