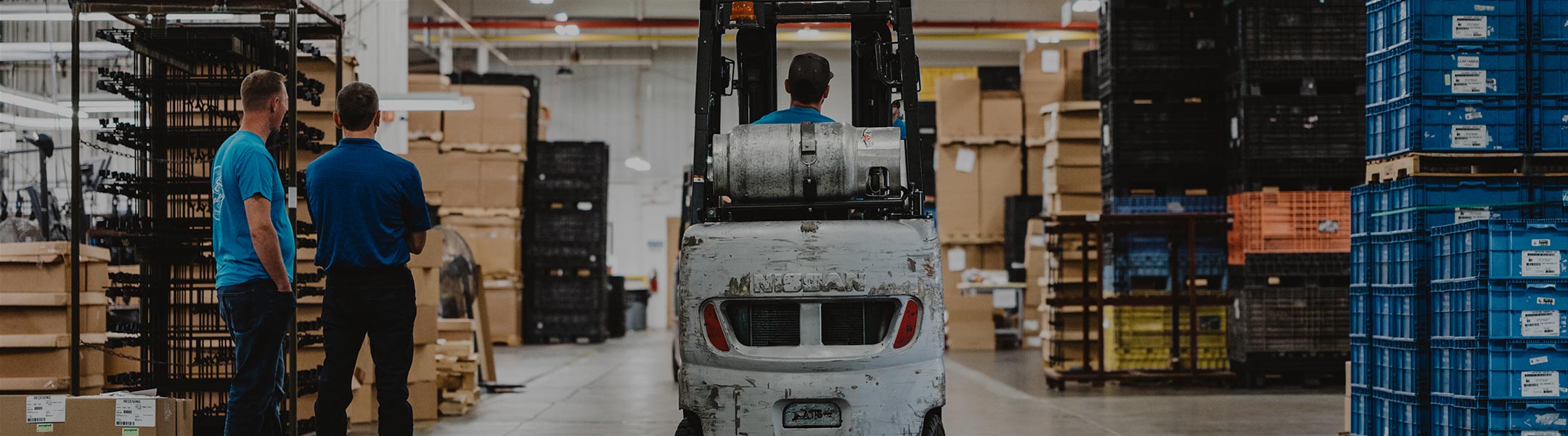
Get your copy of the 7th Annual State of Smart Manufacturing and hear from 300+ manufacturers in this new survey report!
For a monthly digest of expert insights, data points, and tips like the ones in this article.
Staying competitive is often the No. 1 concern for today’s aerospace and defense (A&D) manufacturers.
Key components to these efforts include successfully triangulating cost, schedule, security, scope and reliability constraints, all in order to improve supplier orchestration and time to market.
But where to start? Many A&D manufacturers agree that the first step in managing these many constraints is getting suppliers involved early in projects.
Studies measuring the impact of early supplier collaboration have shown that an active role in project planning, compliance and quality management leads to reduced product errors and lower sourcing costs (Bandyopadhyay, 2005) (Humbert, 2009).
Beyond the immediate project, collaboration can also become a catalyst for process and product innovation.
In the automotive industry, the Toyota Production System teams work to make collaboration more powerful than price. Through well-orchestrated collaboration, the teams have seen reductions in error rates so significant, the time it takes to produce a new model has dropped significantly (Dyer, Nobeoka, 2000).
While security concerns will often drive A&D manufacturers to turn inward to solve product costing, quality, process and cultural challenges, the highest-performing manufacturers are developing secured collaboration links to their suppliers — which leads to greater knowledge transfer and more clarity of project requirements.
Using secure cloud-based applications and supporting platforms to integrate with suppliers, A&D manufacturers are gaining many competitive advantages:
Bottom line: Improving time to market, reducing the cost of quality and exceeding continually higher expectations starts when A&D manufacturers look to collaboration enabled on cloud-based platforms to make constraints manageable. Transforming cost, schedule, security, scope and reliability constraints into competitive advantages starts when A&D manufacturers increase their ability to turn data into intelligence.
References:
Bandyopadhyay, J. K. (2005). A model framework for developing industry specific quality standards for effective quality assurance in global supply chains in the new millennium. International Journal of Management, 22(2), 294-299.
Cressionnie, L. L. (2011). Hand in hand. Quality Progress, 44(7), 62-64.
Dyer, J. H., & Nobeoka, K. (2000). Creating and managing a high-performance knowledge-sharing network: The Toyota case. Strategic Management Journal, 21(3), 345-367.
Humbert, E. R. (2009). The impact upon key performance measures in applying lean enterprise initiatives by defense contractors. (Order No. 3381836, University of Phoenix). ProQuest Dissertations and Theses, 148-n/a.
Kim, S. (2008). Performance-based logistics: Incentive contracting in the aftermarket. (Order No. 3328601, University of Pennsylvania). ProQuest Dissertations and Theses, 205-n/a.
Kim, S., Cohen, M. A., & Netessine, S. (2007). Performance contracting in after-sales service supply chains. Management Science, 53(12), 1843-1858.
Lee-Mortimer, A. (1993). A dynamic collaboration. The TQM Magazine, 5(1), 31.
Penny-Anne Cullen, & Hickman, R. (2001). Contracting and economic alliances in the aerospace sector: Do formal contact arrangements support or impede efficient supply chain relationships? Technovation, 21(8), 525-533.
Usman, A., & Kidd, C. (2013). Critical success factors for configuration management implementation. Industrial Management + Data Systems, 113(2), 250-264.