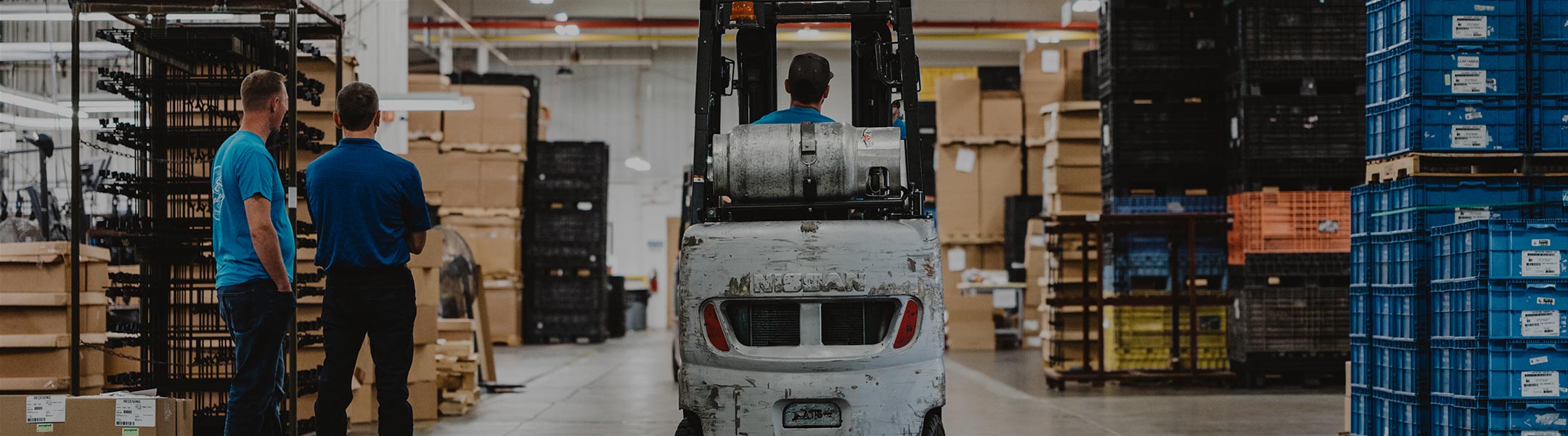
Get your copy of the 7th Annual State of Smart Manufacturing and hear from 300+ manufacturers in this new survey report!
For a monthly digest of expert insights, data points, and tips like the ones in this article.
The complex global supplier network, dynamic customer demands, and the need for short and effective NPI cycles provide little room for error in the electronics industry, especially when it comes to managing the quality of processes and products. A slight hiccup somewhere along the value chain could have significant effects on the bottom line down the road. What electronics manufacturers need is a holistic business measurement to provide visibility into the effectiveness of quality management as it relates to both cost and operating margins. Many are realizing improvements in these areas by measuring the cost of quality metric.
Depending on whom you’re talking to or which company is measuring it, the cost of quality metric may be defined in many different ways. To simplify things, we’ll cover its main elements. At a high level, it can be defined as a function of the cost of good quality and the cost of poor quality.
In this equation, the cost of good quality is a measurement of costs companies incur to ensure the production and delivery of quality products. On the other end, the cost of poor quality relates to costs incurred to evaluate and prevent quality issues. Variables that affect these two areas are below:
The formula above is only the tip of the iceberg when it comes to the cost of quality. There are many more factors to consider. Depending on how granular you want to get, the formula can provide incredible insight into your operation. By measuring each variable as a percentage of revenue, the metric can shed light on the areas that will have the most direct and impactful results on profitability.
To learn more about how electronics manufacturers can evaluate their cost of quality and improve profitability, click here to watch an on-demand webinar with LNS Research on this topic.