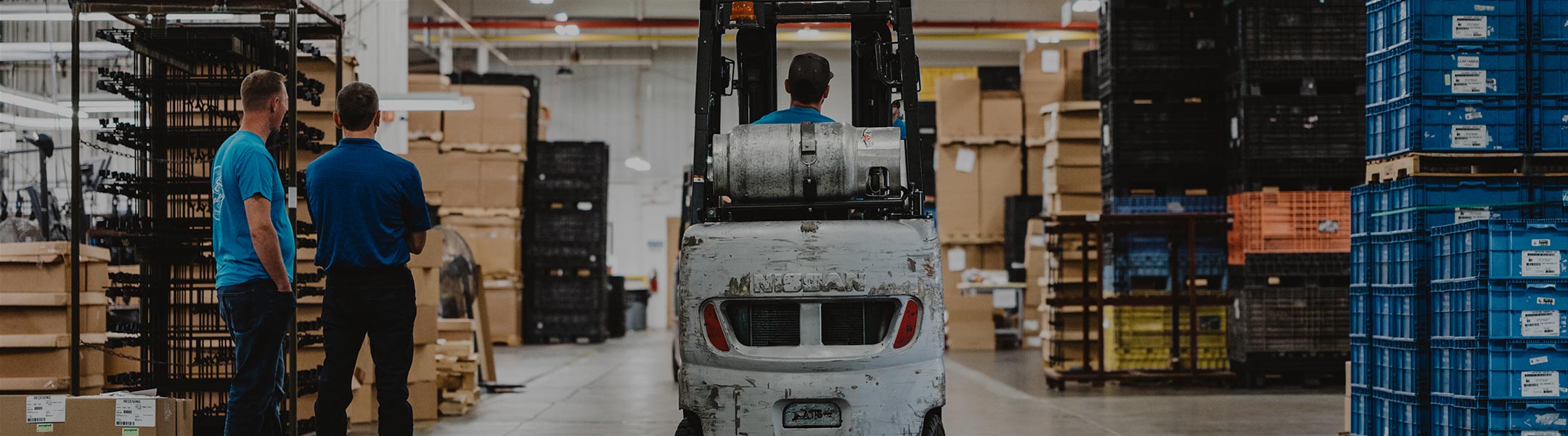
Get your copy of the 7th Annual State of Smart Manufacturing and hear from 300+ manufacturers in this new survey report!
For a monthly digest of expert insights, data points, and tips like the ones in this article.
In the vast expanse of a modern factory floor, the rhythms of production echo beneath the vigilant gaze of towering machinery. Workers and robots perform in a well-choreographed ballet of precision and speed. This industrial symphony is orchestrated by a frequently overlooked catalyst of contemporary innovation – edge computing.
Edge computing is a vital part of the Industrial Internet of Things (IIoT). While it may not get as much attention as robots or smart sensors, its role in enabling near-instant data processing on the factory floor is indispensable. This localized computing is both an innovator’s tool and a practical necessity in manufacturing.
Unlike cloud computing, which processes data in a centralized warehouse, edge computing processes data locally. In manufacturing, this means data from coils, furnaces, and packaging machines – even the entire product lifecycle – is processed on-site. This minimizes latency, enabling time-critical decisions and real-time operational insights.
Imagine a food processing facility where even a minor fluctuation in refrigerator temperature can spoil massive quantities of perishable items. In such a high-stakes environment, even a momentary delay in temperature correction could lead to significant losses. However, with edge computing, temperature sensors immediately relay critical data to a nearby device that analyzes and adjusts the temperature instantly, ensuring seamless operations.
Edge computing extends far beyond this example, permeating various facets of modern manufacturing. Consider a bustling automotive assembly line, where edge devices predict equipment failures before they occur, allowing for preemptive maintenance that minimizes downtime and maximizes productivity. Or picture a pharmaceutical lab, where edge computing aids in real-time quality assurance during the delicate drug production process, confirming that every batch meets stringent standards.
As the backbone of Industry 4.0, also known as the Fourth Industrial Revolution, edge computing merges physical production with advanced digital technology, forming a highly responsive, adaptable, and intelligent network. This integration revolutionizes industries by enabling them to operate more efficiently and effectively.
The deployment of edge computing in the manufacturing sector is not only reshaping the operational landscape but also driving innovation to new heights.
Operational efficiency is the lifeblood of any manufacturing enterprise. Here, the ability to monitor and control processes in real time can be the difference between a lean, mean production machine and an operation bogged down by inefficiencies. Edge computing offers this advantage, with its capacity to process large volumes of live data, effectively manage resources, and produce actionable reports that aid in streamlining operations.
In large-scale industrial settings, the failure of a single machine can lead to a cascade of disruptions, resulting in substantial downtime and significant financial losses. Edge computing’s predictive maintenance capabilities represent a paradigm shift, as they usher in a proactive approach to asset management. Sensors predict potential component failures by detecting anomalies in performance and temperature, enabling pre-emptive actions that avert costly breakdowns.
In the quest for product perfection, quality control has always been paramount. Edge computing elevates this imperative by providing a granular view of the manufacturing process, capable of identifying and rectifying deviations from the norm. It also ensures traceability, enabling manufacturers to pinpoint the origins of defects and take necessary corrective measures in a targeted, efficient manner.
The synchronization of data across various touchpoints through edge computing aids in inventory and product tracking. By facilitating intelligent logistics and warehousing, manufacturers can reduce stockpiling, manage shelf life, and optimize product movements, ultimately curtailing unnecessary waste.
In today's interconnected world, the supply chain is often as crucial as the production line itself. Edge computing plays a critical role in streamlining these processes by providing real-time data on inventory levels, shipment updates, and potential supply chain disruptions. For example, in the automotive industry, where parts and assemblies come from various suppliers, edge systems can predict and manage supply chain issues before they affect production, ensuring that assembly lines never run dry.
Edge computing is also instrumental in promoting sustainable manufacturing practices. By providing real-time data on energy consumption and machine efficiency, manufacturers can make immediate adjustments to reduce energy usage and decrease carbon footprints. This not only helps companies comply with increasingly stringent environmental regulations but also reduces operational costs.
The deployment of edge computing on the manufacturing floor is more than just an upgrade; it is a revolution that reshapes how industries operate, innovate, and deliver products. Its ability to process and analyze data in real-time at the location of data generation presents a robust solution to many of the challenges faced by manufacturers today. As we continue to explore the capabilities and impacts of edge technologies, it becomes evident that the future of manufacturing will rely heavily on this pivotal technology.
Join us in the next installment of this series, where we will delve deeper into specific case studies and explore how edge computing is not just supporting but revolutionizing various manufacturing sectors.