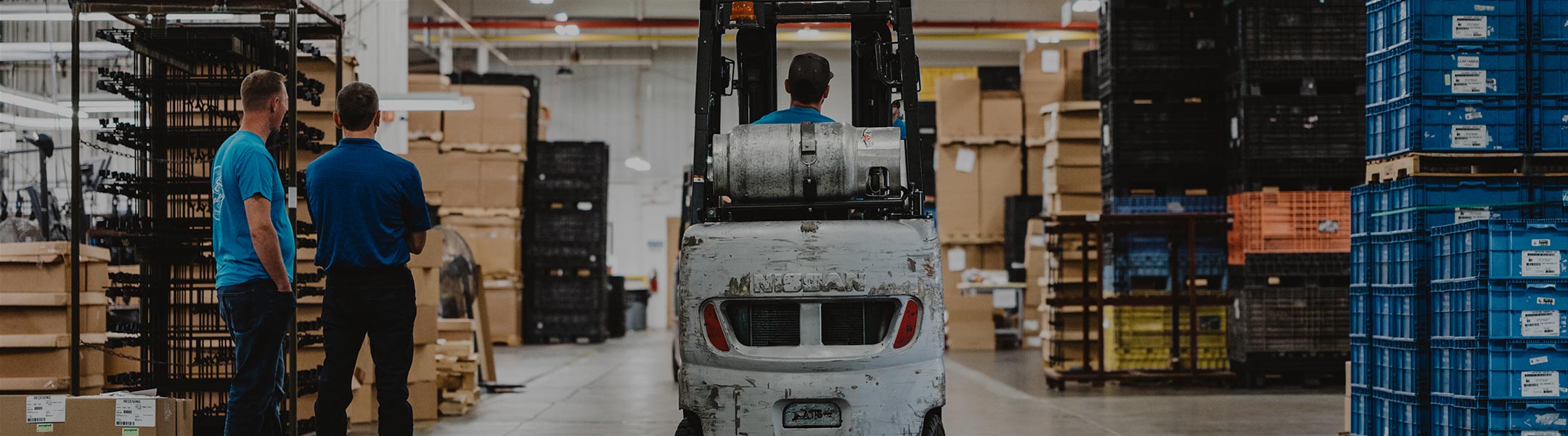
Get your copy of the 7th Annual State of Smart Manufacturing and hear from 300+ manufacturers in this new survey report!
For a monthly digest of expert insights, data points, and tips like the ones in this article.
There was a time in manufacturing before personal computers (PCs). Data was manually tracked, and decisions were made based on experience, gut feelings, and guesswork. But the lowly PC changed all that. Suddenly, companies could store more data and utilize spreadsheets to analyze operational aspects.
As much as that was a big leap in operational improvement, it still relied on an overabundance of siloed, error-prone, and manual data. And while decision-making improved, it needed to be optimized.
Today, manufacturing is on the cusp of a much more significant leap forward, and one that makes the arrival of the PC pale in comparison. As manufacturing industry executives realize and embrace the power of their operational data, they know that to be a true manufacturing industry leader, they will need to embrace data-driven operations and become a technology leader.
Manufacturers face many external and internal challenges with hyper-competitive markets, increasing regulation, and ongoing market disruptions. Automation and data control is the only way to address these challenges to maintain or increase revenue and profitability.
So, where do industry leaders fall in their understanding of how to navigate these changes? To start, 47% cite increasing costs as a significant obstacle to growth. And these increases are not focused on one area that would allow targeted action.
They encompass all manufacturing, including production, maintenance, and overheads.
Similarly, with shifting consumer tastes, more sophisticated customer purchasing decisions, and the rise of mass customization and other capabilities, maintaining and improving product quality is a brand imperative, and 43% consider it a significant challenge to growth.
Compounding these challenges is that manufacturing must deal with many legacy machine assets. As new OEM machines usually contain native connectivity capabilities, other equipment must be retrofitted and updated to bring it into the data stream. As a result, 37% of manufacturers must deal with a lack of agility and flexibility that comes with such legacy systems and assets.
Finally, having access to data and having that data available in consumable, contextualized formats are areas that still need improvement. And 36% of manufacturers need help with data access to unlock the visibility of their operational performance on the shop floor.
How well a company can overcome these challenges boils down to where they are on the maturity path. Those who are further along that path have benefited from more effective decision-making. Takeaways from this maturity scale reveal some interesting insights:
Data-driven manufacturing and decision-making is more than just using data and analytics. It means adopting a different mindset to manage the enterprise. This mindset impacts business models and how decisions are made.
The reality is stark. Half of digital laggards still use traditional, top-down decision-making in their operations. But for digital leaders, nearly half (45%) have already shifted to a collaborative decision-making process. With complete operational visibility, these companies let data and analytical insights guide them.
That visibility and accuracy of insights let them include business partners and external resources like suppliers in the decision-making process to manage holistically.
Data-driven manufacturing is not a trend. As digital leaders progress on the maturity path, digital laggards will be forced to adapt or drop out. The proof, as always, is in the impact on the bottom line.
Revenue performance for manufacturers who are digital leaders is more than double that of laggards. And profit performance improvement is almost triple that of less technologically mature companies.
An analyst brief from IDC, sponsored by Plex, noted that operational efficiency, time-to-market, employee productivity, and cost reduction have realized double-digit improvements in the last year alone.
Process automation is the key to these improvements and overcoming the challenges faced by manufacturing. That automation, combined with robust smart manufacturing and software solutions, leverages a company’s machine data to optimize processes, improve decision-making, and revolutionize performance.
Where are you on your digital journey? Are your systems ready or capable of maturing at the pace needed to remain competitive?
Contact us if you’d like to know more about how software solutions and smart manufacturing can help you embrace data-driven operations.