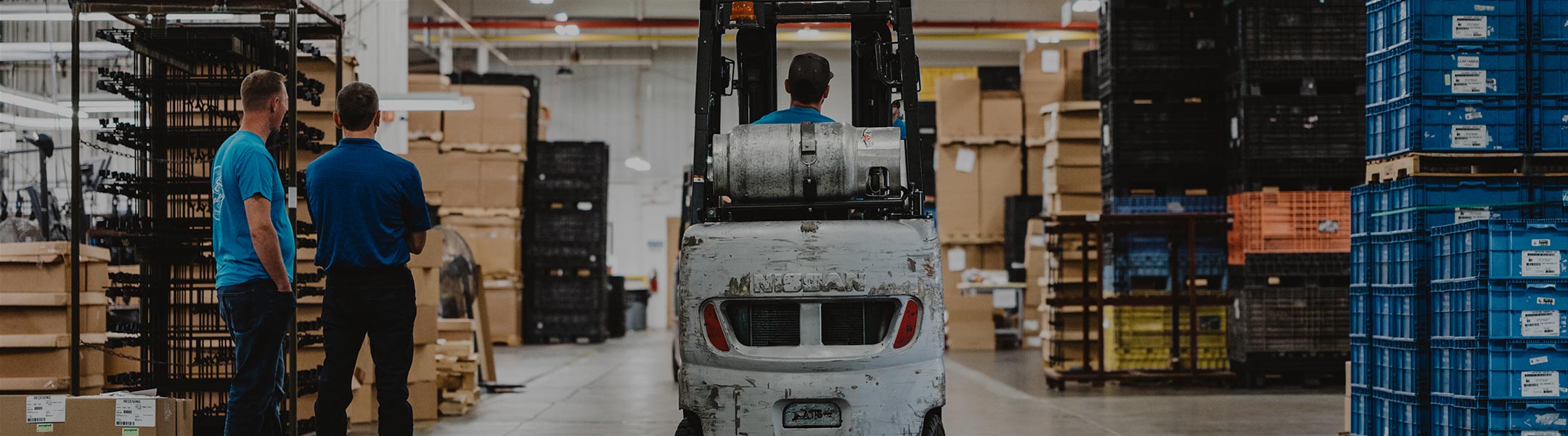
Get your copy of the 7th Annual State of Smart Manufacturing and hear from 300+ manufacturers in this new survey report!
For a monthly digest of expert insights, data points, and tips like the ones in this article.
The Precision Metalforming Association (PMA) hosted the Metal Stamping Technology Conference recently in Nashville, Tennessee. A dynamic, thoughtful, and somewhat frustrated group gathered to talk through the state of manufacturing, the biggest challenges, and how we can begin to address those challenges with technology after we’ve started taking care of people and processes first.
This last part is where a lot of this technology conference focused because‐as we all should know‐technology doesn’t do a whole lot without the power of people guided by processes and vice versa.
Laurie Harbour, President & CEO of Harbour Results, Inc., led off the conference with a compelling and context-setting presentation full of stats showing the state of the industry. Of the many stats she rattled off, her research showed that 58% of PMA members performed as expected in 2022 and almost half (45%) expected to increase revenue by over 5% in 2023. But costs are rising, labor remains a pressing issue, and quality is suffering as result. These high-level themes align with recent research from Rockwell Automation’s forthcoming 8th Annual State of Smart Manufacturing Report, which highlights the stress that quality is putting on organizations.
The connection of labor volatility to quality is clear. Shortages for some, a revolving door of workers for others, and retiring workers for still others are all impacting consistency with product processes and are lowering the quality output that is so important to all organizations. When thinking about ways to address these many issues, it starts with getting back to basics by focusing on people and processes and thoughtfully adopting technology to account for your existing conditions.
As technology continues to evolve with lower barriers to entry, it’s clear that some of these issues can be addressed with a software solution like a Quality Management System (QMS) or Manufacturing Execution System (MES) that can reduce human error by automating data entry and producing alarms and stopping a process if quality and safety procedures or process instructions are not followed.
Harbour also touched on the evolving turmoil that the industry faces‐from pandemic to demand fluctuations and supply chain shortages to the energy crisis, inflation, interest rates, and labor shortages. Labor challenges may never change because, as Will Healy III pointed out in his presentation to close out the conference, the workforce has changed. Next generation workers have different wants and needs out of a role and with the competition from so many other organizations out there, including his example of Wendy’s offering a 401k, tuition reimbursement, free meals, and paid time off, the competition for labor is fierce.
Healy’s presentation also called out the power of purpose for millennial and Gen Z workers and their basic expectations for an organization, particularly considering that they are digital natives that demand a workplace with modern technology. Integrating Virtual Reality (VE) and Augmented Reality (AR) technology with this tech-savvy workforce to attract talent, accelerate training and onboarding, and improve workforce efficiency is a perfect fit on many fronts.
Earlier in the day, Dan Krug, Vice President, Talent at Nucor Corporation, presented an emotive and thoughtful keynote aligned‐but expanding upon‐the message, “Inclusion and Diversity in the Manufacturing Workplace,” which was full of personal stories that accentuated the impact that a culture of inclusion has on your workforce, which in turn impacts innovation and productivity. This powerful presentation accentuated the changes happening in the industry and the now mainstream importance of having an ESG and sustainability policy.
While there were numerous conversations about changes and disruption to the industry, one of the most powerful examples was the change that new technologies driven by electric vehicles are bringing to the market. Government regulations, sustainability focus, and the Inflation Reduction Act for the U.S. are all the driving forces behind this speedy investment into EVs, but there are a number of advantages to automotive manufacturers themselves as well. More modular, simplified designs, utilization of common components, and reduction in stamped and assembled parts will bring higher efficiencies and lower costs to manufacturers as EV volumes increase. Because of the rapid shift to EV investment, we are experiencing the greatest infusion of capital for the automotive industry during our lifetimes. Autonomous vehicles in 2030+ will likely further accelerate this EV shift since it’s likely those models will be built on EV platforms.
Many of the speakers touched on the importance of fiscal responsibility as a key to success, but to achieve this success and build flexibility, adaptability, and resiliency within your operations, it’s important to continue strategic investments for the business‐particularly through new technology‐to position your company in the best possible way for whatever is coming next. Almost every speaker also drove home the point of taking advantage of a downturn for strategically positioning your business through investment to come out stronger on the other side. Each downtown has been a clear lesson in best practices to grow your position and leverage downturns to come out competitively stronger.
As Harbour, Healy, and others pointed out, if you want to be a top performer‐if you want to be an organization that attracts rather than repels talent‐if you want to position your business for success, you need to tune into your workforce, focus on your process, assemble a team to access your organization’s greatest need, and find a technology that can empower your people to lean into process and build success for your organization today, tomorrow, and every day after.