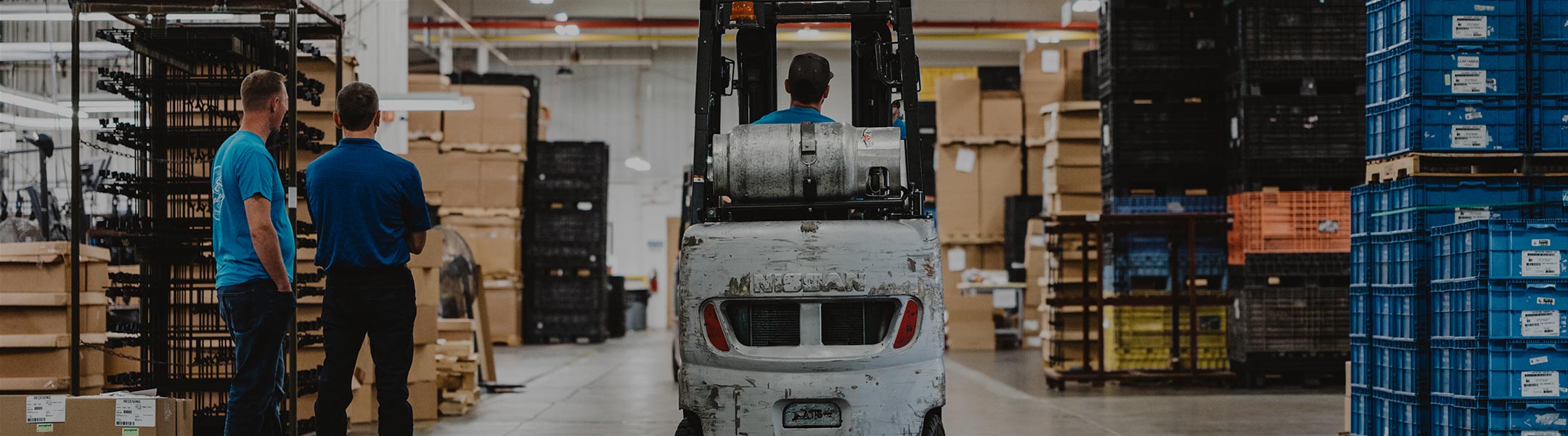
Get your copy of the 7th Annual State of Smart Manufacturing and hear from 300+ manufacturers in this new survey report!
For a monthly digest of expert insights, data points, and tips like the ones in this article.
Complexity in automotive manufacturing is growing. The systems that support your business are likely just as complex—70 percent of manufacturers see an increase in complexity in their organization’s ERP ecosystem due to changing business environments. You need to manage your supply chain and customer demands but the one thing you have the most control over is your own operations.
How do you ensure that your systems can help with that complexity? Are your systems well integrated?
Can your employees get the data they need to do their jobs?
Do you have people dedicated to data analysis to make it happen?
The answer you’ll hear from analysts in the industry is that digital transformation is the key. The consensus is that digital transformation is not only real but inevitable.Top challenges reported by most manufacturers is ensuring consistent quality in products, responsiveness to customer demands, increasing production capacity, getting products to market faster, finding skilled employees, and more. If you go down the road toward digital transformation, will it pay off in helping you deal with these challenges?
1. Controlling the Shop Floor with a Single ERP System
To gain visibility into what is happening on your shop floor, you need to capture the production data—at the manufacturing moment. From barcoding raw materials as they come into the facility and tracking inventory throughout the whole production process, with a single system of record, you gain high resolution inventory traceability so you can reduce inventory and scrap. It’s like a digital paper trail of where everything is and was in your facility to lower the risk of recalls.
Schedules, work instructions, and even error-proofing are available to operators on the shop floor. Integrated quality is applied to manufacturing operations. Control plans drive quality processes. Operators can track tolerances in real time. And everything that happens at the workcenter is captured and made available to the business immediately
2. Connecting the Business
Making production data available to the top floor—business managers—enables visibility for more-informed decisions. In the automotive industry, much of that data is processed through electronic data interchange (EDI) so having that included and integrated within your ERP eliminates the cost of third party providers and streamlines operations. Connecting machines on the shop floor and viewing the data they generate through dashboards on how they are operating helps reduce downtime. Connecting the whole business with data about the business gives you confidence that the information is accurate and up to date.
3. Unlocking Your People Potential
Most IT organizations are focused on keeping the infrastructure running. With the cloud, network, applications, databases, and security management are off-loaded to the cloud provider. Transitioning to the cloud unlocks the true potential of your IT organization by freeing them up for more value-added activities like data analysis. Running your manufacturing business from the cloud also gives you scale to keep up with the ever-increasing pace of technology without increasing your costs.
Imagine replacing system siloes with one, single source of the truth so you don’t have too many people spending too much time juggling too much disparate data. At the end of the day, your expertise is in manufacturing what your customers need—not wrestling with multiple systems just to get visibility into your operations.
For more information, watch the on-demand webinar: 3 Synergies That Drive Success in Automotive Manufacturing.