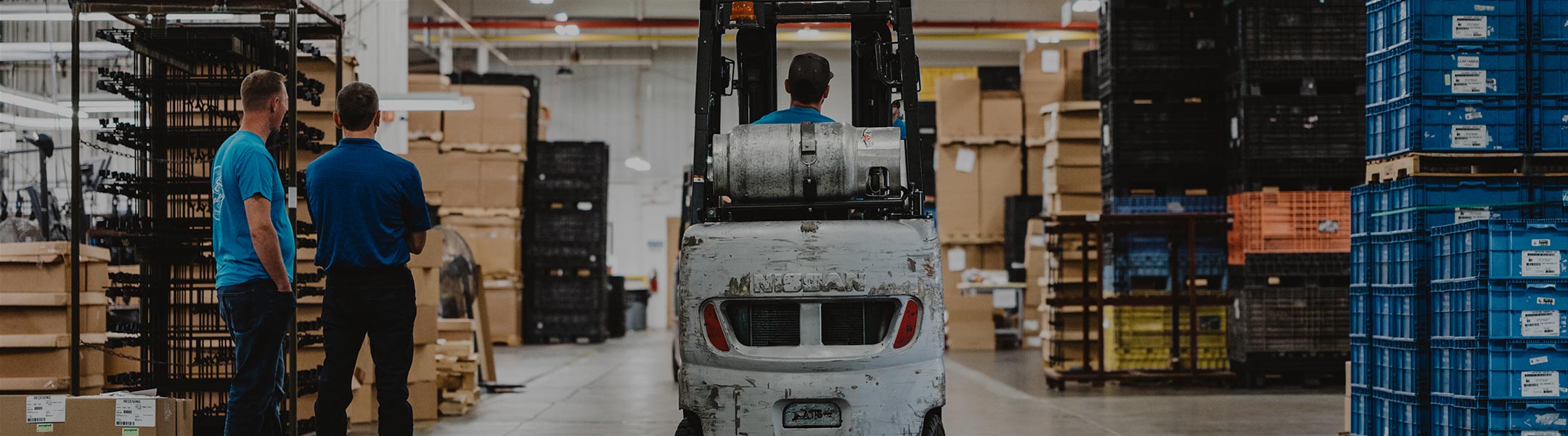
Get your copy of the 7th Annual State of Smart Manufacturing and hear from 300+ manufacturers in this new survey report!
For a monthly digest of expert insights, data points, and tips like the ones in this article.
Everyone has experienced the disappointment of opening a bag of chips or crackers and looking inside only to see half-empty space. Often, the product contains the cryptic warning "Caution: Contents May Have Settled."
Visually, this isn't very pleasant, but everyone knows the content volume is the same. It's just the space between the products affected by the journey from factory to retail shelf. But for food and beverage manufacturers relying on outdated processes, this “settling” has become a metaphor for their operations.
Like the space at the top of the bag, manual data analysis forces manufacturers to settle on low standards for quality in manufacturing. Because it is error-prone and biased, you continuously need to determine if you’re getting what you need and expect.
Manual processes are also time-lagged. When the data is collected, rationalized, analyzed by a person or team, and pushed to its destination, critical events that impact quality may have already occurred or be missed altogether. Then, there are the limits of human analysis. Even if the data is good, humans can only do so much with their thoughts or with spreadsheets.
Manufacturers are left peering inside their data, knowing it could be "more" yet having to settle for the best they can do. Unfortunately, this is more than just an inefficiency or inconvenience. At a time when the FDA is planning new requirements for food labels along with the impacts of the Food Safety Modernization Act, settling for poor quality means settling for compliance issues and increased legal risk.
In an era where stricter regulation and tighter transparency are mandated, food and beverage manufacturers must prioritize quality. Some realize that while their products may settle inside the packaging, their quality can't.
According to the State of Smart Manufacturing Report, improving quality is the #1 catalyst for digital transformation in consumer packaged goods manufacturers, with a quality management system (QMS) topping the list of smart manufacturing technologies being adopted.
Clearly, technology is how food and beverage companies freshen their quality to ensure that their metaphorical "bag" is complete and capable of handling traditional challenges and those that continue to arise in a stricter market. Thankfully, several critical steps will help guide those looking to work toward smarter manufacturing:
Conduct a Self-Assessment – Every company is different, so identify your IT and OT capabilities and define what metrics and KPIs you need to measure when adopting a smart manufacturing solution.
Identify an Advanced Solution – Manufacturing companies are notorious for having legacy software that doesn't help improve quality or, in some cases, suffers from interoperability issues to the point that it makes quality worse.
Develop a Sound Deployment Strategy – While the power of real-time data and analytics is enormous, it requires buy-in so everyone is on the same page. This includes piloting, testing, training, and commitment.
Track and Deploy Continuous Improvement – Smart manufacturing solutions will drive real-time data and analysis to highlight areas for continuous improvement. Review the results against the metrics and KPIs set as a goal. Along the way, new actionable insights will be revealed with the power of visibility and real-time analysis.
Smart manufacturing offers the capability to respond using real-time, actionable data. It unlocks unprecedented gains in efficiency, process optimization, and performance. These gains can be directly translated into superior quality that impacts growth and helps companies address challenges.
For example, the Plex Smart Manufacturing Platform™ lets you freshen your technology and improve quality. Because you can track and trace your products accurately, you can respond quickly. This digital approach enables you to identify process improvements immediately before problems arise. You can leverage full visibility and real-time data to overcome the limitations of manual systems, so your quality bag is full each time you open it.
Get more food and beverage insights related to quality by reviewing the State of Smart Manufacturing: Consumer Packaged Goods report.