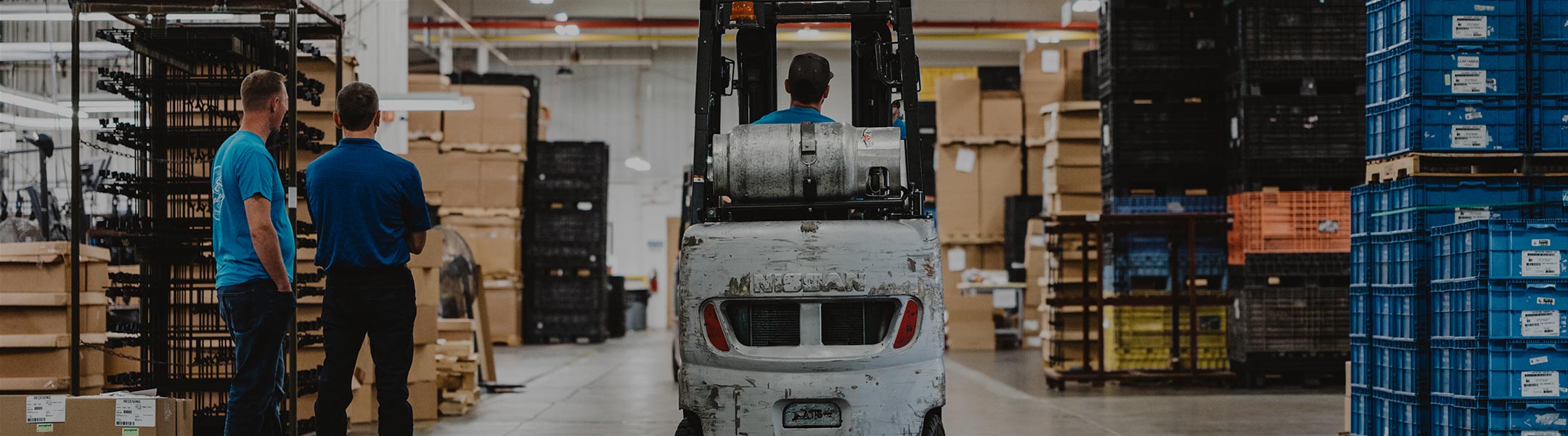
Get your copy of the 7th Annual State of Smart Manufacturing and hear from 300+ manufacturers in this new survey report!
For a monthly digest of expert insights, data points, and tips like the ones in this article.
Manufacturing facilities are filled with expensive equipment. Multi-million-dollar investments can make, or break, a company’s ability to compete and grow. But in today’s connected shop floor environment, smaller, low-cost tools are delivering competitive advantage.
Today, sensors and smart tools are helping manufacturers produce higher-quality products at a lower cost. Let’s take a look at the impact these devices are already having.
While some manufacturers still leverage whiteboards and tracking sheets for inventory, modern manufacturers now use sensors in the form of low-power Bluetooth, smart tags, and even RFID tags to maintain visibility of any item that remains in constant motion during manufacturing.
Consider the journey of raw materials that begins at a supplier site. Material is transported via truck, ship, etc. to a manufacturing plant. From there, it is transformed into a final product. Along the way sensors, tags and smart labels, coupled with ubiquitous wireless and cellular networks, allow manufacturers to monitor and trace both the materials and their path to product.
Not only can these sensors track location, they can report data about the temperature and turbulence materials endure en route. The cost of these new technologies today can be anything from a few dollars down to a few cents, putting experimentation and trials on the shop floor well into reach for most operations.
Cloud ERP systems are a huge catalyst for data collection and sharing of complex manufacturing, design, and costing information. Unlike legacy systems, adding the connectivity required to grab data from new sensors and tags doesn’t require new development or a new hardware stack.
Smart tools that connect to a cloud ERP system are a key aspect of the ongoing cycle of innovation and cost reduction because they make highly complex production lines possible. The torque wrench is a perfect example. For more than 100 years, the torque wrench has been an essential tool for manufacturers because it applies specific torque to a fastener, such as a nut or bolt. The ability to apply a specific amount of torque can make the difference in the performance of an end product.
Today, connected torque wrenches can automatically adjust based on individual product specifications, accelerating the speed of production, improving the accuracy of execution and traceability. For a torque wrench in the assembly of a complex part:
The IP torque wrench is one example of how manufacturers can improve operations as they increase the connections between people, tools, and products on the plant floor. Like sensors, up-front costs are going down dramatically. At the same time, connectivity inherent in new Cloud ERP solutions makes adding smart tools to a connected manufacturing environment simple. Instead of traditional design/development processes involving extensive custom code and bespoke systems, tools like IP wrenches and quality testing gear can be added to shop floor operations in minutes. Looking ahead, it may not be the most expensive tool in the shop that has the biggest impact.