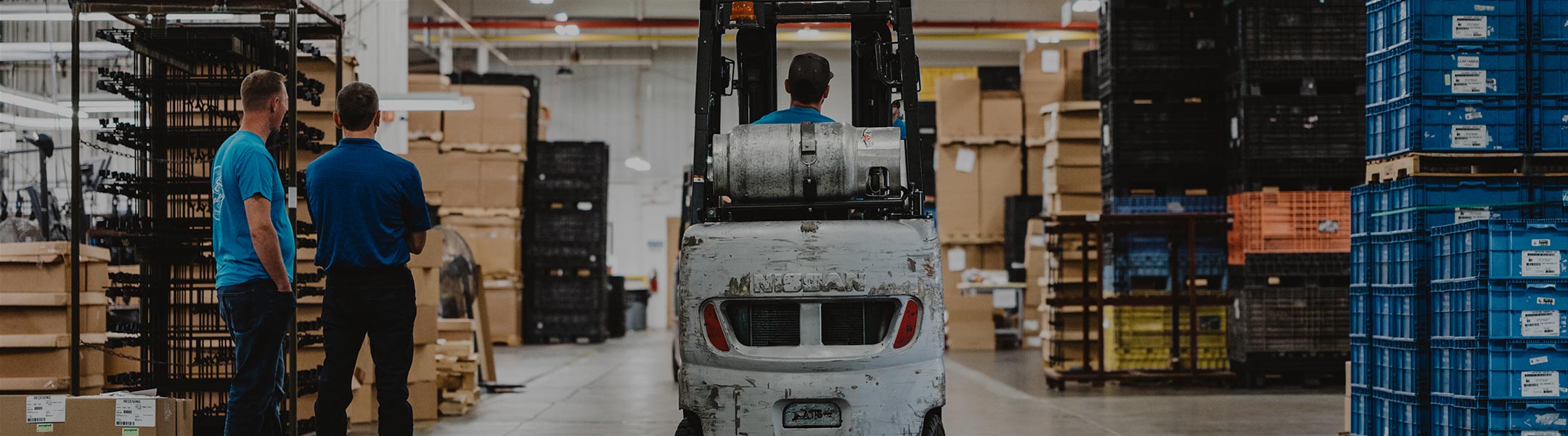
Get your copy of the 7th Annual State of Smart Manufacturing and hear from 300+ manufacturers in this new survey report!
For a monthly digest of expert insights, data points, and tips like the ones in this article.
While there are countless factors that impact your operations, one of the most critical is time. There are only so many hours in the day – time ultimately limits what your operations achieve from quarter to quarter and year over year.
Overall equipment effectiveness (OEE) is the key metric that measures the efficiency of your manufacturing process. Here’s what you should know about factors that might be dragging down your OEE and what you can do to take action.
To improve your OEE, first you must understand what it is and which factors impact it most. OEE measures three critical components of any manufacturing operations:
Each of these factors contributes to your OEE and your overall productivity. Before anything else, you need to have the tools to measure and monitor these metrics – creating baselines and continuously evaluating performance against them.
One of the biggest challenges you’ll face is pinpointing exactly where your losses are coming from among these key metrics. An effective manufacturing execution system (MES) can provide the analytics to trace these losses and the insights you need for corrective action.
Downtime is a clear threat to your OEE. Every time production halts, your operations incur overhead expenses without creating any value. Not only that, but downtime tends to cascade from process to process, impacting OEE at every step of production, both downstream and upstream.
In the worst-case scenario, downtime results in missed production targets and delayed delivery to customers. You can face direct losses due to contract terms and eventually lose customers altogether, so your organization’s reputation is also on the line.
Luckily, there are some straightforward steps you can take to reduce downtime and improve quality improvement – especially when you have the right tools for the job. Automation addresses critical challenges across multiple areas of your operations to tackle OEE as a whole.
First, automated data capture is an absolute must in modern manufacturing. In order to react quickly, your team needs access to real-time plant floor insights. Automated capture also minimizes the risk of human error and lets your team focus on more valuable tasks.
Automation plays a key role during every step of production, including setup. MES Automation and Orchestration with Plex provides the direct machine connectivity necessary to both collect data and control complex processes. By driving setup digitally, your team ensures the right temperature, speed, pressure, and other parameters are set for the job at hand.
Plex Manufacturing Execution System (MES) not only provides your team with the best tools to react to changing situations on the plant floor, it also enables a proactive approach. Proactive operational control lets your team truly maximize OEE throughout every stage of production.
Comprehensive dashboards provide real-time visibility into OEE and other key metrics. Your team can monitor every aspect of production with a bird’s-eye view and the capability to zoom in on finer details as needed for planning, adjustments, maintenance, and optimization. From there, they can make informed decisions and take the most effective action to boost performance.
Making the most of your available time and resources requires choosing the right tools for the job, and the Plex Smart Manufacturing Platform is the perfect solution – bringing together your MES, ERP, and other systems to give your team the best possible foundation to tackle OEE.
Of course, you really need to know you’re making the right choice when choosing the software that will drive your OEE. Download our free Smart Manufacturing Buyer’s Guide today to find the best solution for your operations.