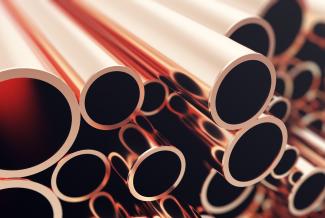
Get your copy of the 7th Annual State of Smart Manufacturing and hear from 300+ manufacturers in this new survey report!
Arrow Fabricated Tubing is a leading supplier of fabricated copper, aluminum, and stainless-steel products to the HVAC and Automotive industry, among others. After being formed in 1978 as a metal service center, Arrow evolved and began the production of copper return bends for the HVAC industry in 1985. Seven years later, they expanded their product line to include fabricated copper assemblies and components. For the past 23 years, Arrow’s exclusive focus has been on the fabricated copper and aluminum tube components market, making them the most extensive provider in North America.
With the access to data on production, quality, performance by specific part, by area, and more, you can manage how you are performing in real time. Thus you don’t have to spend excessive amounts of time analyzing; you can see what you need to do...and do it.”
With increasing success and a broadening customer base, Arrow recognized a need to better integrate their data and provide access and visibility internally and externally. They had become heavily reliant on manual paper documentation and one software system that was not meeting their growing needs. Additionally, there was an increasing desire for better quality data to drive continuous improvement and provide customers with a clearer understanding of their quality defects.
As a result of paper-based constraints, Arrow became overly expedite-oriented, resulting in higher costs and slowed processes on the shop floor. Although they had access to data when they started or finished a job, manual intervention on the shop floor was still required when gauging improvement on any works in progress. Over time, this impacted Arrow’s productivity, forcing employees to locate orders in real time and minimizing the opportunity for proactive action. These inefficiencies left room for human error and wasted resources, leading Arrow to search for an all-encompassing, digitized manufacturing execution system (MES).
Arrow’s most immediate priority was to implement a robust MES with a quality focus that would digitize their environment and help increase throughput with error-proofed setups, quality checks, production recording, and scrap reason reporting. Helping ensure accurate production performance metrics by digitally automating tasks like recording production or scrap was paramount.
The company narrowed in on cloud-based solutions to alleviate investment in infrastructure that is typically required with on-premise systems. Frank Freeman, Senior Manager of Sales and Operations Planning and Manufacturing Systems for Arrow, stated, “we had a vision from our leadership and we spent a lot of time looking to find the right partner in helping us put that together. Plex was the only system that we saw that had the ability to integrate quality data along with all the production data and the massive data that manufacturers collect.”
Plex was launched in December of 2015. With Arrow’s President and senior leadership as big supporters, the organizational acceptance was strong. Freeman stated, “Once we implemented, we were able to pull data together extremely quickly. The thing about Plex is that you’re collecting historical data with every keystroke.”
Moving from paper processes to Plex MES helped empower Arrow’s workforce right off the bat. For example, access to real-time data gave Arrow employees the opportunity to manage their own performance without spending any extra time analyzing that data. They can now easily see what needs to be changed and adjust accordingly without negatively impacting the day-to-day workflow. Employees create work instructions with attachments loaded directly within them. These can then be accessed by individual employees throughout the workday, positively impacting workflow and ensuring that everyone is on the same page.
With Plex, Arrow was also able to quickly serve their customers with more integrated data and better identify where their efforts and resources would be best utilized. Freeman states, “with the access to data on production, quality, performance by specific part, by area, and more, you can manage how you are performing in real time. Thus you don’t have to spend excessive amounts of time analyzing; you can see what you need to do...and do it.”
Arrow has achieved notable results since their Plex implementation. One monumental change has been their ability to manage inventory. Prior to Plex, Arrow was spending much of their time making inventory and moving it to the shipping dock. However, this process often led to the loss of goods prior to it reaching the finished goods warehouse. Plex allows Arrow to barcode everything through their facility. From the time of implementation on, locations and inventory were tracked from production to distribution, giving Arrow peace of mind and increasing inventory accuracy. Freeman stated, “We went from not very good inventory accuracy in the finished goods category to about 98, touching 99 percent accuracy on a regular basis.”
Plex has also changed how Arrow looks at their backlog. Through development of targeted reporting, they can now provide daily updates to the users who need them. This allows employees to view clear-cut reports daily and use those to better perform in their day-to-day workflow. Plex’s digital checksheets system is also being used to correct any quality issues that may arise in production. This reduces quality costs and risks through close integration with product specifications.
Arrow also implemented the Plex DemandCaster Supply Chain Planning solution, which allows them to use the history that they had collected with Plex to help generate future forecasts. With customers ranging from those with solid forecasting systems to those who weren’t robust in that category, DemandCaster allows Arrow to create a long-term plan for themselves and plan out their raw material flows. DemandCaster’s mature planning and forecasting capabilities help differentiate Arrow’s business and support accelerated growth.
Plex has given Arrow the opportunity to reach their full potential. The overall improvement in company-wide learning post implementation has not only increased confidence but also provided employees with skills that can be used every day. Going from a team with limited computer skills to a collective increase in system usage and expertise has given Arrow a leg up in the digital manufacturing world. With high value placed on customer relationships and world-class quality, Arrow has been able to provide customers with more feedback, increasing relationship building and ensuring continuity with customers.
“Plex was the only system that we saw that had the ability to integrate quality data along with all the production data and the massive data that manufacturers collect.”
– Frank Freeman, Senior Manager of Sales and Operations Planning and Manufacturing Systems
Arrow Fabricated Tubing is a leading supplier of aluminum fabricated products to the HVAC industry since 1985, including return bends, crossovers, and interconnected tubing. With 45 years of experience, Arrow provides high volume manufacturing capabilities and the most extensive line of copper and aluminum tubing products in North America.
Industry: HVAC
Location: Garland, TX