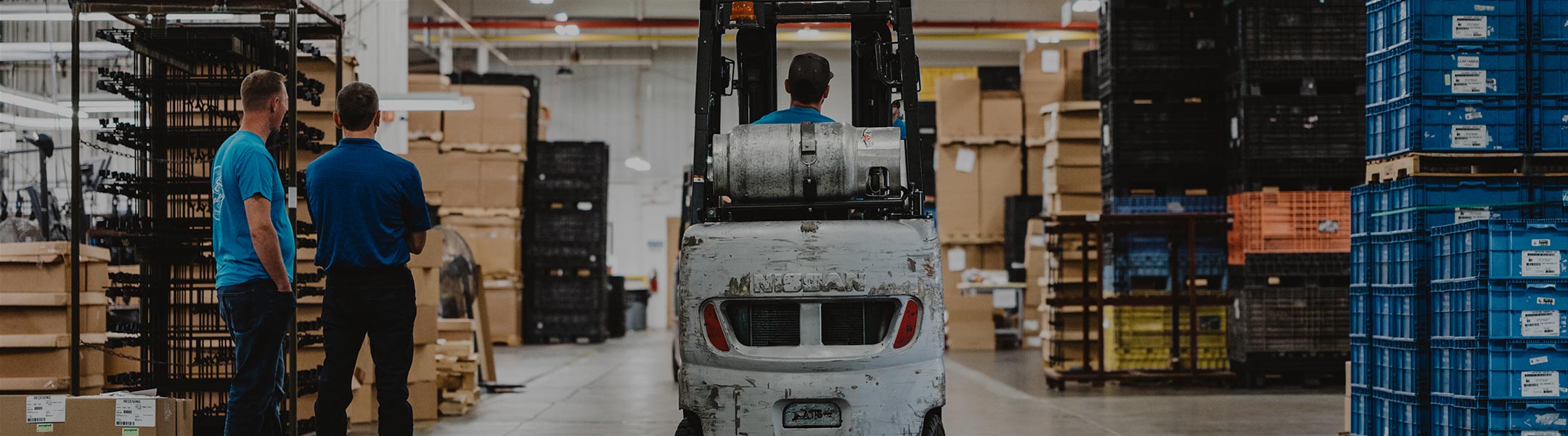
Get your copy of the 7th Annual State of Smart Manufacturing and hear from 300+ manufacturers in this new survey report!
For a monthly digest of expert insights, data points, and tips like the ones in this article.
Having a sound strategy can make all the difference in war, life, and business. With it, there are clear goals and directions on where you are going and how you will get there. Without it, you risk wandering, moving from band-aid to band-aid to fix problems.
Transforming your business and growing it into the future requires a clear smart manufacturing strategy backed by modern technology. With this strategy in hand, your team can make well-informed decisions that move from the “where” and “how” of deployment to equally well-informed tactical decisions that unlock the “what” that you can achieve.
Once a sound strategy for smart manufacturing adoption is in place, companies have a wide range of tools. They can begin to plan the tactical, concrete steps of putting the platform to work. This may include specific process improvements, efficiency goals, cost reduction, and more.
But getting to the point of action requires a deep dive into the nature of the operation and what is needed. It requires a commitment to transforming an enterprise to adopt smart manufacturing to change its business processes from top to bottom.
A smart manufacturing strategy is equivalent to "walk before you run." And this strategy should include several key components.
Connectivity is a critical part of your smart manufacturing adoption strategy. Typically, a manufacturer will have a fleet of equipment from multiple OEMs.
Machines may also be widely different generations, even if the equipment is from the same OEM. And still, other machines may have model differences, size variances, and a mix of digital and analog outputs.
Your strategy should specify how much of your equipment will be connected. This detail will determine how much data will be collected and should also set out how connectivity differences will be overcome. For example, if equipment requires retrofitting sensors or cabling, will your implementation include full connection or only those most convenient?
A smart manufacturing platform includes powerful automation options. This automation is often a replacement for manual data collection. Or it may include automating machinery to make autonomous or semi-autonomous decisions. Yet still, automation can consist of alarms and alerts to notify operators and maintenance of critical operating issues.
Your buy-in and the resources available for deployment will limit the amount of automation you leverage. But the more you automate, the more your smart manufacturing platform will collect data, analyze it, and deliver actionable insights for the best performance.
Once the level of automation is determined, you can focus on what to track. Smart manufacturing connects systems across the enterprise, including interoperability with legacy software systems, and it also connects people from operators and techs through managers and execs.
These staff members will consume the data tracked and the analysis rendered within reports, charts, dynamic HMI displays and dashboards, and other visibility tools. A smart manufacturing strategy doesn’t just unlock data; it also must determine what should be tracked and what systems will be included in the ecosystem.
Analysis lies at the core of a smart manufacturing platform. Real-time data powers a cloud-based analytics engine that delivers actionable insights to improve decision-making, drive automation parameters, take autonomous action, alert staff, and more.
The analysis also uncovers hidden production, quality, waste, and performance trends that would otherwise go undetected. If the strategy includes plans for a deeply connected and automated system, the quality of the data and insights significantly increases.
The tablets, PCs, and HMIs on a smart factory's floor display the platform's visibility. Here, operators and staff utilize KPIs in customizable dashboards to see what is happening and determine how to respond accordingly.
Your strategy should include what KPIs will deliver the greatest value to the operators and staff accessing the production equipment across the shop floor.
When you have set your smart manufacturing strategy at the company level and implemented a system that fits your operation, tactical performance is unlocked to let you drive change and improvement throughout the operation. These tactical actions may include improved training, continuous improvement programs that are themselves automated, quality monitoring, and even new inventory and supply chain actions.
This Smart Manufacturing Software Buyer's Guide is a resource for understanding the elements of developing a strategy for adoption. It also contains critical trends, technology forces, and implementation recommendations that help you find the right software for your needs.
Click here to discover the latest insights in the full guide.