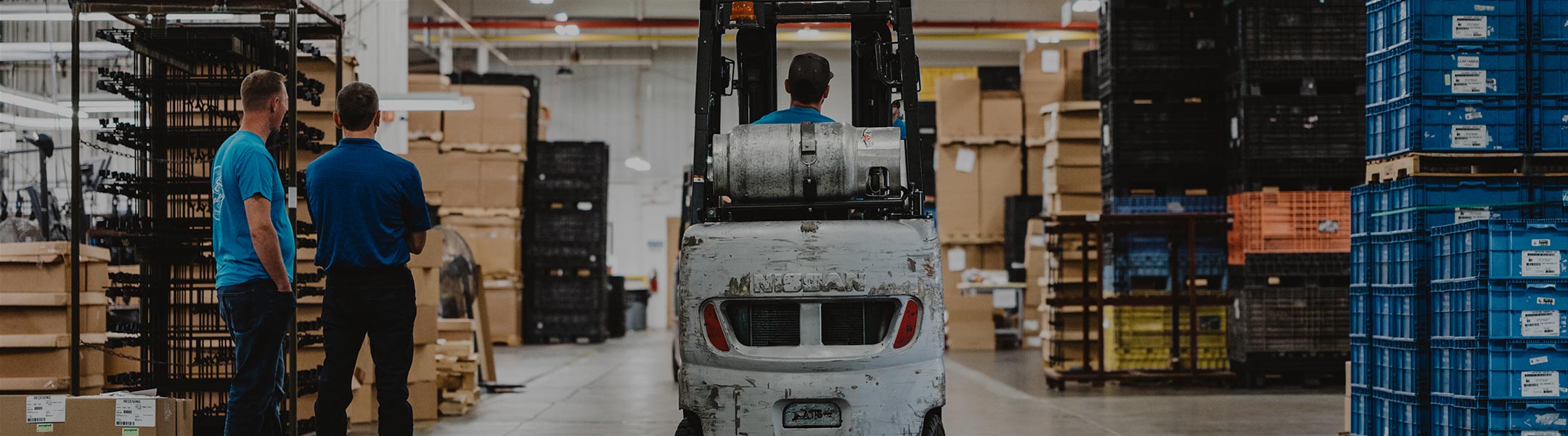
Get your copy of the 7th Annual State of Smart Manufacturing and hear from 300+ manufacturers in this new survey report!
For a monthly digest of expert insights, data points, and tips like the ones in this article.
In the United States, economic growth has been a bit sluggish in the past decade. When you look at global economic growth, there's one common factor with all that causes the economy to grow.
It’s manufacturing.
Due to a number of contributing economic, political, and market factors across the globe, there’s a significant revolution that’s underway within the manufacturing industry. The revolution is commonly referred to as Industry 4.0.
The first industrial revolution (1.0) involved the mechanization of production converting water to steam power. The second industrial revolution (2.0) took place 30 years later when the first electricity-powered assembly line introduced mass production. The third industrial revolution (3.0) started in the late 1960s when the first programmable logistic controller (PLC) enabled production automation through the use of electronic and IT systems.
Industry 4.0 refers to the combination of several major technology innovations, all maturing at the same time, that is expected to significantly shift the landscape of the manufacturing industry. These technologies – advanced robotics, artificial intelligence, sophisticated sensors, cloud computing and big data analytics – all exist in manufacturing today in some form, but as they integrate with one another, the physical and virtual worlds will interlink and transform the industry.
Advanced Manufacturing Technology
The key objective of Industry 4.0 is to drive manufacturing forward: to be faster, more efficient, and customer-centric while pushing beyond automation and optimization to discover new business opportunities and models.
By embedding modern technology into manufacturing, you essentially achieve Industry 4.0 objectives. In terms of business technology, it goes beyond transactions like accounts payable or receivable. It’s bigger than that. It goes beyond applications and software versions. Gone are the days of having to buy adapters and different layers of business technology to maintain and manage. And if the letters “ERP” make you cringe, it’s for good reason. ERP comes with a lot of administrative baggage and frankly dabbles in manufacturing. With the advent of cloud computing, there is a system that allows you to do more than just replace existing functionality. You can transform the way you do business and figure out how you’re going to beat the competition.
The other critical area where technology makes a big impact is with your workforce. Communication and collaboration are what will help you retain your best people. They need to talk about what is happening in the “manufacturing moment” to find the solutions that work. To attract quality candidates, you need to establish an environment that is similar to our everyday modern lives. The days of cubicles, tethered desktop computers, and physically being present on the shop floor are gone. Young workers want to run everything—including business—from mobile devices.
Stepping Stones to Industry 4.0
If you want to thrive in the business of manufacturing, you have to be agile. You have to adapt to customer demand, and you have to look at what it takes to be a leader. If you want to know where your company is on the path to Industry 4.0, we’ve developed a maturity model that can help identify that for you. You can use the model to plot out a path to move through your Industry 4.0 journey which will set you on course to get you ahead of your competition. Click here to go to the maturity model.