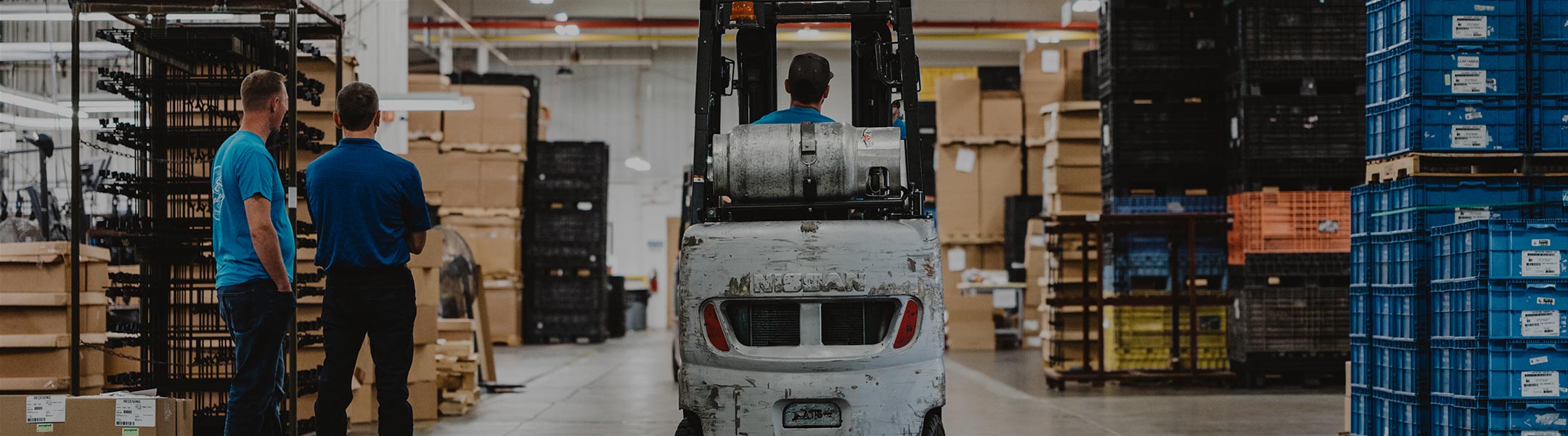
Get your copy of the 7th Annual State of Smart Manufacturing and hear from 300+ manufacturers in this new survey report!
For a monthly digest of expert insights, data points, and tips like the ones in this article.
Inventory is a sensitive issue for any company. Too little, and orders go unfilled. Too much, and precious capital is tied up, affecting equipment purchase plans, reducing cash flow, and even impacting taxation. Across a wide range of industries, lowering inventory costs is front and center in the minds of supply chain professionals.
Depending on the industry, there are several methods of inventory strategy. Each has advantages and disadvantages, and the type of product and nature of the market can impact which method is used. Key methods include:
Controlling and lowering inventory costs is a critical aspect of supply chain management. By optimizing several factors, companies can realize lower overall inventory costs and less impact on cash flow. Optimization techniques include:
Traditional best manufacturing practices used all the above strategies to manage inventory and lower costs. But even in the most successful companies, much of the effort was manual, limiting the accuracy and scope of detail. These systems often encountered erroneous data, human error, and bias in data. And the analysis was human-based and limited in capability.
Plex DemandCaster offers a comprehensive supply chain management planning software suite, including inventory forecasting and optimization. By using cloud-based software from Plex DemandCaster, companies can rely on accurate data that is at or near real-time to manage inventory and implement optimization strategies effectively.
The Plex DemandCaster system also allows robust “what-if” scenarios for contingency planning. It enables supply chain professionals to use advanced analytics and prescriptive and automated analysis to manage inventory and reduce costs. Companies implementing supply chain management software can see a 20-30% reduction in inventory costs.
To learn how Plex DemandCaster Inventory Forecasting and Optimization software can help you lower inventory costs and forecast with confidence, contact us today.