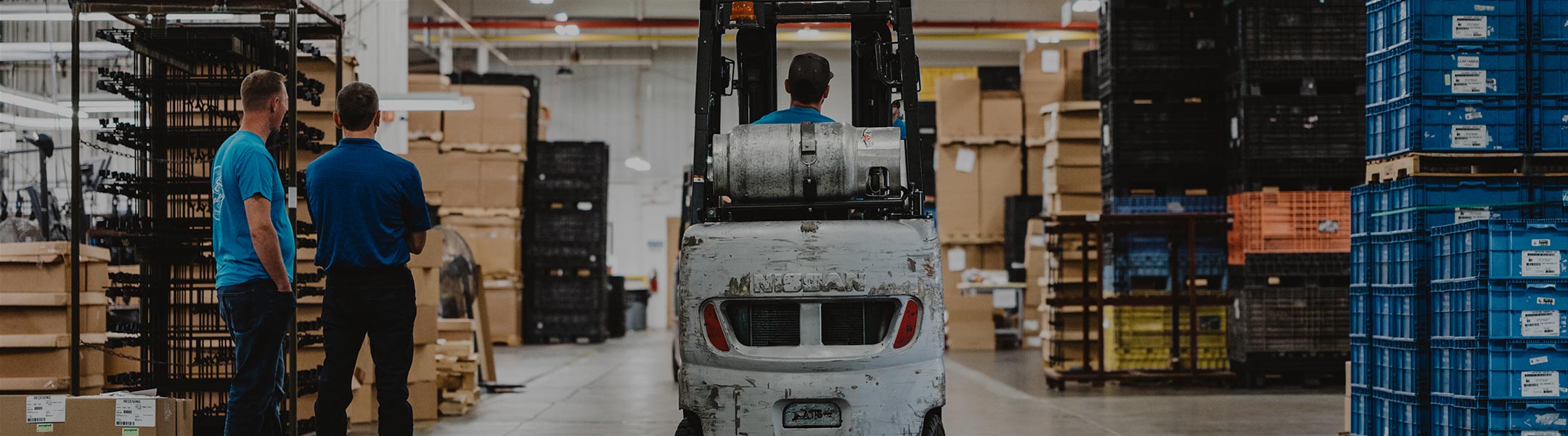
Get your copy of the 7th Annual State of Smart Manufacturing and hear from 300+ manufacturers in this new survey report!
For a monthly digest of expert insights, data points, and tips like the ones in this article.
Many people only look at production operations to assess quality within an operation. But quality is imperative across all departments within manufacturing. Production processes, inventory management, maintenance, and the demand and supply planning process are all critical components of quality management.
However, there are two different approaches for businesses regarding these processes - manual and automated. And each has a very different cost and impact on product quality.
Manual processes involve spreadsheets, clipboards, forms, and other well-known data-gathering and analysis tools to plan and manage demand and supply. They’re prone to human error, bias, and omission, leading to overproduction or underproduction of goods, excess inventory, or stockouts.
In contrast, automated processes use specialized software to accurately perform the same tasks. The critical difference between manual and automated systems is the data depth and analysis speed. With traditional data tracking, there is simply no way to manually record the volume of data required for deeper analysis. The captured data requires entry, manipulation, rationalizing, and other techniques to render it useful.
As discussed in our Smart Manufacturing Buyer’s Guide, automating processes using software with advanced algorithms and predictive analytics eliminates errors and enables better decision-making. Transactions are updated immediately across the system to provide real-time visibility of precise conditions using advanced analytics, machine learning, and a wide range of IIoT devices.
An automated demand and supply process has many advantages and hinges on building a strong digital foundation. It also impacts quality, with the biggest impact being schedule stability. Chaos increases the likelihood of mistakes and shortcuts. By having a stable schedule, the need to stop, start, and expedite goes away.
An automated process also connects to point-of-sale data and pulls information from suppliers and distributors, making incorporating real-time information into forecasting and analysis easier. This ensures more accurate forecasts and allows companies to improve quality across the entire manufacturing operational supply chain.
The best way to ensure on-time first quality goods is to plan supply chain and production processes well. But manual processes require planners and other staff to spend time manually inputting data into spreadsheets, analyzing data, and making decisions based on the analysis. This process strains the entire supply chain and can introduce mistakes in quality.
Using demand and supply planning software, companies can utilize their respective labor to focus on value-added tasks rather than gathering data. Software systems ranging from inventory management and optimization to supply chain logistics and planning create a seamless flow of information.
This all-in-one approach to a unified system and real-time data saves significant time, money, and human resources. For example, software can enable automation for warehousing and inventory management. Transactional data is sent throughout the system instantly, so not only do the accurate insights impact product quality, but they do so with less labor.
Waste management is a burdensome cost and strains supply chains by pulling on labor, staging, storage space, and other vital components of production planning. The first material must be sorted by rework, second quality, and scrap.
Rework creates an additional strain on resources and increases costs. Second quality results in a lower sale price, and scrap is an absolute loss on the materials line. With demand and supply software, real-time data enables proactive measures with suppliers to ensure quality at the outset rather than after materials have hit the production floor.
Real-time software can also generate valuable insights into overall operations by automating the tracking and monitoring of resource usage, compliance, logistics, and more. These insights enable decision-makers to look for opportunities to improve disposal or eliminate waste categories such as scrap, second quality, and rework.
Compliance is a severe challenge for many businesses and almost always directly impacts quality. With a growing number of regulations and standards set by governments and industry bodies, keeping up with change sheets becomes overwhelming.
If the right changes aren’t made quickly, it can mean recalls, fines, or even dangerous safety lapses. The proper demand planning software empowers companies’ compliance efforts using real-time data. Changes made for regulatory and compliance reasons are available across manufacturing, reducing the chance of creating products with the wrong materials or performance specifications.
Software is also an excellent way to track in-house expiry requirements and those from inbound raw materials from suppliers. Companies can maintain vendor scorecards and manage supplier due diligence processes so vendors are ethically and materially compliant.
Scrap, rework, and waste aren’t just production problems; they’re whole system problems. Managing them with automation and advanced software is as significant a contributor to building a culture of quality as any other program.
But this requires a solid digital foundation. If your company doesn’t identify and manage quality digitally across the entire enterprise, customers will identify it for you through returns, recalls, and complaints. The solution is to embed your QMS software into other processes across the internal supply chain.
Plex QMS will automate quality by empowering complete supply chain visibility from vendor production to the point of sale. If you want to build a more robust culture of quality that reaches beyond the production floor to encompass all aspects of the supply chain, automate your demand and supply process with software.
Contact us to learn more.