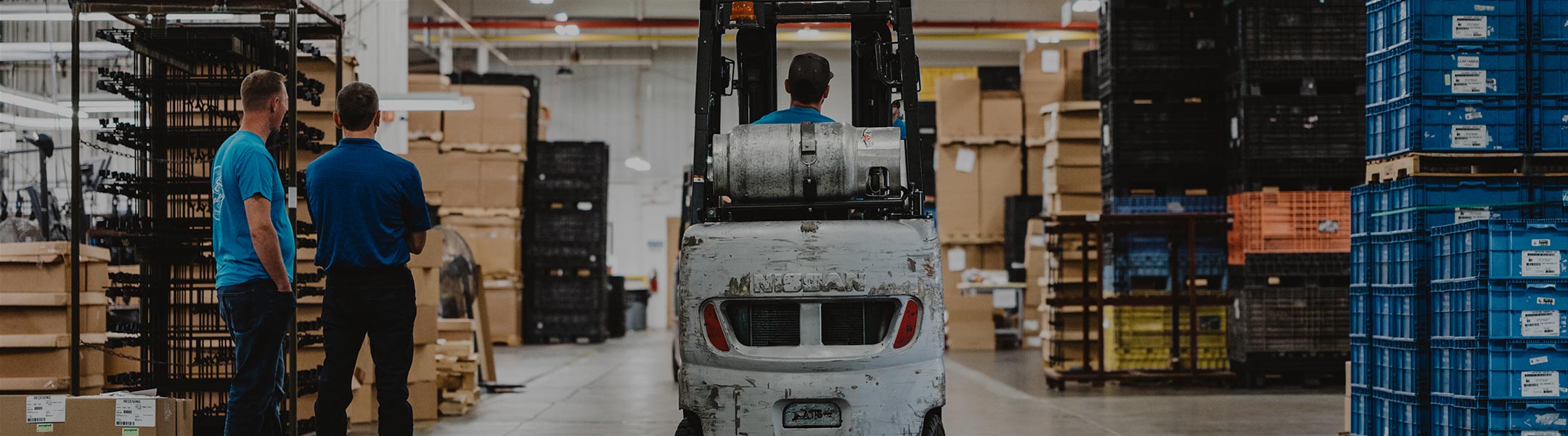
Get your copy of the 7th Annual State of Smart Manufacturing and hear from 300+ manufacturers in this new survey report!
For a monthly digest of expert insights, data points, and tips like the ones in this article.
Most companies use Material Requirement Planning (MRP) software, or an MRP module of an ERP, to plan and manage the purchase, production, and transfer orders of finished goods and components based on a demand plan or forecast. It is time-phased and can manage large numbers of materials—and bill of materials—to ensure the right components are ordered and on hand to support production-scheduling software.
Yet, MRP systems cannot do everything. Materials Managers have to ensure that data is accurate, and supply attributes are set optimally, which can be non-trivial and can make or break the effectiveness of an MRP:
All of the above data is crucial in their own right, but they also contribute to the calculations of re-order points and buffer inventories for all finished goods and materials. MRP systems generally do not calculate or evaluate re-order points and inventory buffers. In the rare occasions that they do, they might not be using the calculations best suited for your particular business.
This depends on the growth or decay of the business in general. It also depends on the volatility of the business environments. According to ISM in the "The Next Challenge for Global Growth: Keeping Up With Demand" article published in the April 24th edition of the Wall Street Journal: Economic data are also showing a constrained supply side. The Institute for Supply Management’s index measuring backlogs of orders in manufacturing has reached its highest level since May 2004. Set against robust demand, supply chains are “struggling to keep up,” the ISM says.
Regardless, if the issue is demand or supply related, MRP systems are not suited for analyzing and resetting demand and supply attributes on a continuous basis. Most companies do these calculations and evaluations themselves in home-grown software or spreadsheets. Others use third-party software specifically designed to size and calculate the inventory parameters on a rolling basis, while populating the MRP with re-orders points and buffers over the next 6-12 months.
The bottom line is that MRP systems are very good and may be the central engine for managing inventory and ensuring customer service. However, MRP systems require good data and the setting of optimal parameters to run effectively. This includes the periodic recalculation of re-order points and buffers often best done by specialty software such as DemandCaster.
It is interesting to also note, when we first built DemandCaster it was done so with the inclusion of a robust MRP engine in order to properly visualize the impact of demand and supply on both a short- and long-term basis. By better visualizing your reality, we help you move from reactive responses to more proactive decisions.
Today, many of our customers prefer to use DemandCaster in place of their ERP systems since it moves all the MRP-related parameters out of your ERP's black box, making it easier to modify settings and view the impact before taking action. These orders can then be pushed back to your ERP for execution.