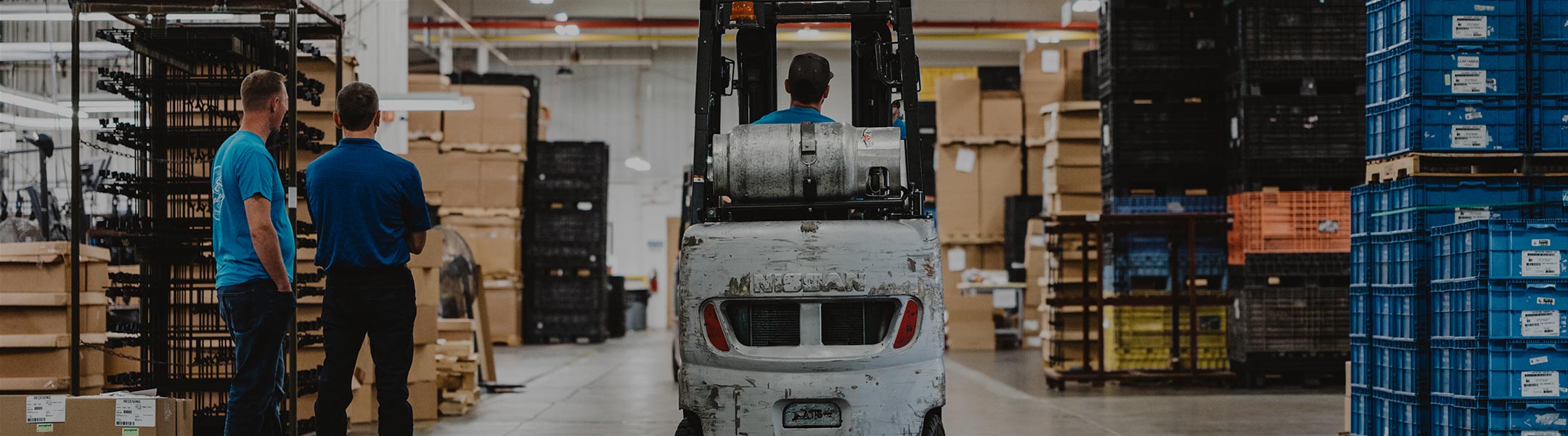
Get your copy of the 7th Annual State of Smart Manufacturing and hear from 300+ manufacturers in this new survey report!
For a monthly digest of expert insights, data points, and tips like the ones in this article.
For years, many companies relied upon Sales and Operations Planning (S&OP) to align processes in their supply chain. By doing so, companies were able to improve performance and profitability. As the value perception of S&OP matured it became apparent that it could become a more effective tool by extending the benefits of S&OP throughout the entire supply chain.
Integrated Business Planning (IBP) has evolved the concepts learned in S&OP to include more of an end-to-end supply chain picture. This means products, demand planning, and strategic planning can work to align company plans regularly. This allows managers and executives to better allocate resources and respond nimbly to changes in the market.
Every company works to grow. And for Small and Medium-Sized Businesses (SMBs), growth tends to be incremental. In these companies, business planning may consist of disparate systems and the ubiquitous “planning by spreadsheet”. In fact, Gartner has found that 50-60% of all companies still use Excel for some form of planning. As they grow, SMBs may begin to exhibit “Complexity Characteristics”. This includes things such as scale, higher variability, more complex organizational structures, and the effects of globalization on the supply chain. Systems without data interoperability and with manual planning systems become much less effective.
Integrated Business Planning (IBP) is a process for bringing the fragmented elements of an enterprise together. It aligns business strategy, finances, operations, and planning. A successful IBP framework consists of seven steps critical to aligning company plans. These steps aim to: decipher the data, develop a demand plan, drive a supply plan, delineate constraints, deliver consensus, deliberately execute, and do it again. Companies that leverage technology to oversee a framework for IBP establish routines and automate business processes under one umbrella.
Demand planning is a key part of the IBP review cycle. The demand review looks at customer demand forecasts over the coming 2-year period. It also looks at performance to forecast for the period as well. Without solid demand planning, IBP does not work.
With IBP’s holistic view of business performance, complexity characteristics will quickly outstrip the ability of a company to use spreadsheets for accurate demand planning. Too much is at stake for errors to be introduced through a manual process. If demand forecasts are not reliable, the rest of the plans for the company will be thrown off. And because integrating all business processes through technology is critical for IBP to succeed, the use of demand planning software is critical as well.
Demand planning is “forward-looking”, using data to drive forecasts and plan the supply chain, operations, sales, and marketing. Demand planning software gives companies implementing IBP a distinct advantage. Benefits of accurate forecasts include:
In traditional demand planning, data was not real-time, creating a lag between demand signal and the commencement of production. This meant that data was outdated by the time those production plans were put into effect, reducing forecast accuracy. Also, data was traditionally siloed across organizations, causing breakdowns or gaps in communication. Collaboration and consensus on a plan were possible only after data from various fragmented internal systems were reconciled.
The result was a cycle of stops and starts that further impacted the accuracy of demand planning. Because today’s markets are demand-focused, it is important to have forecasts reflect the reality of today and the future.
Today’s demand planning software enables companies to work with very large data sets over short, medium, and long-term timeframes. This software uses highly advanced algorithms to provide predictable analytics spreadsheets cannot. Benefits of agile demand planning software that compliments IBP include:
DemandCaster provides robust demand and supply planning software that works alongside IBP deployments and delivers reliable Demand Review cycles for execs and managers. Click below to learn more on how to speed your business growth with a connected supply chain.