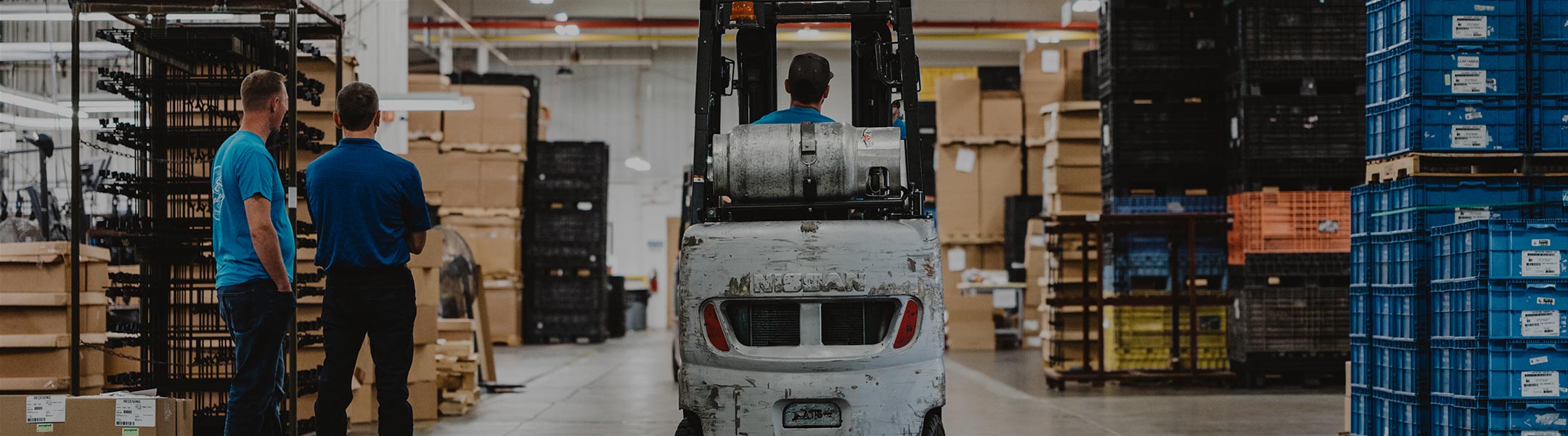
Get your copy of the 7th Annual State of Smart Manufacturing and hear from 300+ manufacturers in this new survey report!
For a monthly digest of expert insights, data points, and tips like the ones in this article.
For many companies, inventory management is where all the elements of the supply chain converge.
Inventory may be seen as the bloodstream of any competitive business. Its unobstructed flow is critical to the well being of any organization that trades in tangible goods. Like the life-sustaining “oxygen” that is carried by the blood to various parts of the human body, inventory carries value for manufacturing, marketing, and sales. Like the doctor who extracts a few samples of blood from a patient’s arm in order to evaluate health and wellness indicators, a view of inventory can say a lot about a business. Accumulation of unnecessary inventory is frequently symptomatic of bigger problems that lurk somewhere in a company’s systems infrastructure and processes. Its significance cannot be overstated.
The forces of technology, globalization, and consumer empowerment have profoundly influenced the way that industries have managed inventory in the past thirty years or more.
Tools that range from the ubiquitous but powerful Excel spreadsheet to Warehouse Management Systems (WMS) to Demand Planning and Forecasting Systems to multifunctional and integrative Enterprise Resource Planning (ERP) Systems have helped us to make inventory-related computations at exceedingly high speeds, and have improved inventory record accuracy substantially.
Globalization has challenged businesses to reposition inventory within its supply chain to take advantage of production economies in remote locations and drive reductions in Cost of Goods Sold. Many organizations have pursued a horizontally integrated supply chain (as opposed to the traditionally vertically-oriented supply chain) as they search for economies of production and delivery.
Consumer empowerment has led supply chains to become more responsive, agile, and quality-focused, as companies direct more attention to the demand side of their businesses.
However, studies seem to indicate that improvement in inventory performance has been uneven across American industries. In a recent analysis, Lora Cecere (SupplyChainShaman.com) found that in eight out of twelve US industries studied, days of supply of inventory actually increased when one compares the 2004-2006 time period to 2010-2016. This, in spite of the technological advances that we have enjoyed.
What, then, does the near future hold for companies who are able to successfully manage inventory? Here are five predictions:
The year 2018 places us in the midst of the Fourth Industrial Revolution. Additive manufacturing (“3D Printing”), Artificial Intelligence (AI), robotics, and Blockchain are all establishing themselves, individually and collectively, as significant disruptors.
As 3D Printing evolves and matures, manufacturing of parts and components will move closer to the point of engineering and new product development. Prototypes and even finished goods will be printed right next door. This will remove the need to build and accumulate inventory in remote, overseas locations, first on a small scale but in the near term, this trend will become economically significant. It will add an entirely new dimension to businesses who seek to become agile and flexible.
AI will assist businesses in making decisions, especially routine ones, with greater accuracy and with higher levels of sophistication. Computers will learn from experience and will respond to changes with greater levels of quality and certainty. Humans will rely increasingly on AI to make profitable business decisions that balance cost with customer service.
Robotics are well-established and will continue to influence industry as they are used to manufacture products with less need for manual labor, reduced manufacturing cycle time, and improved health and safety performance. Humans will continue to be relieved of dangerous and monotonous work, necessitating the need for education and training that is targeted at higher levels of business acumen.
Blockchain will revolutionize the way that financial transactions are conducted internationally, and the manner in which chain-of-custody documentation will pass through the extended enterprise. This will improve the speed, quality, and security of information.
Legend has it that Tim Cook of Apple once exclaimed: “Inventory is fundamentally evil!” The Toyota Production System (TPS), and Lean Thinking sees inventory as “muda” (waste). The message is clear, but it is also an exaggeration for effect. Insightful companies will see that too much inventory is waste, but that inventory, deployed in the right quantities at the right time in the right places, can provide substantial benefit to businesses and enhance competitive advantage.
The supply chain concept has been encouraging practitioners for decades to knock down the walls of communication and destroy functional silos that interfere with collaboration. Visionary companies will see that there is a lot more work to do to fully embrace this ethic.
It is only by taking a system-wide view of inventory investment that practitioners can hope to optimize its deployment. At each stage of production, from raw materials to finished consumer goods, and at all transportation activities in between, the economies and trade-offs need to be analyzed. After analysis, the results need to be synthesized and impacts of various solutions assessed from the perspective of benefit to the entire supply chain.
Such holistic analysis requires effective and efficient communication, and cross-functional understanding. This can be enabled by education and training, along with levering technology.
Since the 1990’s, the trend for American, Canadian, and Western European industry has been to locate manufacturing offshore, often through outsourcing. This trend was initiated by the search for low-cost production, and lower “ex-factory” pricing that would translate into lower cost of goods sold. For a while, this strategy was broadly successful, and East Asia became the Factory to the World.
Through the Re-Shoring Initiative, for example, Harry Moser has encouraged American companies to review decisions made regarding offshoring of production to account for changes in the relative cost structures that have emerged over the past twenty years. He argues that many companies failed to account for the Total Cost of Ownership (TCO) when decisions to offshore production were made. Supply chain risk profiles were not fully understood, nor were the effects of longer supply pipelines. Engineering changes became more difficult to execute. A rising middle class in China has increased the labor cost of manufacturing in that country, to the point where it may be argued that total costs of production in Asia are now roughly equivalent to those available by producing closer to home.
Through TCO analysis, and by responding to the “source locally” initiatives, more businesses will repatriate manufacturing closer to home. In turn, this will have a profound impact on inventory investment strategies.
Globalization is with us forever. International trade will continue to benefit human welfare. But the dynamics will undoubtedly change.
As businesses pursued a more horizontally integrated business model, outsourcing and offshoring production and distribution, the risk profile of supply chains changed dramatically.
In the post 9/11 era, intense focus has been brought to bear on matters of supply chain security. At first, the prime motivator for the development of security programs such as C-TPAT was to protect the USA and its allies from inbound transportation of weapons of mass destruction. These programs have broadened their scope in an attempt to prevent a wide variety of supply chain threats. Security concerns include transportation of contraband materials, smuggling, piracy, organized crime, and counterfeiting.
One of the costs of globalization has been widespread introduction of counterfeit material into valuable supply chains. Pharmaceuticals, food products, aerospace, and fashion industries have been favorite targets of unethical traders in recent years. Validation of the authenticity of components and finished goods is now a special concern of buyers and inventory managers. While work on the Internet of Things (IoT) promises to help develop increased sophistication of product identification through barcoding and similar initiatives, protection of inventory in the short term is an expensive proposition.
In summary, successful companies will embrace the challenges of inventory management in the 21st century by levering the technology that is being offered through the Fourth Industrial Revolution. More important, companies will look at inventory as a strategic asset, that when properly deployed will deliver increased value and competitive advantage. Effective collaboration between supply chain partners will take on increased importance. The intensifying risks inherent with global sourcing in combination with a better appreciation of TCO will motivate companies to rethink their global inventory strategies.