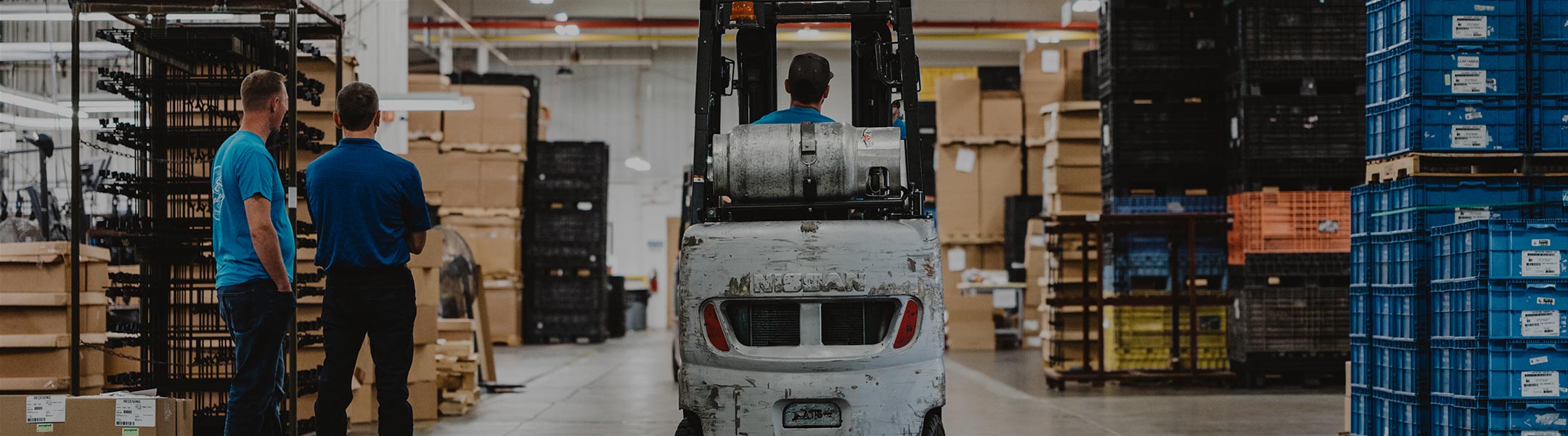
Get your copy of the 7th Annual State of Smart Manufacturing and hear from 300+ manufacturers in this new survey report!
For a monthly digest of expert insights, data points, and tips like the ones in this article.
Paper records are prone to errors, difficult to manage, and may be impossible to find in a timely manner, like within two hours as the FDA requires. High profile recalls have increased in recent years and culpable manufacturers have paid high costs to their businesses and their brands.
Applying Rigorous Track and Trace Methodology
A system that uses rigorous track and trace methodology throughout governs operational behavior. Operators cannot proceed to next steps unless the previous step is validated against a digital control plan that has been designed and approved by engineering. This inherent error-proofing protects against quality failures from operators using materials that may look alike but are not.
Documenting and Recording Each Step
Barcode scanners and printers record and document every step from receipt to movement to inspection and on to shipping. For every action on the shop floor, there is a transaction in the system. Simply tracking the receipt of raw materials and shipment of finished goods may fulfill minimum requirements, but the real value of product traceability is when every step is tied together in an end-to-end historical chain. A high-resolution trace tree illustrates the path of every part or lot of material visually and shows how it relates to every product and shipment of finished goods.
Catching an Error Before It Becomes a Costly Recall
When a particular lot of material has been flagged or quarantined as non-compliant, the system will automatically trigger the “no-go” response wherever that material is trying to be loaded. Suspect orders can be tracked down to a specific lot of material or shipment of finished goods to identify any and all affected product. This makes it much faster to trace backwards or forwards to find the responsible party or affected customer(s) to better contain the issue and minimize your exposure. Without such a capability, companies typically recall whole production runs at greater expense than necessary.
Errors end up costing your company both in actual dollars and reputation—whether it’s loss of time, loss of material, or worse, loss of customers. Want to discover more ways to protect your manufacturing business from errors? Download the eBook: 6 Ways Error-Proofing Protects Your Manufacturing Business.