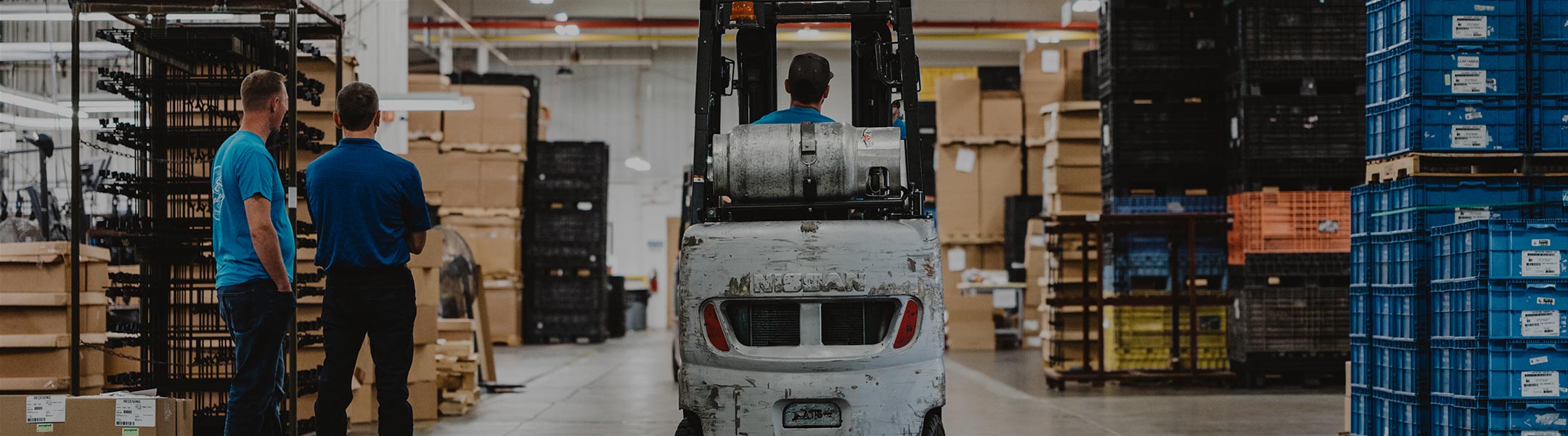
Get your copy of the 7th Annual State of Smart Manufacturing and hear from 300+ manufacturers in this new survey report!
For a monthly digest of expert insights, data points, and tips like the ones in this article.
As the COVID-19 crisis rolled across the globe throughout 2020, many companies found themselves with brittle or unmanageable supply chains that hampered their response. Many were forced to shutter for part or all the pandemic. Others took longer inventory positions early and have been able to mitigate production losses. And some simply ran out of material, forcing the temporary shutdown of popular product lines in many markets.
As the disruptions caused by the pandemic upended many supply chains around the world, planners and managers have been forced to re-evaluate once stable supply chains and craft new approaches to fulfillment. And as in any disruption, inventory has found itself in the spotlight.
One thing that has become clear during this time has been that companies must look at inventory from several angles. They must evaluate not only how much inventory they need, but also the importance of specific inventory items and levels based on the most profitable product lines. Contextualizing inventory goes beyond traditional differences such as process vs discreet industries. Now, inventory must be shaped in context with the markets being served, profit margins and revenue, and several other factors. In short, inventory must be contextualized to allow planners and managers to develop a sound strategy to succeed should disruptions on the scale of COVID occur again.
The days of simple dollar calculations of total inventory valuation over broad ranges as the only number that matters may be over. And to develop a broader strategy for inventory going forward, there are several key performance indicators that must be considered together to put inventory in context:
To navigate today’s disruptions, inventory needs to be considered using several filters and multiple KPIs. And human efforts alone, regardless of the number of spreadsheets and formulas, can’t keep these numbers accurate in order to develop the best strategy for an optimized inventory.
Fortunately, planning software can help when contextualizing inventory, analyzing data and providing insights into inventory levels to succeed during times of disruption. With advanced analytics, sophisticated “what-if” scenarios, ABC analysis, and other tools, inventory planning and optimization software from Plex DemandCaster can help anticipate the unexpected and develop an inventory strategy that works along with multiple parameters.