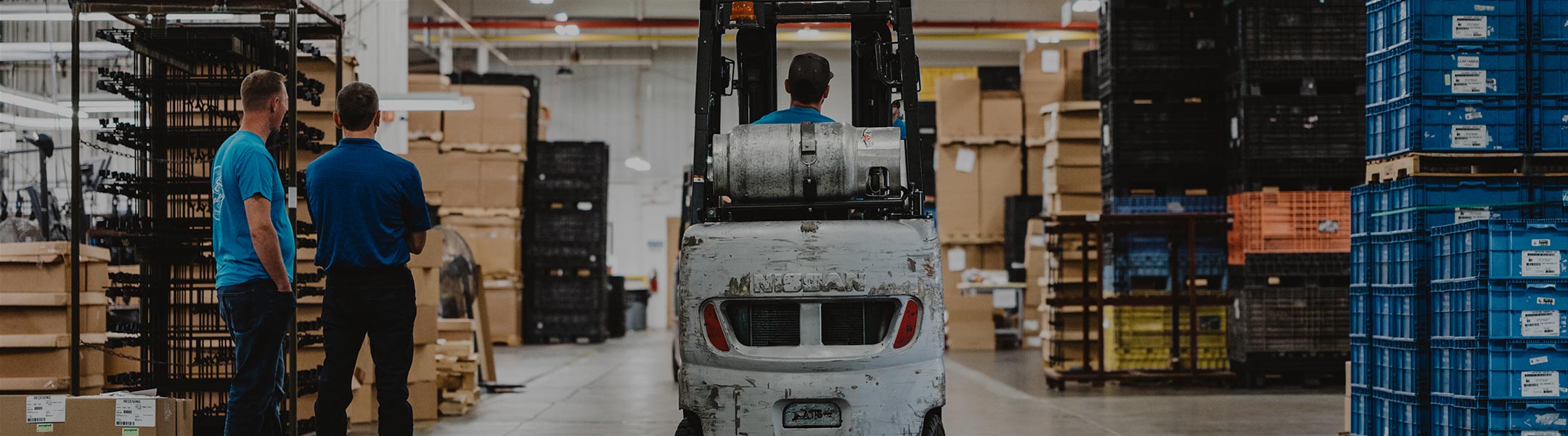
Get your copy of the 7th Annual State of Smart Manufacturing and hear from 300+ manufacturers in this new survey report!
For a monthly digest of expert insights, data points, and tips like the ones in this article.
Supply chain planning can be a daunting task. And, as economies globalize at a faster rate, just keeping pace will become increasingly difficult. Studies have shown that as much as 21% of a company’s performance is impacted by its global supply chain network. Further, it is estimated that to maintain the same level of “value-added leverage” realized today, companies must increase the global reach of their supply chain efforts by an additional 43% by 2023.
For large companies with the advantage of size, increasing the global reach of their supply chain is a difficult task, but one that can be absorbed operationally with less disruption. These companies usually have the available skill sets and the appropriate planning software as well as ERP software required to manage many of the challenges.
But for small and medium-sized companies without that degree of scale, there are several factors that can make the task even more difficult. For one, many small to medium-sized companies operate with varying levels of planning skillsets. Often, planners’ duties are combined with other tasks that must be managed outside the supply chain. And, in addition to the “many hats” conundrum, those same skillsets may not have had the benefit of professional supply chain training.
Secondly, many small to medium-sized companies employ disparate planning methods consisting of a collection of spreadsheets and notes, as well as anecdotal evidence and “gut feel” assumptions. But as the complexity of the supply chain increases, spreadsheets become harder to reconcile in a single workbook. Additionally, anecdotal evidence is often wrong and gut feelings become less effective in decision making when variables such as tariffs, government certification requirements, increased regulation, and others are introduced.
Many companies manage supply chains with suppliers and vendors in different parts of the world. Some raw materials and components are sourced locally, others regionally, and many from across the globe. There are different variables that drive the logic behind sourcing, but the result is that most modern supply chains have multiple legs that vary in length.
Short supply chain legs consist of local or regional suppliers. Often, these suppliers can offer lower quantities for more effective just-in-time (JIT) planning as their goods are usually available within a few days or, in many cases, on the same day. Lead time is less a factor as transportation for these vendors may be a matter of courier arrangements with FedEx and UPS or arranged through third party delivery or less than truckload (LTL) shipping. In cases where expedited shipping is called for, the cost is often acceptable when compared to urgency or total order value.
Long supply chain legs consist of cross-continent or international suppliers. To capture price benefits, minimums are often higher in the form of truck or container load. Lead times are longer and many additional costs such as landed costs, customs duties, and freight forwarder charges must be considered. In long supply chain legs, expediting freight may be cost prohibitive.
The reliance upon different lengths of supply chain legs has a strong impact on how the supply chain is managed and what decisions are made. It also affects the planning and scheduling efforts regardless of whether the planning system is optimized through software or is manually managed. The following are a few of the variables to consider when managing different supply chain leg lengths:
Long supply chain legs usually require higher minimum purchase levels. In the case of small to medium-sized companies, this may result in the need to buy excess inventory of raw material or components and could tie up cash in held stock that either moves slowly or not at all. Planners are faced with lower per unit costs for raw materials as an absolute on the spreadsheet, but when compared against order position, costs are often more per unit over time. But, the use of archaic and overlapping methods for planning may make this difficult, or even impossible, to see until after the fact.
Shorter supply chain legs may cost more up front but may be of benefit if the product can be ordered for JIT applications. However, the inability to see the impact of these realities prohibits effective decision making as the requirements for purchasing, holding, and allocating inventory are so different. This problem may be especially acute depending on which production method is used, especially in made-to-order (MTO) and assemble-to-order (ATO) production environments.
When supply chains are stretched across the globe, the length of the chain may impact product cost. And, with the complexity of the modern supply chain, cheaper isn’t always better. For a small to medium sized company, holding excess stock due to a lower purchase price may lead to higher costs in terms of warehousing, labor, and reduced cash flow. In some cases, large component orders may even exceed available space.
For locally sourced material, the reverse may be true, as having access “today” may become an overriding consideration with purchasing when valuable data such as total volume needed could justify larger and less costly shipments from a global supplier. In these cases, it is the inhibition of inadequate systems to identify the best option and provide actionable alternatives that drive cost.
Short supply chain legs are easier to manage. From common language and culture in communication, to distance as an absolute, short legs have fewer variables and regulatory hurdles to overcome. Long supply chain legs often carry added variables that must be managed.
When sourcing overseas, a planner/purchaser must consider things such as total landed cost, freight forwarding negotiations, customs, tariffs, regulations, certification, and a host of other concerns. This requires a higher level of skills and planners may be slowed or prohibited from effectively addressing these issues as they sort through spreadsheets to find the data needed to make decisions. This also increases labor required for effective planning as information is discerned after the fact, eliminating the capability for trend analysis.
Many companies rely on forecasting or some form of multiple iteration “what if” planning. But if the day to day management of supply chain segments is complicated due to leg length, planners may find themselves with vastly different data sets that are difficult to reconcile to produce an effective “what-if” forecast. Manually balancing a container load with a twelve-week lead time and extensive landed cost considerations against lot sizes of smaller quantities that are readily available same or next day is difficult.
As the need for accurate and actionable data increases, and as companies struggle with an increasingly complex supply chain comprised of different leg lengths, software to manage the data is imperative. Many platforms exist to allow planners to manage the data in real-time to smooth out differences impacted by supply chain leg length—differences that cannot be managed with only human analysis. Such software helps reconcile supply chain leg length in several ways:
As supply chains mature and as global supply chain footprints increase, the need for effective software platforms is clear. By deploying planning software, decision-makers can act strategically and tactically and make rational decisions based on real-time data to even out differences in long and short supply chain legs.