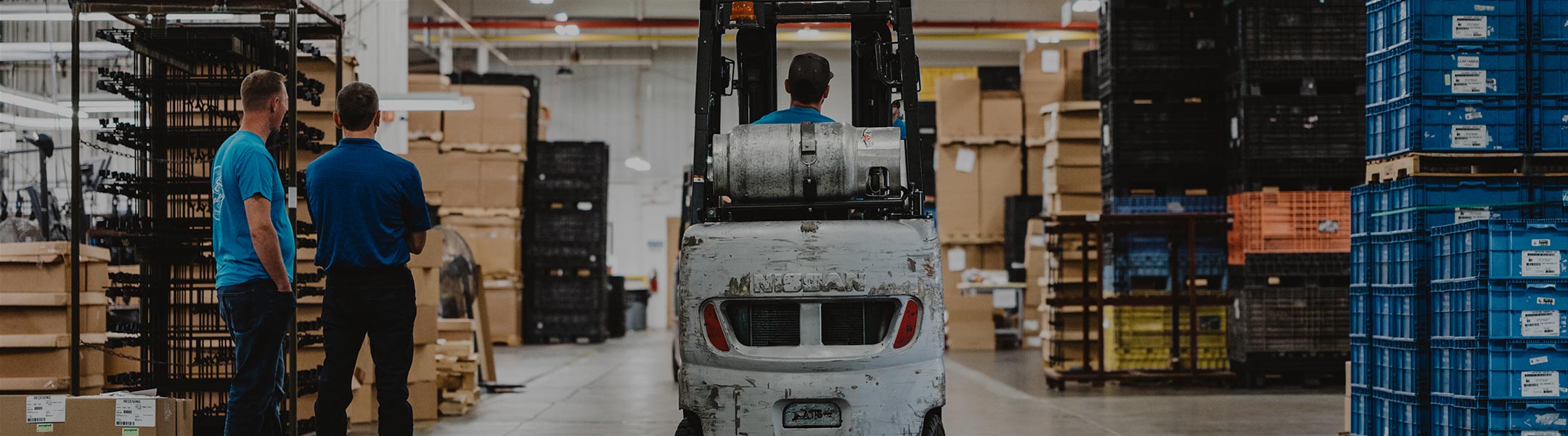
Get your copy of the 7th Annual State of Smart Manufacturing and hear from 300+ manufacturers in this new survey report!
For a monthly digest of expert insights, data points, and tips like the ones in this article.
Lead time variability is a problem in any supply chain / manufacturing environment. Just-in-time supplies don’t always work out that way: you order too soon or too much and now you’re carrying inventory on your supplies, possibly risking obsolescence. You order too late and even a small shipping delay can put production into a full stop. At the same time, demand variability can create disruptions for your production cycles too.
The ideal is to be able to order your supplies just in time for production needs, to meet the varying demands of customers. Variability exists in all aspects of a supply chain: customer demand, supply, production, and shipping, to name a few. Lead times can change at the drop of a hat, so the goal is to limit that variability.
But how?
There are many reasons that your lead time can get skewed:
The problem is that forecasting based on past needs isn't always accurate and can't factor in any of the above causes of variability. You need to get to a stage of predicting your needs, as well as possible disruptions to the supply chain.
Predicting customer demand isn't always possible so lead time variability can be even further skewed, beyond the causes mentioned above, but there are a few ways that you can close that gap a little more, resulting in better customer service response:
The goal is to maximize supply performance while minimizing any of the causes of lead time variability, both in demand and supply. With the availability of data to allow more predictive analytics to work in your favor, you can develop better processes and start limiting the impact of lead time variability on your production bottom line.