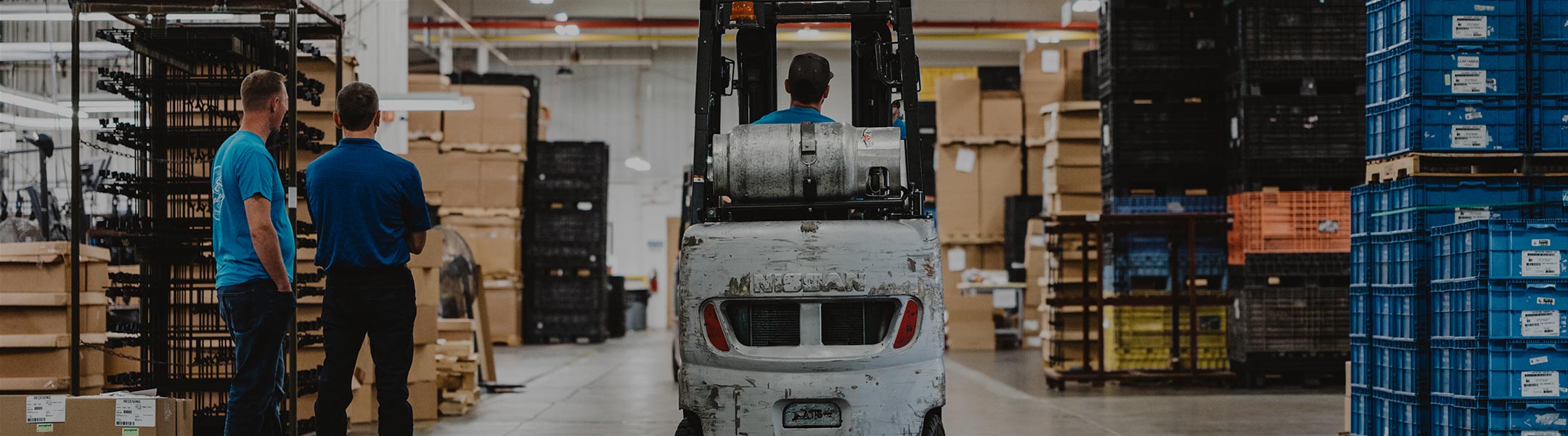
Get your copy of the 7th Annual State of Smart Manufacturing and hear from 300+ manufacturers in this new survey report!
For a monthly digest of expert insights, data points, and tips like the ones in this article.
With disruption such as COVID-19 rapidly shifting consumer tastes, market volatility, and human error, the threat of both overstock and stockouts is always present. On the one hand, companies strive to have enough stock available to manage their order position and fulfill service level agreements. On the other, excess inventory can drive up costs and restrict cash flow. So what part does safety stock or safety time play in this?
One way to ensure order fulfillment is by using safety stock – that extra edge used as a buffer between orders and on-hand inventory that allows a company to achieve high service levels and maintain customer satisfaction. The retention of safety stock is an attempt to capture forecasted demand for a product. However, the caveat is that you understand that demand in the first place.
Safety time is an attempt to leverage lead times to ensure that materials and supplies arrive just in time for the correct production level. It may be based on actual lead time if there are few, or even a single, component and supply is predictable. Or a company may use a more complex analysis that includes considerations such as internal review, supplier lead time, transportation, and other factors.
While each method has distinct advantages and disadvantages, they are often used together. In companies with a sophisticated supply chain management system, the balance between the two can be managed efficiently. But in those whose supply chain management is still plagued by spreadsheets, disparate and siloed internal systems, and “gut feeling”, there is a danger of creating problems in their supply chain.
One such problem can arise when safety time does not capture or recognize rising demand quickly enough. If lead times from suppliers tend to run long, or if the material comes from abroad, seasonal demand or other unforeseen surges in orders can result in shortages by the time the product arrives. If the surge is large enough, safety stock levels may be depleted before arrival. In the above case, failure by the planning system to recognize or capture demand can push it into expediting mode. This impacts profitability in the form of lost sales or cancelled orders as well as adding expensive expediting costs to Cost of Goods Sold (COGS). And if the misstep is big enough, or continues to happen, it can throw the entire planning system into a spiral.
Of course, the opposite scenario is a concern as well. By missing demand signals, a company may not detect trending drops in sales due to disruption, changing consumer tastes, or other factors. In these cases, if automatic replenishment quantities – or human analytical shortcomings – continue to kick in, even as demand drops, both safety time and safety stock calculations become moot as the company begins to carry too much inventory.
The tendency of many decision-makers is almost always to err on the side of extra stock “just in case”. But when that instinct is coupled with missed demand signals, a company can find itself overwhelmed with stock. This drives up holding costs and may result in the company having to take on additional warehouse space, adding cost at a time when orders are slowing.
For companies looking to balance safety stock with safety time, there are a few things to consider:
The most effective way to balance safety stock and safety time is with demand and supply software. Using advanced analytics, near real-time data can be combined with historical data to drive optimum economic order quantities and set both stock and lead time targets that align with demand.
oday’s demand and supply automation software also offer tools such as “what if” scenario planning, and ABC analysis to focus stock and inventory levels on the most profitable products. Combined with time-phased inventory forecasting, tasks such as order timing and quantity can be automated with confidence.
If your company is mired down in spreadsheets, manual overrides, and miscommunication between planners and suppliers, Plex DemandCaster offers Supply Chain Planning software that helps you put demand in control of supply. By automating your supply planning with Plex DemandCaster, you can confidently reduce demand uncertainty to find the best balance between safety stock and safety time for your business.