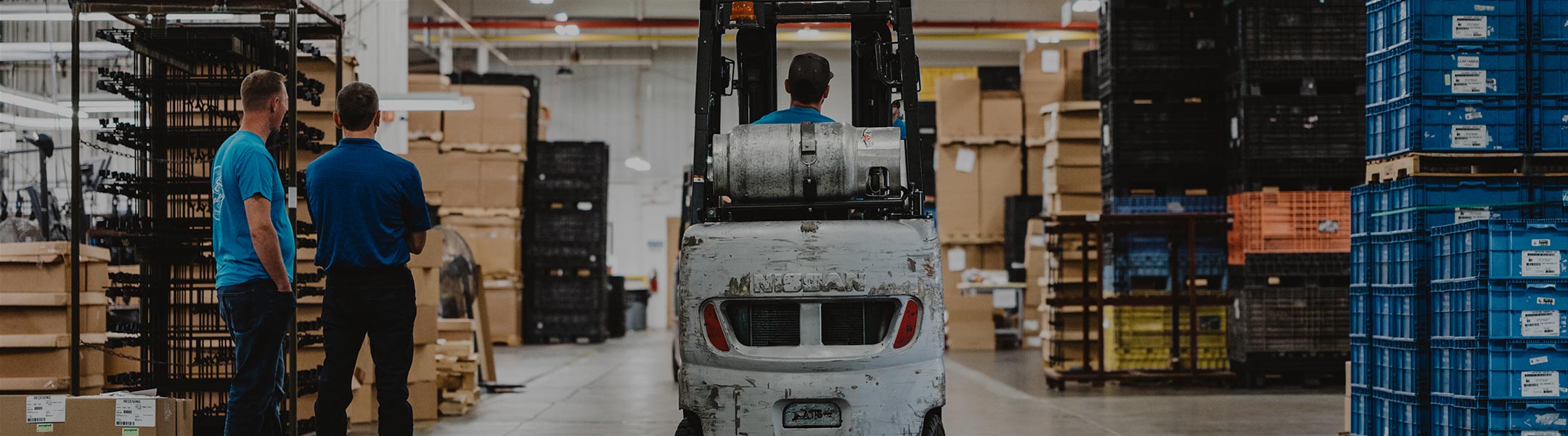
Get your copy of the 7th Annual State of Smart Manufacturing and hear from 300+ manufacturers in this new survey report!
For a monthly digest of expert insights, data points, and tips like the ones in this article.
Unless you have supernatural abilities, you’re like most humans who can’t accurately predict the future. But as a manufacturer—you need an effective way to “see” into future customer demand so you can allocate the right amount of inventory, optimize production, and keep customers happy.
Since a crystal ball with the ability to predict the future doesn’t exist, you possibly rely on spreadsheets, informal input from your cross-functional teams, and even your gut instinct to do supply chain planning. You’ve likely discovered that these processes are far from accurate. If only there were a magical crystal ball.
Luckily, you can look to organizations like APICS—the world’s leading community for supply chain excellence. APICS states that organizations with mature, digital financial and supply chain planning processes have results like:
How? I can tell you that these organizations don’t use a crystal ball. They do use an integrated business planning system. These organizations collect and leverage data (like order history, demand forecast, capacity constraints, available inventory, and prior commits) to gain a holistic view of the business. With this view, they gather cross-functional input from sales, marketing, engineering, and operations, and finance to add to the plan. This plan informs their strategy and their corporate strategy influences this plan. Then, they continually synchronize operational and financial systems so all information is up to date and ensure that the plan is operationalized and executed. And when things change, the plan gets updated and everyone has access to it so they can respond appropriately.
We call this connected manufacturing. It’s the foundation for successful planning and execution, and if you’d like to share and discuss this with your colleagues you can download an infographic about it here.
You can also read The Definitive Guide to Connected Manufacturing, which will give you a comprehensive, step-by-step overview of this strategy our customers tell us gives them a competitive advantage.