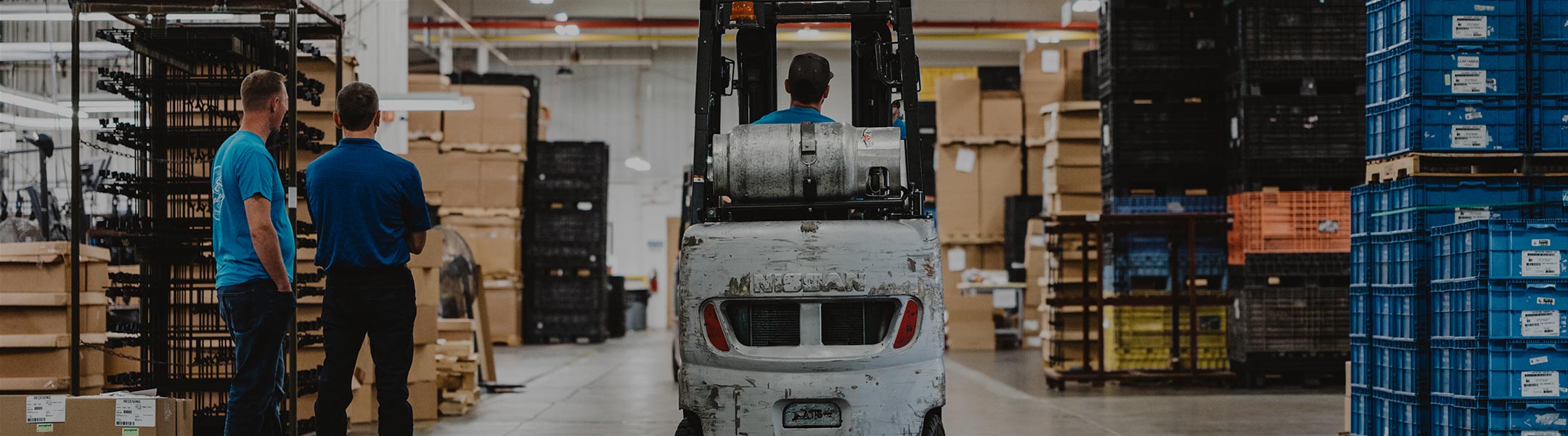
Get your copy of the 7th Annual State of Smart Manufacturing and hear from 300+ manufacturers in this new survey report!
For a monthly digest of expert insights, data points, and tips like the ones in this article.
Not all manufacturing is the same. Some finished goods take only a few steps and a little sub-processing before they’re ready for shipment. Others may require precision cuts and tight tolerances that bring them within requirements for more precise monitoring and equipment. And yet others are deeply derivative with multiple sub-processes, subtractive or additive processes, and complex assembly.
There’s also differentiation in bulk goods, like flour, which may be less complex than a single unit with multiple assemblies and electronic connections like consumer appliances. And finally, there are manufacturing complexity levels that result from regulations and expiry concerns. It’s enough to make anyone’s head spin.
As complexity rises, so does the risk in all the cases above. A plastic coat hanger won’t require the same regulation as a machined part for the aviation industry. Nor are shoes regulated with the same safety requirements as pharmaceuticals.
Not only does risk rise with complexity, but it’s often the case that it grows exponentially. One example would be that of a product like insulin. It requires exacting standards of process and cleanliness, and its risk of spoilage requires controlled environments. After production, it must be refrigerated and used before its viability date has passed.
Consideration for each level of complexity must be factored into the manufacturing process. But the mitigation for the risks they cause - individually and as they overlap - must be part of that process too. This changing level of risk requires continuous updates to technology and equipment, as well as meticulous and often manual tracking.
Many companies are overwhelmed by the paperwork traditionally required for these complex products and their associated risks. Mistakes are made, and it’s difficult for manufacturers without the administrative infrastructure needed to support risk mitigation to expand or break into new markets.
One focus of regulatory bodies and governments in recent years has been traceability and the chain of ownership of materials. Each year brings tighter requirements and tolerances, and traditional traceability is time-lagged and error-prone due to manual data management.
In addition to product risks, manufacturers must manage risks from vendors in terms of product quality, delivery, and missed deadlines. As the pandemic laid bare, supply chain reliability suffered; many industries were forced to utilize substitute products for critical applications, increasing the risk for the well-finished manufacturer.
Because complexity increases risk, the two are intricately linked within manufacturing. But that linkage means they can both be addressed with the same solution.
With an IIoT-enabled smart manufacturing platform, companies are better equipped to manage risk and complexity digitally through:
Regardless of your company’s level of complexity and risk, a solution like the Plex Smart Manufacturing Platform will help you build complexity into optimized processes and manage risk while taking advantage of all the above benefits.
Contact us today to learn how Plex can make your operations feel simpler, safer, and more successful than ever.