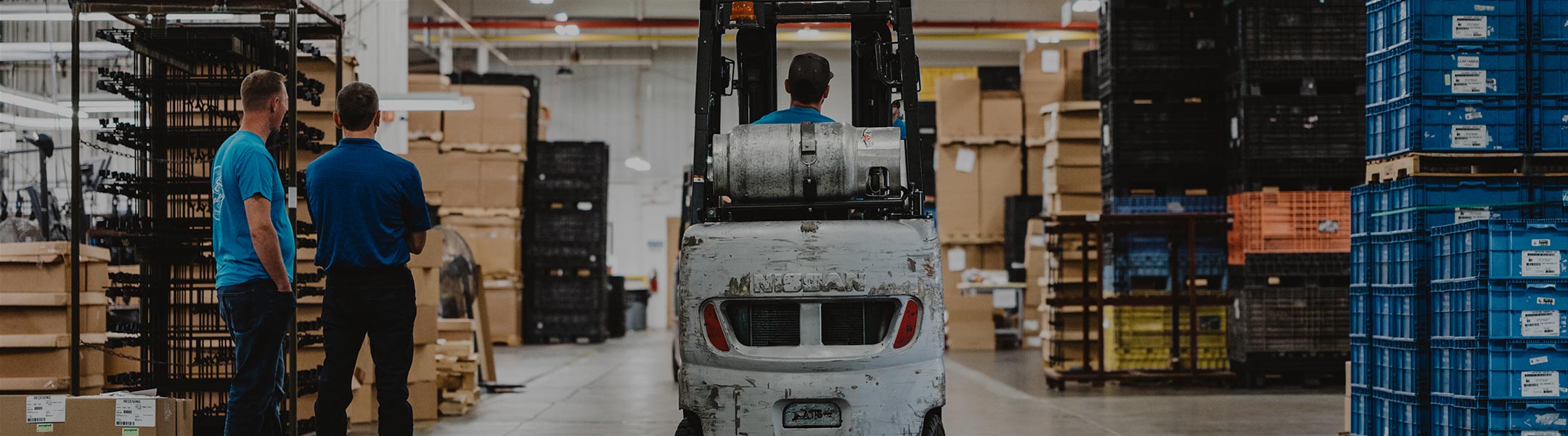
Get your copy of the 7th Annual State of Smart Manufacturing and hear from 300+ manufacturers in this new survey report!
For a monthly digest of expert insights, data points, and tips like the ones in this article.
You likely use some type of traceability procedure to comply with customer and market mandates and/or for service, safety, and process improvement purposes. However, if you are relying on manual processes, you are likely missing critical steps in the production process where errors may occur. You also open up your business up to a potential recall that could result in financial loss, illness, or even lost lives.
The Potential Impact of Recalls
For example, more than 36 million pounds of processed turkey products distributed to 26 states were recalled by Cargill, the third largest turkey processor in the U.S., for Salmonella Heidelberg bacteria. The investigation took five months from the first reported case of the illness to identify the source of the contamination. Why the long delay? There were multiple paths through a complex supply chain that needed to be tracked to find the cause of illness.1
You may also be aware of the more than 12 million vehicles in the U.S. being recalled for faulty airbag inflators. These inflators were identified as responsible for 11 deaths and more than 100 injuries worldwide. In a report authored by the U.S. Senate, the airbag supplier notified automakers that some of its traceability records were incomplete.2
Simply tracking the receipt of raw materials and shipment of finished goods may fulfill bare minimum requirements in some cases, but manual tracking can become challenging when raw materials are split from original shipping containers and used in multiple products throughout the facility. If there is an audit or recall, it can take hours or days to go back and trace where materials are in production—or in the supply chain.
Traceability is More Than Just Tracking Materials
A rigorous track and trace approach records virtually every movement and operation for high-resolution visibility. For every action in production, there is a transaction in the system. Real-time reports on machines, components, stations, shifts, and operators involved in the defective product and processes can be caught before the product is shipped. Barcode printing and scanning are tightly integrated so that all relevant information is consistent and controlled from the production database onto labels, including a library of customer-specified shipping labels that print automatically at ship time.
This level of traceability and genealogy creates a digital “family tree” that illustrates the parent-child relationship of each component and operation in production. An automatic genealogy that includes component details (batch/lot, etc.) production operations (date, machine, operator), and other information guides search and documentation both backwards and forwards (or upstream and downstream) from any item in question to its ultimate source or disposition.
Rigorous Traceability Makes Compliance Easier—and Faster
To meet compliance regulations, you need to prove that you can trace materials and components throughout production. A single, central database makes it easy to collect and store information from suppliers and lot numbers to expiration dates. All data is readily available, eliminating hours of manual labor often required to provide documentation for compliance. Instead of tracking documents or mimicking paper-based systems, real-time production data are available instantly—so your people can spend more time preventing recalls than responding to them.
Make sure the system that supports your traceability processes that not only tracks materials and components through the entire supply chain and as they flow through production but also can isolate problems to prevent them from becoming a costly recall.
See how one food and beverage manufacturer leveraged the Plex Manufacturing Cloud for end-to-end traceability and inventory accuracy, read the success story: Dominion Liquid Technology.
About Revolution Group
Revolution Group, an Ohio-based business and technology consulting firm, delivers IT, CRM, and ERP solutions to small and mid-market organizations in manufacturing and professional services. For over 20 years, Revolution Group has helped clients elevate their businesses with innovative technology solutions. With deep CRM and ERP implementation experience, and collaborations with the Plex Manufacturing Cloud, NetSuite, and Salesforce, Revolution Group is in a unique position to offer clients world-class cloud platform solutions and industry expertise. Whether you seek to improve business processes, decrease costs, mitigate business risk, or increase revenue, our team will work closely with you to deliver the innovative solution that meets your business objectives. www.revolutiongroup.com
1. End-to-End Traceability: Reducing Recall Risks for Food and Beverage Manufacturers. Plex Systems. June 2016.
2. Danger Behind the Wheel: The Takata Airbag Crisis and How to Fix Our Broken Auto Recall Process. U.S. Senate Committee on Commerce, Science, and Transportation. June 22, 2015.