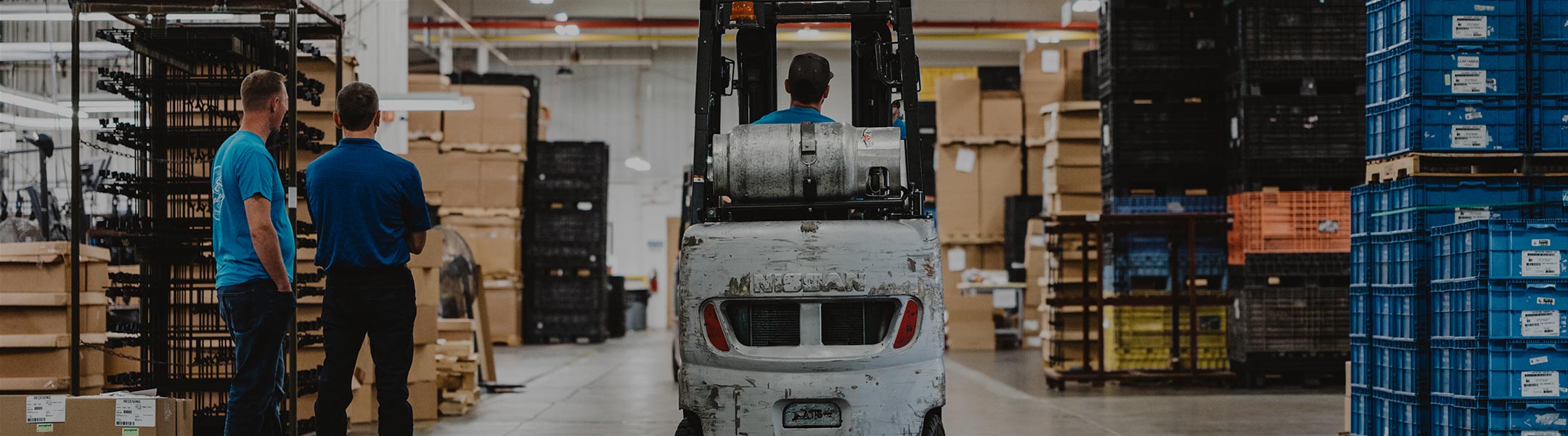
Get your copy of the 7th Annual State of Smart Manufacturing and hear from 300+ manufacturers in this new survey report!
For a monthly digest of expert insights, data points, and tips like the ones in this article.
With the world having been plunged into uncertainty during the COVID-19 pandemic, a critical issue for business managers is stabilizing their supply chain to a consistent flow of components and materials. One July report by the Institute for Supply Management indicates that as many as 97% of companies have been impacted by COVID-19. And while production levels in many sectors have returned to near pre-COVID levels, there is still cause to be wary should a second wave become a reality.
Already, National Association of Manufacturer’s data shows that respondents anticipate a 4.3% decline in sales in the coming 12 months and a 3.8% fall in production over the same forecast period. But with the crisis drawing out over a longer period, what can companies do to manage supply chain planning in a time of global discord?
During the 2008 recession, companies used a variety of tactics to survive and pull through the difficult years that followed. For many, this included traditional steps such as layoffs, reductions in product lines or service levels and other remedial methods to cut losses. However, others used the time to transform their business and improve their operations. This resulted in a 5% increase in EBIDTA for those that took that route, compared to companies enacting more conventional control measures.
As these uncertain times continue, in order to improve-and in many cases survive- companies have an opportunity to deploy new software platforms and analytics to leverage Sales and Operations Planning (S&OP). This “invest-to-survive” strategy strongly impacts supply chain planning where new, data-driven digitization will enable leaders to manage supply chain constraints by better understanding demand and supply at both a granular and meta level.
Planning software also enables better collaboration across the supply chain. The explanation for this is that silos are broken down so stakeholders across an organization have access to critical data. This gives them time to respond with a combination of automated actions or more appropriate decision-making since the data and analysis is provided in real-time.
For those companies willing to digitally transform, these new technologies can be used to navigate the current reality and weather the storm of COVID-19. The use of digital technology can not only help to stabilize supply chains—it can even be leveraged to thrive and succeed as these platforms improve efficiency and agility.
Here are 5 keys to managing supply chains with advanced planning software for these uncertain times:
Even before COVID-19, supply chain complexity had been an increasingly “hot” issue. Add to the picture new tariff restrictions, regional conflicts and geopolitical events/disruptions, and you’ll know that securing access to materials and critical resources is not without difficulty. However, by optimizing S&OP process, digitizing planning efforts and strengthening partnerships across the supply chain, companies can develop new and successful strategies to forge ahead.
DemandCaster offers best-in-class S&OP software as well as an equally effective Supply Chain Planning Software Suite to help companies manage supply chains. With robust “what-if” scenario planning, ABC analysis, multi-echelon demand forecasts and more precise forecasts driven by real-time data, these platforms can optimize your supply chain to provide leaner, more effective management in uncertain times.