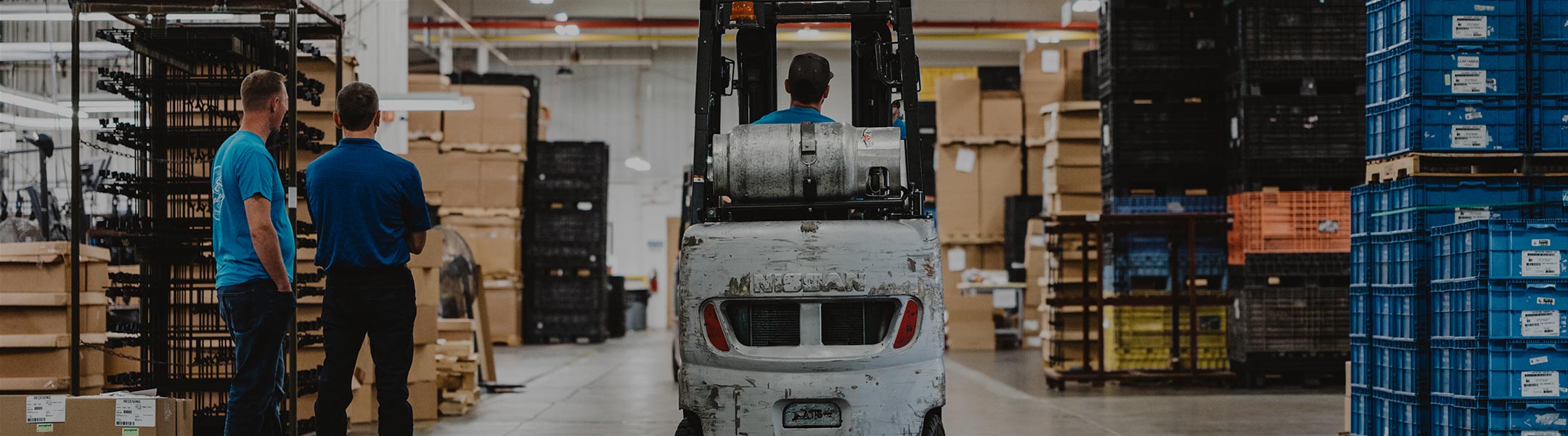
Get your copy of the 7th Annual State of Smart Manufacturing and hear from 300+ manufacturers in this new survey report!
For a monthly digest of expert insights, data points, and tips like the ones in this article.
Product and technology innovation has transformed life as we know it in the last few decades, and the pace of change is only getting faster over the next decade. Inventors and innovators continue to look for ways to make life easier, automate repetitive tasks, and remove the likelihood of human error by teaching machines to do what humans would otherwise do. Self-driving cars removing the need for human drivers, robots automating manufacturing processes that required line workers, and self-guided vacuums and lawn mowers are only a few examples.
While several jobs are certainly being automated for greater efficiency, if you read the latest news headlines, you might be under the impression that manufacturing workers are very close to being replaced by robot overlords who will soon take our jobs, our money, and our futures. Some government officials have even proposed taxing manufacturing robot productivity (in lieu of payroll taxes) to protect manufacturing jobs.
For many manufacturers however, the idea of automation replacing human jobs couldn’t be further from the truth; but the relationship between industrial automation and jobs* is complex.
Truth in the Numbers
When it comes to today’s manufacturing workforce, it’s important to not only look at jobs that could be automated, but also the jobs that are going unfilled:
At the same time, economic forecast company Oxford Economics (OE) recently shared a very scary global statistic: By 2030, robots will displace 20 million manufacturing jobs worldwide.
Looking at the math, something seems amiss, even accounting for the differing timelines and dispersion of robots globally. Why aren’t predictions for future workforce shortages less cataclysmic?
The skills gap.
Machines vs Humans? Who is best suited for the job?
Put simply, not all jobs in a manufacturing environment can be automated.* As the manufacturing environment has evolved over the last couple centuries, humans have played a critical role in managing change, directing the use of technology, and making decisions with a broader contextual awareness than machines may have access to.
Increased use of automated tools and technology will require a different skill set from future machinery operators and managers alike. A study from McKinsey & Company on automation and the future of the workforce predicts that the following skills are going to become increasingly important:
According to Sue Griffith Smith, the future of work requires ongoing education, flexible skills, and engagement from both educators and manufacturers. Smith is the Vice President for Advanced Manufacturing and Applied Sciences at Ivy Tech Community College and serves on the National Advisory Council on Innovation and Entrepreneurship Board with the U.S. Department of Commerce. These responsibilities give her a front-row seat to both preparing students for the work of the future and talking with legislators about what that future will look like.
“What we need to understand is that in the future, factories aren’t going to look like they do today: They are going to be integrated production environments,” says Smith.
Smith says that while machines and factories of the future will be very fluent in artificial intelligence, have greater spatial and environmental awareness, and are going to have greater agility to respond to changing conditions, the manufacturing ecosystem as a whole will need more than that to succeed. These integrated production environments of the future will also need greater agility to respond to new systems, new customers, and changes in global trade policies, which will continue to shape the industry as we know it. The latter is not something that machines and robots can automate, and therefore, the automation-proof skills* required for the industry to thrive will need to be developed and will ultimately protect human jobs.
When it comes to helping manufacturing workers develop those skills, Smith says it’s not enough to have an online education. “We have to have an educational system that aligns with the industry and support careers that don’t exist today,” says Smith. “Students graduating now have to demonstrate competence in several areas. There’s a pathway that exists to success in manufacturing, but future workers still have to be educated to thrive in modern manufacturing.”
Manufacturing Has a Culture Problem
Manufacturing has a reputation problem. CNBC recently reported that many Americans consider blue-collar manufacturing work “beneath them.”
Nick Pinchuk, chairman and CEO of Snap-on is quoted in this article as saying, “It is a PR problem. People view these jobs as welders or mechanics as the consolation jobs of our society. These jobs are not a consolation prize.”
Manufacturing jobs, especially skilled trades, continue to be available. Unfortunately, millennials choose to turn down these jobs in favor of careers in other industries that provide better working conditions, better pay, and better growth opportunities. We need to look no further than the 2.3 million manufacturing jobs projected to go unfilled, for proof of this.
So should robots be considered the enemy? The evidence says probably not.
The gap between the jobs that need to be filled and the talent required to fill them is broad and can’t entirely be filled by robots. One could even argue that the prevalence of industrial automation solutions isn’t creating problems – it’s actually solving problems, but can’t do it alone. In fact, automation and technology advancements may be helping prevent the manufacturing industry from falling into a complete tailspin.
The right kind of education, a culture that embraces and enables lifelong learning, and a different perception of the manufacturing industry are all required for manufacturers to find, keep and foster the kind of talent that will lead to success over the next decade and far beyond.
Advice for Manufacturers: Fix the Culture
Smith’s biggest piece of advice? Get involved.
Manufacturers should look step up and take control of the situation, treat their team like a critical business resource and behave like marketers when it comes to publicizing employment opportunities.
Employees from any generation – boomers to millennials – value these five things in a future employer, says Smith:
This doesn’t replace salary and benefits but can be differentiators in an extremely competitive marketplace, and may be part of what helps put manufacturing careers on part with other industries for millennials.
The Fourth Industrial Revolution is upon us and work needs to similarly transform to keep up. Manufactures who take the step to proactively prepare for an evolving workforce will be pleasantly surprised to find that automation, robots, and humans can coexist peacefully.
No robot overlords required.
Download this report for more information on the future State of Manufacturing Technology.
Sources: