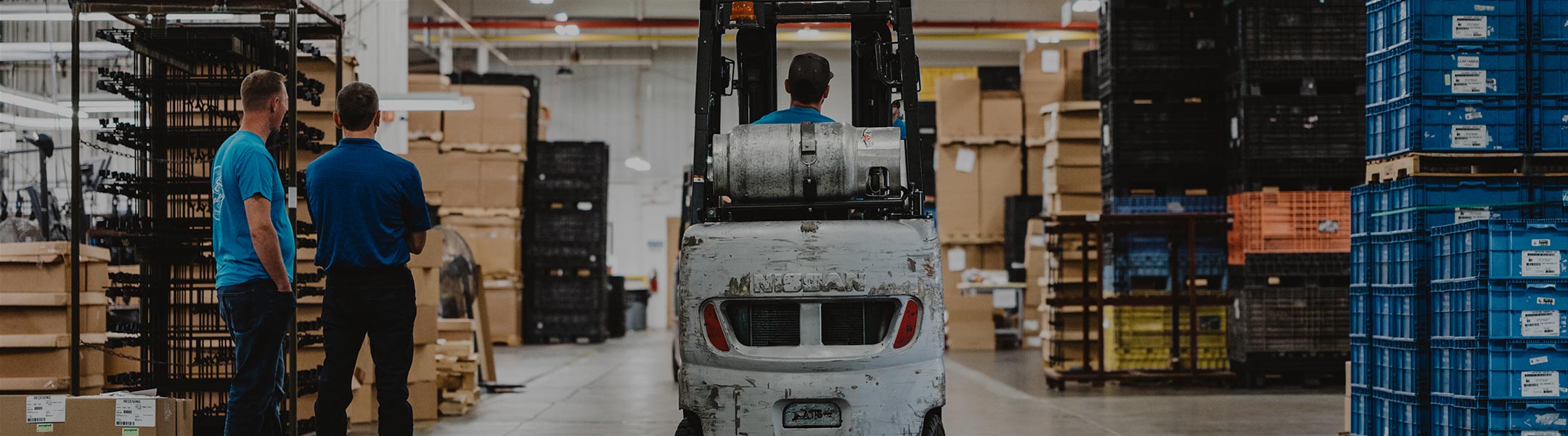
Get your copy of the 7th Annual State of Smart Manufacturing and hear from 300+ manufacturers in this new survey report!
For a monthly digest of expert insights, data points, and tips like the ones in this article.
Manufacturing is undergoing a renaissance. Through robotics, AI, machine learning, virtual and augmented reality, and more, digital manufacturing is being leveraged for greater efficiency, new products and services, and process optimization.
The newfound control and utilization of machine-generated data enables companies to weave a digital thread through all their business practices and enhance value throughout the entire enterprise. But what about skilled trades? Where do they fit into this new business model?
When people think of skilled trades, they might think of machine operators, fabricators, electricians, welders, and other professions where skillset, physical labor, and art combine. A common misperception is that these trades are replaceable in the new digital manufacturing world.
But this impression misses the focus of digital manufacturing. While robots will perform tasks faster and AI analytics will process data and offer paths not considered before, the need for skilled trades will evolve, not disappear.
A four-year degree has always been perceived as a ticket to a high-paying job. But as technology advances and manufacturing becomes as much a digital endeavor as a physical one, the need for technical skillsets will increase. That same push for more tech-savvy employees will lead to the evolution of skilled trades incorporating digitization into their discipline.
The growing trend of digital manufacturing means that many high-tech, good-paying jobs won’t require a four-year degree. Instead, it will come down to a greater emphasis on training for technology and digital transformation within skilled trades and in areas where current and future employees already have an interest. This leaves many who will be entering the workforce soon to question whether the traditional college path makes sense.
As staffing shortages in manufacturing worsen, there is already a move toward these skilled jobs and higher incentives with better quality of life and working conditions. This shift in perception coincides with the digital revolution creating new opportunities.
Skilled trades were long considered to be focused on manual labor and even somewhat dull compared to other career paths. But those entering the workforce now and in coming years have been raised on technology and gaming. Their early exposure to the same types of intuitive systems and gamified learning means that they’re familiar with the kind of user experience being brought into trades jobs.
This history and comfort with the technology that’s powered their entire lives make them easier to train, retain, and keep interested. In short, many skilled trades will see a decrease in traditional, physical labor and instead focus efforts on managing technologies such as:
The Plex Smart Manufacturing Platform helps manufacturers connect their factory and unsilo systems to unlock the power of their data. MES, ERP, Supply Chain Planning, Production Monitoring, and Asset Performance Management solutions unlock the power of technologies like the above, generating analysis and insights that can be used by skilled trade employees. Not only does that enable them to be more efficient, but it also empowers them to focus on their most value-added and impactful responsibilities. The result? Jobs that continue to make a difference and have security long into the future.
Click here to learn how the Plex Smart Manufacturing Platform can help your company achieve digital transformation and empower all your employees.