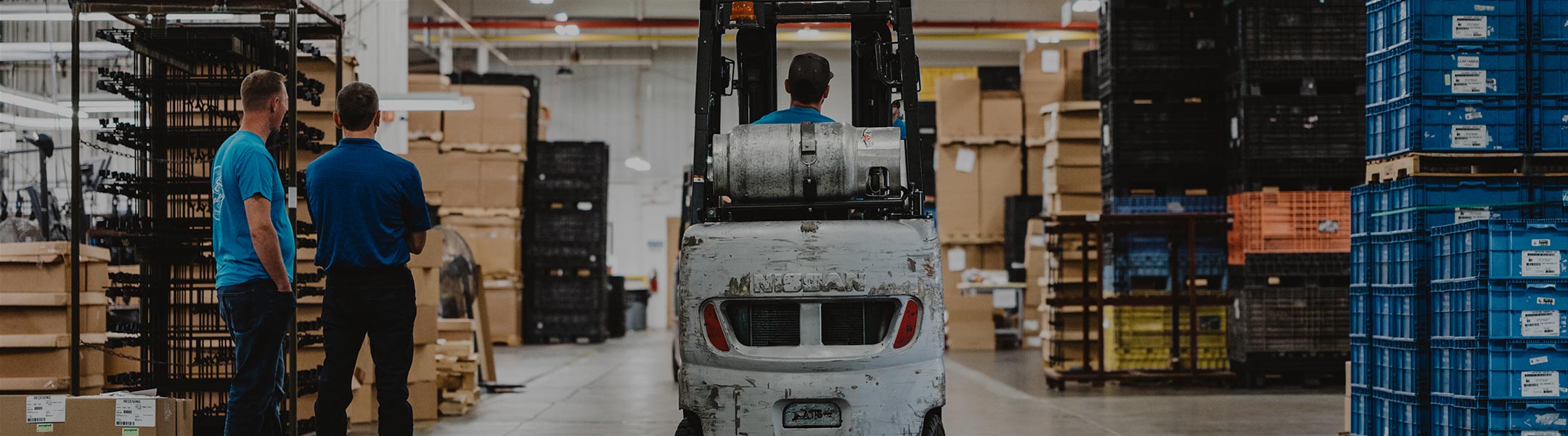
Get your copy of the 7th Annual State of Smart Manufacturing and hear from 300+ manufacturers in this new survey report!
For a monthly digest of expert insights, data points, and tips like the ones in this article.
Production scheduling is an essential component in any manufacturing operation. It synchronizes operations so everyone is on the same page and uses the same game plan.
As the plan is executed, production team members work off a dispatch list, which holds the essential information used to bring the schedule to life and translate the production plan into execution. How production scheduling is managed varies significantly across industries. Many organizations still use manual systems or Excel spreadsheets, while others utilize various software like ERP or MES systems.
Given the wide range of manual, semi-automated, and automated production processes, traditional production scheduling tools have many limitations, including:
Once the production plan is created, many planning systems look at rough cut capacity to determine machine time, labor, and other elements. However, this, too, is a limiting factor because planners may find that the machine capacity of specific functions for multiple orders is not feasible within the allotted timeframe.
These limitations often hinder the production of a realistic production schedule. One way to overcome this is to couple the production plan with a concise and detailed schedule of a company’s finite resources.
Finite capacity scheduling addresses many of the limitations noted above. It’s a process that schedules the work needed to fulfill orders within their timeframe while properly allocating the resources necessary to complete the job.
Finite capacity scheduling takes the constraints of the operation into account. These include labor, staging, raw materials storage, tooling overlap, etc. By optimizing these variables within the production plan, a schedule can be created that increases output, reduces waste and waiting time, and drives higher operational efficiency.
The production plan defines the “what” of demand. It accounts for what orders are incoming, the materials needed, and other resources required. Planning uses a long-term horizon and sets orders' quantity and due dates. It also generates a rough-cut analysis of work center capacity.
Finite capacity scheduling works on a short-term horizon, such as a week or month. Its goal is to optimize production flow using synchronized dispatch lists that work within the constraints of material, capacity, and resources.
A finite capacity schedule has many benefits over traditional scheduling, including:
With manual or semi-automated planning systems, schedules can become complicated quickly. In an attempt to plan the correct sequence for the schedule, combinations of material requirements, blends, tooling, and other factors rapidly scale to an untenable level, creating schedules that are not feasible, hard to stick to, and do not take all constraints into account.
Standalone software systems improved these problems, but they needed to be more robust algorithmically and created a ceiling on improvement. A finite capacity schedule is essential to fully address complex manufacturing challenges.
Rockwell Automation has taken the reality of finite capacity scheduling as part of a suite of smart manufacturing solutions with its Finite Scheduler Application for discrete manufacturers. The tool is an API application that works with any existing standalone system.
Data quality is key to tackling scheduling feasibility and stability issues. Many companies struggle to access and collect basic information such as process time, accurate changeover times, etc.
The Finite Scheduler takes a different approach to overcoming these obstacles. As an ERP/MRP agnostic adaptive production scheduler, it will use machine integration and machine learning to develop optimized processes and setup times. This data can then generate increasingly more accurate schedules as data quality improves. The adaptive scheduler will also be able to utilize data from events on the plant floor to change the schedule using prescriptive algorithms.
Upcoming versions will have an interactive dashboard that shows resources, orders, and schedule components. Users can see different views, setup times, tooling, material, and more.
The rollout of the Finite Scheduler is part of an overall strategy of combining solutions across digital transformations. It can work with any ERP or standalone software via API, and can be effectively used with Plex supply chain planning software. It can even be integrated with high-speed and highly sophisticated robotics on the plant floor.
As this combination of solutions matures, the Finite Scheduler will be the glue that allows for schedule attainment and feasibility that was not possible before.
Watch this webinar to learn more about the Finite Scheduler's potential in your operations and how it can fit into your overall digital strategy.