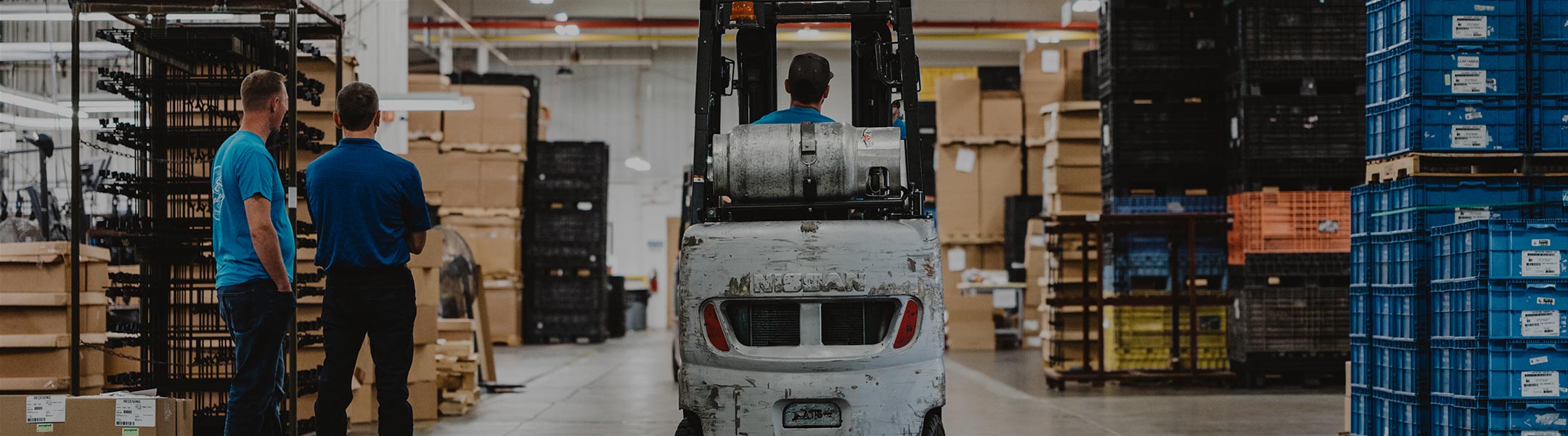
Get your copy of the 7th Annual State of Smart Manufacturing and hear from 300+ manufacturers in this new survey report!
For a monthly digest of expert insights, data points, and tips like the ones in this article.
There's an old business phrase that says that the customer is always right. While many companies have tied themselves into knots trying to service ever-changing consumer tastes, there is one area they often neglect to address in their efforts.
What if the message customers send points to your system more than your product? And what if the things they ask for require you to abandon a manual system or improve a disparate one? In that case, you must have an answer for when they knock.
Enterprise software has represented an attempt to improve service levels for decades. These systems were a leap forward from ERP and MRP systems to QMS and MES.
But with clunky user interfaces, prohibitive interoperability, and the need for regular updates and training, many companies wound up with a disparate patchwork solution that today cannot go far enough to respond to customer demands on operational processes. The answer lies in the execution; all solutions point to executing with real-time data and analytics to ultimately best serve customer needs.
Mass customization, small lots (or lots of one), shorter lead times, and continuous updates are only a few features your customers might expect. The only way to address these demands is by weaving a digital thread throughout your operation. That may lead you to a manufacturing execution systems (MES), but standalone versions with no ability to communicate across the enterprise to break down silos are not enough.
Instead, a digital thread is needed to tie these systems together. An MES as part of a true smart manufacturing platform allows companies to control processes and machines to execute with precision. This digital thread creates complete visibility by leveraging real-time data and advanced analytics to identify areas for process improvement that increase efficiency and uptime.
An MES within an intelligent manufacturing platform extends the reach of data to track parts and availability for maintenance and inventory to ensure materials are available when needed. Such a platform also empowers track and trace capability, which is critical to compliance today. This traceability also goes directly to the core of the information needed to satisfy the expectations of your modern customers.
Digital execution need not stop at an MES. The power of real-time analytical insights lets you automate extensively and orchestrate the tasks required for an intelligent manufacturing environment. A solution like Plex Automation and Orchestration connects to machine assets at the edge, allowing highly accurate and precise automation that reduces the need for human action even more.
A fully orchestrated MES enables tracking for quality, scrap, production, and many other KPIs. Decision-makers can use this information to create automated workflow to achieve more reliability and predictability while providing customers with continuous updates and visibility of their orders.
Let’s look at an example to understand the real-life impact. When Wisco Industries began receiving excellent customer feedback for things like integrated quality and advanced EDI for order tracking and confirmation, they discovered an opportunity to address customer requests that would give them an advantage in operational improvement.
By choosing Plex, Wisco was able to meet new customer expectations by eliminating data silos, automating processes, and implementing procedures that improved their operation. This choice resulted in a 20% reduction in overall inventory and a 15% reduction in raw material inventory. Wisco's use of Plex improved shop floor operations, making them more competitive while keeping existing and new customers happy.
A smart manufacturing platform with advanced MES capabilities removes redundant tasks and error-prone manual data. It allows you to focus on execution and orchestrate it across the enterprise from the machine edge up. The result is a smart manufacturing environment that can fully answer the door when customers come knocking, just like in the above example.
Learn more about this topic in the related article How Demand Drives Execution.