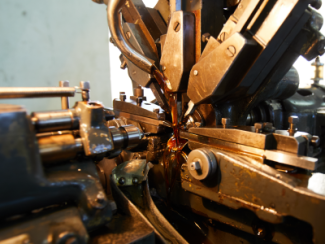
Get your copy of the 7th Annual State of Smart Manufacturing and hear from 300+ manufacturers in this new survey report!
The Electric Materials Company provides services to a wide array of industries around the world. With 110 years in business, the company has made a name for itself as a global leader in commutator manufacturing. The original product lines included street railway repair parts and drop forgings. Over the years, EMC expanded to a state-of-the-art, 420,000 square foot plant in North East, Pennsylvania, with advanced product lines and facilities. The team strives for continuous improvement in today’s highly competitive markets, making them a reliable and consistent partner for their customers.
With sustainable growth in mind, EMC realized that the existing system in place, implemented in 1995, no longer supported the company’s development goals. They faced significant challenges due to an outdated system that was never fully utilized, including a lack of digitization, limited plant floor visibility, and insufficient control of materials and finished goods. Trustworthy data was also hard to obtain, leaving the team heavily reliant on paper-based processes.
As the Electric Materials team looked to modernize operations, they recognized a need for a more streamlined solution to address their unique business needs. They aimed to improve overall operational efficiencies, increase access to data and reports, and find a solution that would be user-friendly for everyone, both internal and external.
The initial evaluation process was initiated by upper management and later extended to include the company’s power users, emphasizing a team-centric mentality. The decision-making process stemmed from the desire to find a solution that would address business challenges related to yield loss, remelt, actual cost tracking, and more. Additionally, there was emphasis on the adoption of a cloud-based platform following a corporate mandate that would allow the company to further align with broad organizational goals.
Plex emerged as a leading candidate, both due to its cloud-based nature and user-friendly implementation style. Upon investigation, Plex’s test environment was an additional perk as it provided the team with invaluable resources in the transition process. One EMC team member had prior knowledge of the platform and recommended Plex as a potential solution early in the evaluation process. By ultimately choosing Plex, the company was able to address immediate needs while simultaneously establishing a foundation for future growth and expansion.
The Plex implementation at the Electric Materials Company was carefully planned, marking a major transformation in the company’s operations. Officially kicking off in January 2023, the implementation involved both leadership and key users throughout the entire process. This strategy allowed team members to gain a better understanding of Plex while also enabling them to better support other employees as the go-live date neared.
EMC took a structured approach to the implementation, with Plex providing “homework” assignments and hands-on assistance. The Plex team also conducted regular follow-ups through the process, further reinforcing the training and ensuring progress at every stage. Additionally, leadership emphasized the importance of consistency during the implementation process, encouraging everyone on the team to learn and effectively use the platform. Operators on the shop floor were quick to adapt to Plex, further exemplifying the effectiveness of Plex’s structured training coupled with support from upper management.
When a company migrates from one solution to another, they usually have existing data and infrastructure to transition with. EMC, however, decided to revamp their engineering operations alongside their implementation. This made for a unique implementation process; while it added another challenge to creatively approach during the migration, starting from scratch within Plex offered EMC the ability to tap into the full potential of Plex. Within only six weeks of going live, Electric Materials Company had returned to business as usual—after three months the plant was fully operational on Plex, matching productivity levels of their previous system and more. Additionally, the company went paperless on the production floor overnight with overwhelming success.
The implementation spanned approximately 15 months and proved the adaptability of the EMC team. While the cloud-based platform was new to them, the team experienced a smooth transition and Plex’s compatibility with the existing technical infrastructure was witnessed in real-time. The Electric Materials Company continues to integrate external systems into Plex today, further demonstrating the success of the project.
Since completing the Plex adoption, the Electric Materials Company has experienced a significant transformation. From streamlined processes to enhanced visibility, the improvements seen have been both impactful and timely. Prior to the implementation, the team spent a considerable amount of time manually compiling reports and tracking finances—a process that was both time-consuming and prone to human error. Now with Plex, the same data is more easily accessible, and the team has seen a drastic reduction in the need for IT support.
Alongside time savings, EMC has also seen cleaner, more accurate data with Plex. Becky Ramsdell, Electric Materials Company CFO, praised the system for its impact on inventory management: “We’ve never had such clean data. We fly through our cycle counts on a weekly basis and our month-end counts within hours.”
Real-time data has also been particularly transformative within production control and inventory management. The ability to measure key performance indicators (KPIs) that were previously inaccessible has allowed the team to improve on-time deliveries, increasing them from around 40-50% to 60-70%. This boost is crucial for the company as it ships between 350,000 and 400,000 pounds of product each month and processes between 650,000 and 700,000. Most of this volume flows through the EMC press, making Plex’s ability to provide clear visibility into operations even more impactful. This will only continue to improve as it gets into the hands of more supervisors and management on the shop floor. Additionally, with everyone—from operators to upper management—viewing the same real-time data, employees no longer need to hunt for paperwork or rely on outdated information to stay informed.
The newfound ability to track issues and improvements through support tickets has also been a major player in the team’s success with Plex, streamlining collaboration between the shop floor and the office. Employees are now more engaged and proactive, knowing that they can easily track items that need attention. EMC has also seen improvements to its onboarding experience, with HR integrating its processes into Plex. The role-based security has made the setup of new users more efficient, further improving operational efficiency.
“From an end user standpoint, the system [Plex] is so easy to use once people are trained properly, it’s less IT support and it’s in the cloud,” stated Patricia Schwarz, IT and Continuous Improvement Manager. “It’s amazing once you have everything in place, we know it’s going to work consistently for every employee as needed, 24/7.”
On the financial side of business, Plex has helped to significantly reduce the time required to access invoices, purchase orders, and inventory data. What used to be a very manual process is now streamlined, allowing the accounting team to resolve issues in real-time. “Before Plex, I would spend hours pulling formatting data for reporting. Now with Plex, I can extract data easily and use v-lookups to link data from multiple reports. I can spend more time analyzing data rather than formatting,” noted Jessica Duda, Accounting Manager.
Despite the significant progress already made, the full potential of Plex at the Electric Materials Company has not yet been realized. MES A&O is currently being implemented into EMC’s automated plating line, and the team is looking forward to making more informed decisions and increasing the pace at which the department runs. Additionally, EMC is already planning what’s next, including further integration of the Engineering and Quality Assurance departments. Looking ahead, team members are excited about the continued expansion of Plex’s functionalities and its ability to drive even greater productivity and collaboration across the organization.
Based in North East, Pennsylvania, The Electric Materials Company (EMC) has been entrepreneurially owned since 1915. The company manufactures high quality copper extrusions, forgings, electrical commutators, and more. With over 40 copper alloys, EMC can design, engineer, and manufacture products from start to finish in house. The 420,000 square foot plant serves a wide variety of industries from transportation and mining to industrial and nuclear.
Industry: Copper Mill and Component Manufacturer
Location: North East, PA