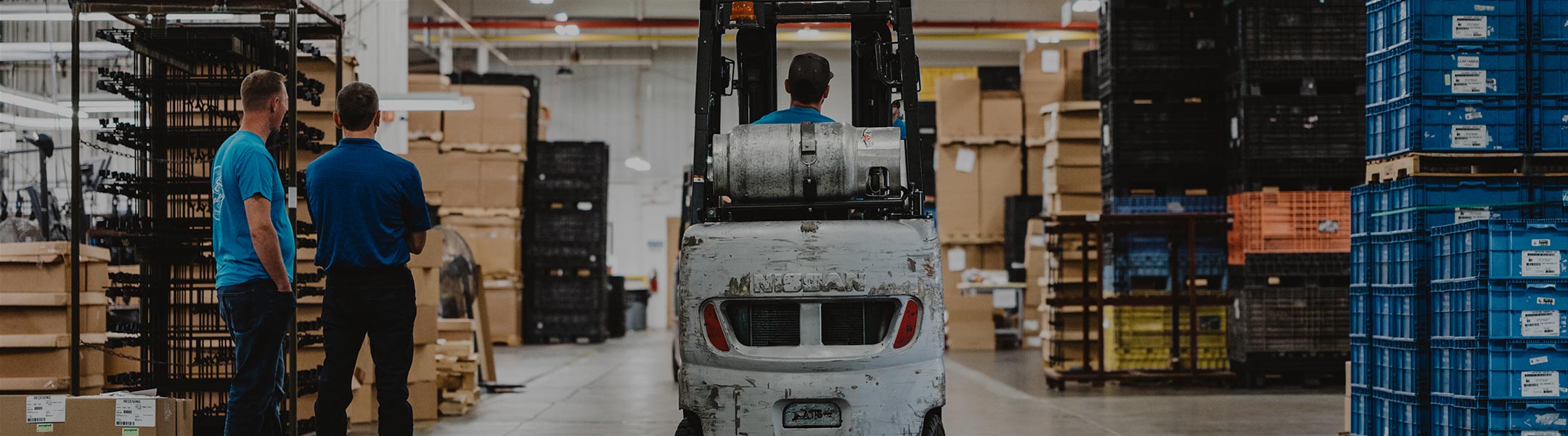
Get your copy of the 7th Annual State of Smart Manufacturing and hear from 300+ manufacturers in this new survey report!
For a monthly digest of expert insights, data points, and tips like the ones in this article.
In today’s world, the system of vendors, activity, and data required to source, produce, and deliver products to customers is increasingly complex. And the supply chain represents the steps required to make this happen. But as product companies extend their reach globally to capture the lowest material and operating costs, managing the supply chain has become increasingly difficult.
One major component in any supply chain is raw materials, the unprocessed materials, components, or partially finished assemblies that are required to build or produce a product. These are both the building blocks and the starting point for any final product and ensuring adequate supply and proper management of raw materials is critical. Moreover, they represent an investment that affects the cash flow and financial health of an enterprise as the cost is accrued at the point of acquisition and is listed as a current asset on a company’s balance sheet. As a result, it is important to use best practices for managing raw material inventory.
There are two basic subcategories of raw materials. Direct materials are those that are incorporated into the final product. Whereas indirect materials (often referred to as supplies or consumables) are not included in the final product but include things such as oils, rags, cleaners, markers, gloves, support material, and many other items used in the making of the final inventory items. Both types must be included in materials planning to ensure enough material is on hand to build the required number of units to fit the sales position or sales projection. It is also critical to plan for any established “safety stock” to address quality fallout, returns, or buffer stock against sudden increases in demand.
Materials planning is the method used to determine the requirements and quantities of raw materials to implement production. Many companies use traditional Material Resource Planning (MRP) systems to help calculate the requirements for the current product mix. Materials planning may also include data based on past consumption. And in many cases, while it is always better to calculate than to predict, materials planning may include forecasting due to seasonality, market volatility, or other external factors.
Purchasing is also a key fundamental in maintaining the correct level of raw materials inventory. As material requirements take shape, purchasing must coordinate the flow of materials into the production process on time and in the right quantities. And in a global economy that utilizes far-flung supply chains, this is no easy task.
Factors that complicate the purchase, and therefore influx, of raw materials, include:
All these factors come into play and bring focus to the importance of keeping track of raw materials inventory. As a critical part of a delicately balanced ecosystem, managing raw materials inventory can make or break the supply chain effort. As the material plan and purchasing coordinate to deliver raw materials, there are several issues to watch for and manage tightly:
Overstocking can result from many factors outside of the traditional slowdown in order position, including:
Understocking too can result from several different factors and threaten productivity through work stoppage. These factors include:
Quality management and traceability should be built into any supply chain. But when it isn’t, quality rejections for raw materials can cause severe shortages or increased costs due to expediting. Compliance issues are also a concern for assemblies and subassemblies for parts such as electronics and automotive parts where full traceability is often regulated by the receiving country’s government.
These concerns are important for any company, but small to medium-sized companies often face a heightened level of exposure when raw materials are not adequately managed. Each variable adds cost through higher warehousing costs, added labor, or paused production. And many SMB organizations do not have the ready cash flow and reserved resources to recover from excess inventory nor the resources to expedite when faced with shortages. In addition, the skillsets deployed within SMBs may also be of concern as these functions may often be done using staff that “wear many hats” and perform several functions.
In seeking to answer the challenges of modern inventory management within a global supply chain, companies should assess their methodology. If the optimal frequency for ordering materials is determined using a combination of disparate spreadsheets and a collection of “tribal knowledge”, it is possible that the company will not be able to handle the complexity of raw materials management. Likewise, if the calculation of safety and buffer stock levels is inconsistent and not formalized or data-driven, then chances are there will be shortages. And finally, if the calculations used to generate the materials plan and procure materials isn’t really a “calculation” at all, but instead consists of multiple, incomplete, and overlapping spreadsheets, then there will be gaps in the inventory in various degrees. Fortunately, with the increased complexity of the modern supply chain, data management software has come of age to help formalize and manage raw materials inventory and to optimize inventory control and eliminate these gaps.
Software for effective data management of raw materials inventory should have several key features:
With the challenges faced by small and medium companies as globally sourced supply chains continue to become more complex, data-driven, analytically capable software, such as DemandCaster, is the best option for managing raw materials inventory without losing track.