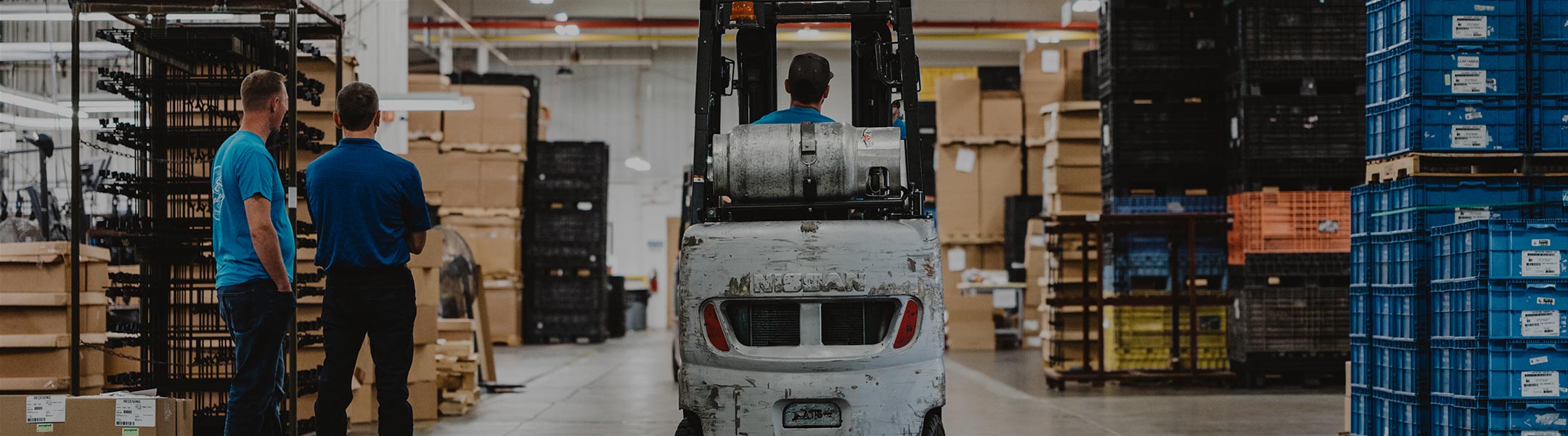
Get your copy of the 7th Annual State of Smart Manufacturing and hear from 300+ manufacturers in this new survey report!
For a monthly digest of expert insights, data points, and tips like the ones in this article.
A manufacturer’s inventory management strategy is a critical link between supply chain management and manufacturing. For years, there has been an increased focus on inventory optimization and controlling cost while ensuring an adequate supply of materials and components. But today, inventory strategies must include plans for dealing with issues beyond cost optimization
Gone are the days when a stable supply chain meant that inventory strategy consisted predominantly of Lean management methodology. An inventory management strategy today has two primary concerns. One is a flexible and agile strategy that acknowledges and plans for large-scale disruption. The second requires an inflation strategy to address year-over-year rising costs.
Until 2015, inventory management strategies looked for cost optimization. Global supply chain legs could be planned alongside local and regional suppliers to create a predictable forecast. Beginning with the tariffs and trade wars of 2016 and 2017, disruption upended that setting. These events were trumped by COVID-19, which saw events of congested ports and supply shortages where there had been none before.
The supply chain strategy to deal with these events shifted from Lean and JIT to a new combination of reshoring and nearshoring. By moving supply chains closer to the point of production, supply lines could be stabilized. But it meant higher costs and different realities for transportation and logistics. Disruption-based inventory strategies also included the return of buffer stocks and the increased space and holding costs associated with them. These buffer stocks, along with reshoring and nearshoring, returned some confidence to manufacturers at the expense of a traditional definition and method of inventory optimization.
Parallel to adopting a disruption-based inventory strategy, manufacturing companies have also had to adopt an inflation strategy. With year-over-year inflation tracking at its highest level in over forty years, supply chain professionals have had to face another reality that many in the profession have never had to experience, much less build into a supply chain model.
One fundamental change in strategy tips the scales further toward buffer stocks. To hedge against inflation, many companies have adopted higher order quantities. This hedge takes advantage of held inventory as an appreciating asset. But bumping into that decision is the need for additional warehouse space and associated handling and holding costs.
Depending on the size of the enterprise, larger order quantities may not be an option, and for those who can place volume orders, there is an inflection point for the value gained on the asset vs. those added costs. Larger order quantities aren’t ideal for food and beverage or pharmaceutical operations with tightly-regulated perishability and “use by” standards. These manufacturers may need to address higher costs by accepting smaller margins and using tax-favorable accounting for the increased inventory cost.
Another choice in inventory strategy is the method of inventory used. Companies use FIFO, LIFO, or averaged strategies most commonly. The best method for inflation depends on the industry the planners are in and what works best for the company. The strategies a company maintains during an inflationary period will affect its turnover ratio or inventory “turns.” Using FIFO, a COGS statement will reflect the lower cost, and using LIFO, it will reflect the higher cost. Others may temporarily use an average costing (for example, process or commodified materials).
Supply chain professionals must determine what works best for their enterprise. The best inflation strategy must also include an assessment and choices based on purchasing power. Companies may need to adjust order quantities depending on the cash flow, use of inventory financing, and other variables. Or, they may need to consider ABC analysis and “what-if” contingency planning to secure the most profitable product lines.
Ongoing disruption and inflation are causing a complete reassessment of traditional inventory strategies. They require a different mindset and new tools for supply chain professionals and decision-makers, enabling them to redefine optimization to address the new normal. Manual inventory optimization was always extremely limited in scope and effectiveness, and it’s impossible with the double threat of disruption and inflation.
Supply chain management software solutions from Plex DemandCaster offer the agility and flexibility required to develop the best pricing strategy for each manufacturer. Inventory optimization software from Plex DemandCaster improves inventory tracking and provides more accurate and automated reordering that changes dynamically as reality changes.
While inflation will always be more costly, the software can respond and provide insights for the most optimized cost for the current reality. With Plex DemandCaster, manufacturing supply chain planners can make data-driven decisions that improve all supply chain operations, keep production running smoothly, and accurately forecast in a demanding environment.