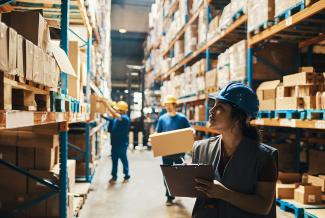
Get your copy of the 7th Annual State of Smart Manufacturing and hear from 300+ manufacturers in this new survey report!
Experiencing a recall can feel as daunting as an IRS audit. But when a problem emerges, there are proactive steps that can immediately help with investigation and mitigation.
Keeping records of inventory receipts and issues—a basic feature you’ll find in any ERP platform—will only take you so far. To fully understand the extent of a problem so you can respond proactively, you’ll also need complete records of all activity, movement, tests, measurements, and plant floor data. And all this information must be logically tied together in one digital system of record.
Even when the OEM responsible for the design, material specification, and source has examined and approved all processes and quality measurements, your cooperation is essential. To facilitate root cause analysis and mitigation, you must be able to clearly identify all provenance and relationships. This process can be annoying and time consuming—and it still may not yield definitive information. Every gap in your data will lengthen the recall and multiply its costs for everyone.
Your best way forward is to focus on recordkeeping discipline by using data management tools that track all data from the shop floor to the top floor and make it accessible for full traceability. Most manufacturing ERP systems don’t go far enough in supporting the kind of analysis you need to get through a recall investigation smoothly and efficiently. If you’re reading this, then your ERP probably falls into that category.
Together, these two capabilities provide a proactive approach to traceability that we call active compliance.
Most ERP systems only offer passive compliance, meaning they’re capable of recording transactional information. They can capture lot identification from the point of receiving, through production, and on to shipping, and maintain a record that you can query from the raw material lot forward or the customer order backward. This may be a huge improvement over your current capabilities, but it’s not enough. Using this approach, you still can’t prevent full-scale problems—you can only find them after they’ve occurred.
In active compliance, your system gives you visibility into, and control over, all your activities in real time. It won’t let anyone start a job if the wrong material or lot has been delivered to the workstation. At the same time, it makes sure the operator is properly certified to run the equipment.
A system with active compliance displays instructions to ensure the operator follows the right steps, enforces any required tests or inspections, monitors the calibration of the test equipment, and stops the job if the process goes outside the control limits. Best of all, it captures information directly from the equipment to maximize accuracy and prevent any impact on operator productivity.
When a part is identified as defective, the OEM will want to know its full history, including who produced it, the materials used, their source, details of the production process, and any measurements that were taken. Creating and maintaining that database should be relatively straightforward, as long as your ERP system is fully integrated and capable of capturing and linking the data properly.
Inventory movement data is only the beginning. You must also capture and integrate each inventory receipt and issue, source, date and time, lot identification, operator, location, and enough detail to link to certification, test results, and provenance that may be in another database. Additionally, production records should include similar information for all parts and materials used, including details on every process step such as equipment used, specifications, version, work instructions followed, reporting parameters, quality measurements, and so on.
Once you’ve collected and stored your data, focus on accessibility. The OEM will want to see the full history of each part and everything that went into it. You’ll need to provide evidence that you followed all procedures and completed all tests and measurements—and show the results.
This information may or may not be available in your current system. How difficult will it be to gather the documentation you need? How auditable are these records? Can you prove that they’re complete and accurate? Active compliance enables you to answer these questions positively and confidently.
Suppose a part is found to be defective. The OEM will use its records to confirm that the part, materials, and process were properly tested and certified. Next, the OEM will expect you to confirm that you followed the specifications, used materials that were in compliance, and can clearly isolate the specific parts affected by any problems that were detected.
That last requirement is critical to limiting the extent of the recall, but it may involve backward and forward traceability. Huge quantities of products are often recalled simply because the manufacturer couldn’t confidently determine whether a defective part was in the final product.
An additional benefit of this kind of traceability is realizing that a defective material or part found in one OEM’s investigation may also have been used in another customer’s products. You can then proactively inform the other customer of the potential problem and help them avoid their own recall—or at least limit the damage.
You’re eager to provide the information needed to bring any investigation or recall to a speedy conclusion. But searching through computer transaction records, combining them with information kept in spreadsheets and filing cabinets, and cross-checking records in other computer systems (such as MES, quality, or procurement) can be difficult and costly.
Take a proactive approach by combining all required data and history in a single digital system of record and using tools that are designed to trace relationships and provenance. This doesn’t just happen—it must be thought out and planned, then built and maintained with traceability in mind.
We know this because the Plex Smart Manufacturing Platform was born on the automotive shop floor as a single source of truth. Combine a powerful ERP with MES functionality and active compliance tools, and it’s easy to see why our clients have enjoyed the most robust traceability on the market. By relying on Plex, automotive suppliers like you have consistently minimized the time, effort, risk, and cost associated with recalls while increasing agility and quality. Are you ready to join them?