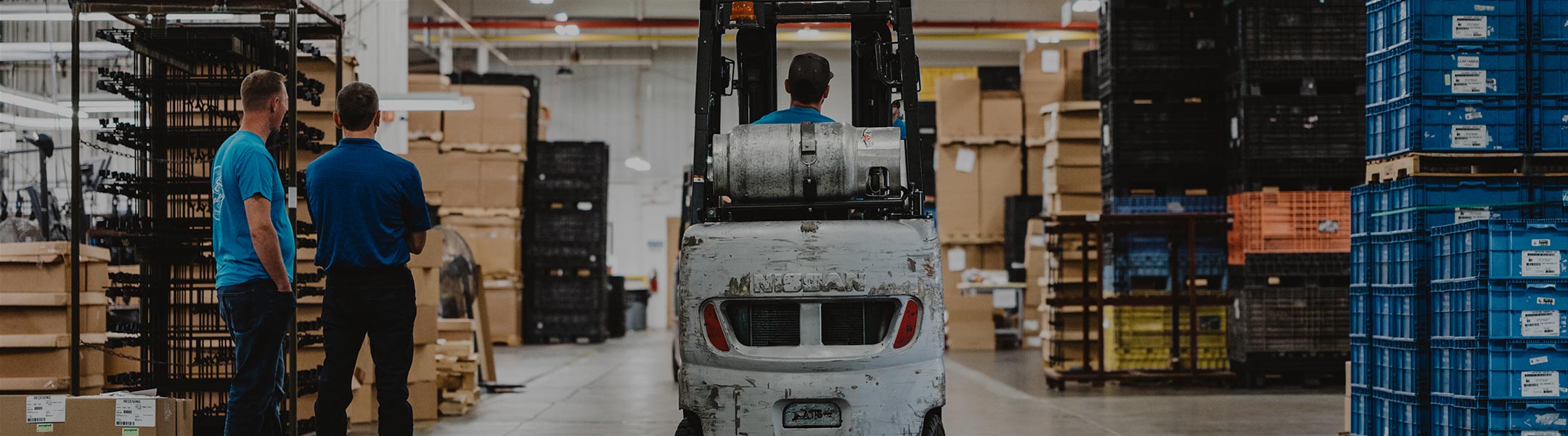
Get your copy of the 7th Annual State of Smart Manufacturing and hear from 300+ manufacturers in this new survey report!
For a monthly digest of expert insights, data points, and tips like the ones in this article.
We define quality as a product or service that meets and exceeds customers’ expectations on a consistent basis.
Accomplishing this in aerospace and defense — an industry known for its complexity and depth of compliance and quality management requirements — is an ongoing challenge.
A&D manufacturers are continually working to stay in compliance with AS9100 Rev. C requirements, which define traceability, document control and record storage, in addition to International Traffic in Arms Regulations (ITAR) requirements. Auditability and transparency are deliberately designed into many U.S. Department of Defense standards, including the Defense Contract Audit Agency (DCAA) and Truth in Negotiations Act (TINA).
However, there is some good news: Compliance and transparency can be used to reduce user and system error as well as operating risk, all while maintaining business agility — and, most importantly, driving the new product development and introduction process.
It is common to find many aerospace manufacturers relying on new products for 60 percent or more of their revenue in any given fiscal year. When technological change is factored in, the urgency to use compliance as a catalyst of greater competitive business process performance becomes clear.
At Plex, we’ve seen 10 strategies emerge that are particularly well-suited for creating a catalyst for continual process improvement and competitiveness:
1. Compliance and quality management strategies have the best chance of succeeding when there is a single system of record that galvanizes a manufacturer around a common and shared set of quality objectives. Consolidating multiple on-premise legacy ERP systems with a single, unified cloud ERP system that can scale with the business makes greater economic sense than attempting to integrate multiple legacy ERP systems together. This is especially true in the areas of AS9100 and ITAR compliance.
2. According to Aberdeen Group, legacy ERP systems that were customized and installed for a different version of a given aerospace or defense business model deliver correct data only 30 percent of the time or less. Manufacturers who choose to consolidate or replace these systems free up their production managers and manufacturing teams, helping them become strategists instead of data collectors.
3. A&D manufacturers get the most value from their compliance and quality management system when they take into account supplier quality levels and tooling requirements, along with creating Corrective Action/Preventative Action (CAPA) workflows for a cycle of continuous improvement. Complaints from customers, process variations and production inconsistencies need to be managed using the CAPA process.
4. Quality is a team sport, and the best A&D companies excel at creating and managing a set of metrics that measure collaboration, compliance and quality on an ongoing basis. For any quality management system to succeed, it must take into account the specific requirements for regulatory compliance — very clear performance metrics for quality control and a series of manufacturing and operations metrics that report on both quality and collaboration. Compliance, quality control and manufacturing operations all need to be synchronized in the objectives set for a manufacturer’s compliance and quality management system.
5. The highest-performing aerospace quality management systems connect manufacturing operations from the shop floor to the top floor with metrics that translate project performance to financial results. It is possible to know how distributed order management performance and the recent investment in production systems’ calibration systems impact the bottom line when compliance is used as the catalyst for driving this level of accountability. Compliance becomes the driving force for unifying the shop floor to the top floor in the highest-performing A&D manufacturers today.
6. Manufacturing compliance and quality management system needs to track and report variability reduction, cycle time reduction and risk mitigation across each manufacturing plant or location. These three factors are foundational to achieving compliance and quality management objectives.
7. Taking a customer-centric approach to defining strategies for attaining compliance with AS9100, DCAA, ITAR, TINA and ISO standards (ISO 9001, ISO 14001 and ISO/IEC 18000) more efficiently measures their financial contributions. Using a customer- and revenue-driven approach also helps justify having a senior executive lead these initiatives, further increasing their probability of success.
8. Publishing supplier audits and the data they produce on a corporate intranet site, with a series of analytics and metrics included, helps track trends in their performance over time. Studies by Gartner, IDC and others show supplier audits are the single most valuable benefit of having an enterprise compliance and quality management system in place.
9. Implementing a Non-Conformance/Corrective Action (NC/CA) program to evaluate suppliers’ inbound orders often reduces defective raw materials shipments and wrong orders, and minimizes late deliveries.NC/CA data shared across a cloud-based platform with suppliers also leads to benchmarking and corrective action strategies based on agreed-upon improvement goals.
10. Defining objectives for process cost, transaction time to process reductions, and greater accuracy of transaction volumes is at the center of many aerospace quality management programs today. Making continual process improvements measurable provides any manufacturer with a very clear view of how their compliance efforts are reducing the cost of quality and driving profits.
Bottom line: The compliance requirements A&D manufacturers face need to be seen as a catalyst for continual process improvement and a call to greater competitiveness.
For Further Reading:
Looking under the hood at Toyota – part 2. (2010). Business and the Environment, 21(6), 4-5.
Dyer, J.H., & Nobeoka, K. (2000). Creating and managing a high-performance knowledge-sharing network: The Toyota case. Strategic Management Journal, 21(3), 345-367.
Miller, P.E., & McKinney, M. M. (1998). Analyzing effects of regulatory compliance in manufacturing. Industrial Management + Data Systems, 98(3), 108-112.
Psomas, E.L., Fotopoulos, C. V., & Kafetzopoulos, D. P. (2011). Core process management practices, quality tools and quality improvement in ISO 9001 certified manufacturing companies. Business Process Management Journal, 17(3), 437-460.
Rosenberg, L., & Weiss, R. (2002). Global pharmaceutical insights: Manufacturing compliance emerges as a key topic in boardrooms. Chemical Market Reporter, 262(14), 21-24.
Vinhais, J. (2004). Leaning Into Six Sigma. Medical Design Technology, 8(11), 32-34.