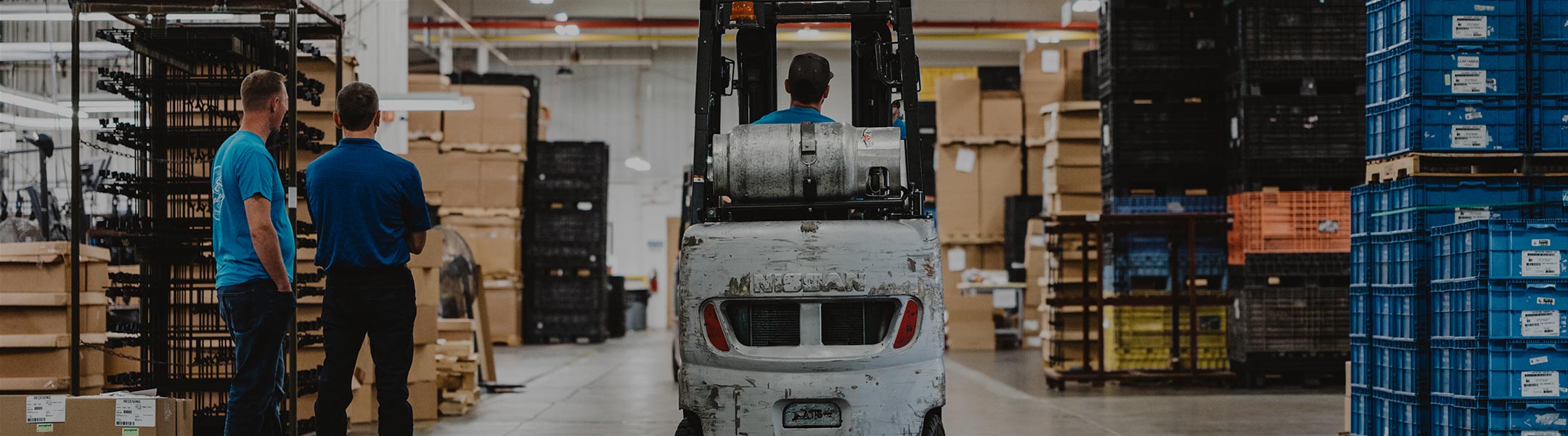
Get your copy of the 7th Annual State of Smart Manufacturing and hear from 300+ manufacturers in this new survey report!
For a monthly digest of expert insights, data points, and tips like the ones in this article.
Management thinker Peter Drucker is often quoted as saying that “you can't manage what you can't measure.”
In a manufacturing environment, this sage management advise can quickly feel impossible to achieve. The effort to measure every relevant data point manually can become overwhelming, so most manufacturers prioritize what to measure at all, and then determine what amount of risk they’re willing to take on accordingly – whether it’s risk of not being able to meet customer demands, or the risk of too many carrying costs.
Just consider inventory management and the concept of safety stock. Manufacturers add additional quantity to buffer against the unknown and the uncontrollable. Yet according to analyst David Turbide, optimizing safety stock should be about more than getting that equation right.
It’s actually about consistent data accuracy and relationships, he says. Manufacturers can lower the risk of not being able to fill orders or the risk of tying up cash in excess inventory by tightening inventory control and recording accuracy, as well as working with suppliers to improve reliability and quality, can help companies reach the ideal risk-reward breakpoint.
Of course, capturing accurate data can be challenging for operators and plant managers that must rely on paper-based manual processes, taking up a ton of valuable time. Thankfully, as manufacturing software tools have matured, manufacturers are gaining access to technologies that can automate the work, allowing leaders to make better business decisions and control the business through greater visibility.
Consider the experiences of A&K Finishing, a plastic paint solution provider that works with automotive companies like General Motors, Ford, BMW, and Toyota.
As the company grew, it knew it need to find a way to capture its inventory data more efficiently and effectively, both to free up time consumed by physical inventory counts, and the ability for the company to focus on what makes a difference for its customers: quality.
By digitizing inventory management, A&K Finishing was able to reach greater inventory accuracy which far exceeded their physical inventory counts. They went from being thousands of dollars off expectations per month when measuring inventory to just a $900 discrepancy within 10 months of their digital transformation – and that was due to a faulty BOM calculation entered into the system, which was immediately corrected.
A&K’s leaders found that their own time entering v. analyzing data shifted quickly. Scott Hankamp, the company’s operations manager, used to spend 85% of his time on data entry alone. Now, he doesn’t do any data entry. Instead, he now spends 30% of his time reviewing data to drive continuous improvement.
Manufacturers: It’s always a worthy effort to make sure your company’s cash is staying where it needs to.
You can’t manage what you can’t measure. End-to-end visibility in a manufacturing environment means recording every receipt, move, production, and shipping steps. When choosing a system to help automate your processes, make sure that you choose a system that can track inventory through work-in-progress steps. This type of visibility makes the black box of production more transparent – a rare offering among systems today.
Learn more about how manufacturers like you leverage manufacturing execution solutions to achieve greater visibility and control on the shop floor by downloading our white paper on achieving manufacturing agility through MES Excellence.